In-Depth Analysis of 1969 Dodge Charger Body Panels
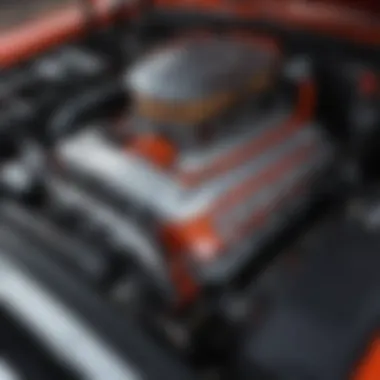
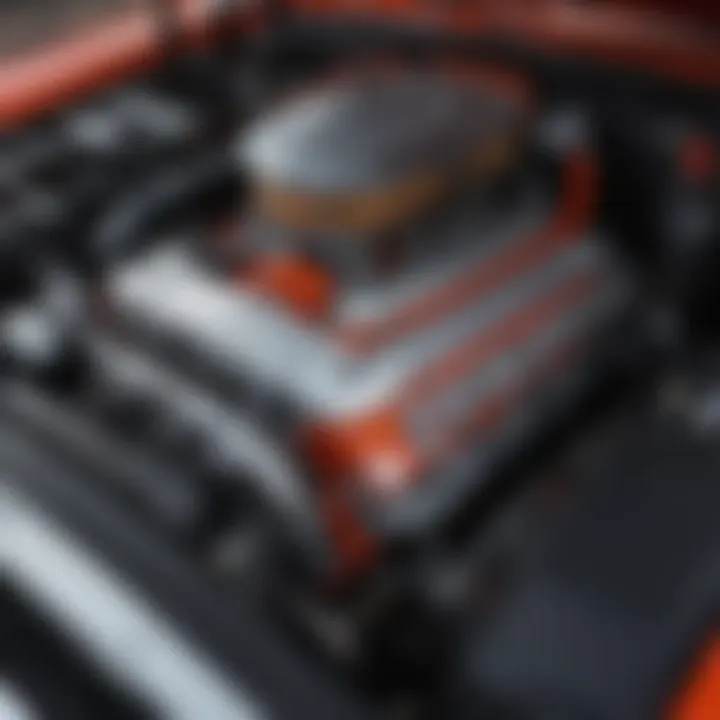
Intro
The 1969 Dodge Charger stands as an emblematic figure in automotive history, marking a significant era in American muscle car design. In contemplating a restoration or customization project, understanding the plethora of options for body panels becomes essential. The body panels not only define the aesthetic of the vehicle but also significantly affect its durability and aftermarket value.
This guide intends to explore the various body panels specific to the 1969 Charger, while emphasizing the importance of quality in both OEM and aftermarket selections. With recent technological advancements in materials and manufacturing methods, ensuring proper adherence to standards during selection is crucial. It serves as more than an explorationโit is a definitive resource for enthusiasts and professionals alike seeking in-depth knowledge and practical guidance in the automotive restoration realm.
Automotive Features and Innovations
In certain respects, understanding the foundational elements of automotive design and technology is paramount for anyone undertaking restoration of a timeless classic like the 1969 Charger. Jus like retention of nostalgic aesthetics also applies to body panels but advancements in manufacturing do let cars leverage newer technologies that modern polarized drivers often demand. This section highlights the general trends associated with automotive features and innovations that are particularly relevant in today's car culture.
Overview of Latest Technologies
New methodologies in body panel production include advancements in material composites, enhanced corrosion resistance, and weight-saving measures without sacrificing integrity. Materials like high-strength steel and aluminum provide effective options that outperform traditional materials in many contexts. Increased use of such innovations guides restorers in making choices that retain functionality while matching the vehicle's original look.
Original Equipment Supplier Significance
When engaging with restoration, understanding the distinction between original equipment manufacturer and aftermarket can have lasting implications. OEM panels maintain the specifications that ensure proper fitment and integrity of the Chargerโs classic structure. This often results in higher costs; however, novices and seasoned restorers alike must weigh cost versus relational value.
Essential Body Panels for Dodge Charger
Critical body panels that one may need for the restoration encompass fenders, doors, windows and roofs. Every panel is engineered to blend seamlessly into the car's overall aesthetic while adhering to both structural and safety performance objectives. Selecting high-quality options is important because a poor choice can compromise both the car's performance and appearance.
Types of Panels Available
- Fenders: Essential for the frontal and rear aspects of the vehicle. Accurate shaping and strength contribute seriously to aesthetics and functionality.
- Doors: They not only define lines but also house essential mechanics and electrical systems. Ensuring a strong seal and alignment keeps interiors intact and functional.
- Hoods and Trunks: Specific types are available for reproduction roles tailored toward weight and power regulations focusing on use of a restoration or customized finishes.
Sourcing and Networking
Engaging with peers, resources and platforms directly impacts the experience when seeking parts or ideological guidance. Utilizing sites like Reddit or automotive community forums provides interaction with individuals on similar projectsเฅค There is value in finding nearby suppliersโindirectly helping local businesses emphasizes cultivating a car culture built on shared resources.
Being well-informed transforms a restoration from a mere task into a fulfilling artistic endeavor that armors a car with passion as much as expertise.
In prioritizing both quality and fitment during selection, one supports longevity and stability of the restoration project, anchoring the journey from the assembly line to today's roads.
Prolusion to Charger Body Panels
The 1969 Dodge Charger is not just a classic car; it signifies an era of bold design and powerful performance in the automotive world. Understanding the body panels of this car is essential for enthusiasts and restoration professionals alike. Body panels, being the exterior components, define the overall aesthetic and structural integrity of the Charger.
Historical Context
In 1969, the automotive industry was experiencing rapid changes. Muscle cars gained immense popularity amidst fierce competition. The design of the Charger reflected these trends, combining speed, design innovation, and power. The panels themselves had to meet specific standards for aesthetics and performance. Characteristics such as size, shape, and material contributed massively to the vehicle's overall appeal.
Dodge styled its body panels to reflect an aggressive stance, evident in the elongated hood and sporty rear meets. Variations in panel production included both durability and cost. Additionally, original production methods often set a standard that aftermarket companies strive to replicate for restoring classic vehicles.
Significance in the Automotive Industry
The significance of body panels extends beyond mere visual appeal. They form the first line of defense against elements and impacts, contributing to a carโs longevity. In the case of the Charger, body panels were engineered for specific aerodynamic properties, aiding in performance. Also, these components play a vital role in safety. During a collision, the body panels absorb and distribute energy, protecting occupants.
In restoration and modification circles, original equipment parts exhibit value due to their craftsmanship. OEM panels demonstrate compliance with authenticity standards and ensure that each restoration retains its historical integrity. This authenticity is a valuable consideration for collectors. Custom body panels provide individuals a chance to modify the vehicle's aesthetics. Yet these alterations often require careful planning to maintain functionality and quality.
Retaining original design elements while incorporating modern materials can significantly enhance the overall performance and longevity of classic cars.
Furthermore, advancements in technology push for improved options in newer alternatives to original designs, further impacting restoration practices. A comprehensive understanding of these historical aspects lays a solid foundation as we dive deeper into the various types of body panels available for this iconic model.
Types of Body Panels
Understanding the Types of Body Panels is essential when it comes to restoring or customizing the 1969 Dodge Charger. Body panels not only define a vehicleโs aesthetic appeal but also influence its structural integrity. Each type of panel serves a distinct purpose, and knowing these intricacies can guide owners in making informed decisions regarding upgrades or replacements.
Fenders
Fenders are critical as they protect the wheel wells from debris and help maintain the vehicle's airflow. The design and fit of fenders are vital for both aesthetics and function. Sourcing original fenders can ensure a proper fit, but there are also aftermarket options. When choosing fenders, car owners typically consider weight, style, and compatibility with other existing body parts.
Hoods
The hood is more than just a cover for the engine; it shapes the entire front profile of the 1969 Dodge Charger. A well-fitted hood enhances airflow, particularly for high-performance models. Many restorers carefully choose aftermarket hoods, as some styles can offer functional vents or heat extractors that original hoods lack. Weight and material type also influence the decision. For example, a lightweight fiberglass hood might be preferred for speed-focused builds.
Doors
Doors play both functional and aesthetic roles on the Charger. They must be aligned correctly to ensure smooth operation and prevent water leaks. The door mechanisms, including latches and hinges, should also be studied. For restorations, it's essential to find doors that match the original specifications precisely since they affect the car's overall build quality and appearance. Considerations on some models even include sound-deadening features within the door panels.
Quarter Panels
Quarter panels encompass a crucial section of the car's body, located at the rear. Their structure provides mounting points for parts like tail lights and offers a base for the rear bumper. Reinforcements within these panels are essential for maintaining a vehicleโs strength. Poorly fitting quarter panels can compromise integrity during collisions. Restoring or replacing them should thus involve careful measurement and consideration of both original specifications and current materials.
Trunks
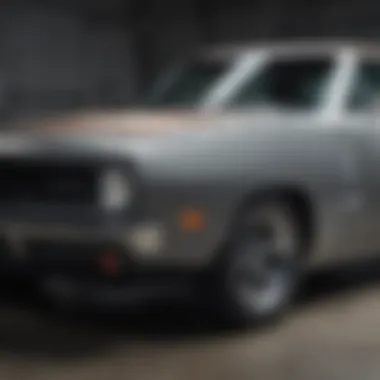
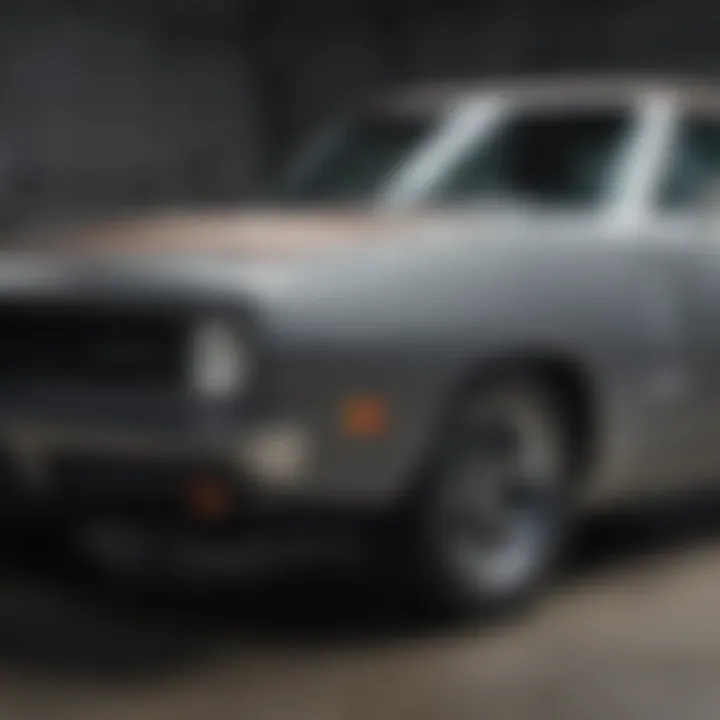
The trunk represents another vital area. When restoring a Charger, a well-designed trunk panel provides access to battery and storage while maintaining a sleek line throughout the rear. Companies sometimes provide trunk floors that align with original specs, which can be significant for a complete restoration. Any deterioration or rust can lead to extensive follow-up work, making it necessary for restorers to consider material quality and compatibility heavily.
Rockers
Rockers are identified along the sides of the car, acting as structural supports and a barrier against harmful dirt or rocks thrown by the tires. Rust is a common problem, so inspecting rockers is essential when restoring. Aftermarket options often exist that mimic OEM parts, and they can be ideal replacements. Quality fit here impacts overall durability and ride quality. As these are accessed often upon entry, their alignment affects daily usability, making informed choices crucial.
In summary, each type of body panel is noteworthy in its functionality and aesthetics. Understanding their roles is not only beneficial for restorations but underlines the significance of precise fitting and quality selection to achieve an authentic 1969 Dodge Charger experience.
Aftermarket Options
The aftermarket options for body panels play a crucial role in the restoration and customization of the 1969 Dodge Charger. While original equipment manufacturer (OEM) parts are revered for their authenticity, the aftermarket industry provides a diverse range of panels that satisfy different needs. Benefits include availability, cost-effectiveness, and innovation in materials and designs. However, several factors should be considered when exploring aftermarket solutions, including supplier reputation, panel quality, and potential longevity of the products.
Overview of Aftermarket Suppliers
Aftermarket suppliers have emerged as a vital source for 1969 Charger enthusiasts who cannot find original panels or prefer modern adaptations. These suppliers vary from small, specialized operations to large companies that offer extensive catalogs of components. When selecting a supplier, it is important to evaluate the following features:
- Experience in the Industry: Longevity in the market suggests reliability and quality.
- Customer Reviews and Feedback: Understanding the experiences of other buyers can inform purchasing decisions.
- Product Range: More variety typically means better chances to find exactly what is needed for a restoration or customization job.
- Return Policies and Guarantees: These policies provide security for ensuring product quality before finalizing the purchase.
Quality and Standards
Quality and standards are paramount when dealing with aftermarket body panels. Unlike OEM parts that follow rigorous standards from manufacturers, aftermarket panels can vary significantly in quality. Some options may be manufactured using high-tech materials, providing enhanced durability, while others may use inferior processes, leading to issues down the line. When assessing quality, consider:
- Material Properties: Ensure that panels are made from robust materials suited to withstand wear over time.
- Manufacturer Standards: Look for suppliers who follow established quality practices. Certifications and warranties can be strong indicators of durability.
- Finish and Prepares: Check for smooth finishes and proper preparations as these will affect how well paint adheres and reflects overall aesthetics.
"Quality materials not only enhance the lifespan of panels but also affect the overall value of a vehicle during resale."
Cost Analysis
Costs associated with aftermarket panels can range widely. Factors influencing prices include:
- Material and Construction: Higher-quality materials usually lead to higher prices due to better manufacturing processes.
- Brand Reputation: Well-known brands often charge a premium, but this could assure better quality.
- Availability and Market Demand: Limited supply items might cost more, especially if they cater to a niche segment.
While searching for aftermarket options, car owners should perform a cost-benefit analysis compared to original components. Sometimes spending slightly more on quality parts leads to yielding more value primarily through durability and fitment that reduces future expenses on repairs.
Understanding this landscape is essential for 1969 Dodge Charger restorers. Future-proofing any installation can result in both aesthetic appeal and functional performance.
Restoration Considerations
Restoration is a key factor for anyone tackling a classic vehicle project, especially with the 1969 Dodge Charger. Attention to detail is not just about aesthetics; it's about ensuring the car retains its value and authenticity. Body panels represent a significant part of a car's structure and its visual appeal. Thus, understanding the specific considerations related to restoration can substantially impact the quality of the final outcome.
Matching Original Specifications
Obtaining body panels that match the original specifications of the 1969 Charger is vital. Not all panels manufactured for the Charger will fit the same way as its original components. When restoring a classic vehicle, the integrity of each component is essential for both performance and historical accuracy. If original sizing, contours, and mounting points are overlooked, it could lead to complications during assembly and affect overall safety and durability.
Many suppliers offer reproduction parts tailored to meet OEM standards. Itโs imperative to verify documentation that asserts these panels meet the necessary specifications. Certain aftermarket dealers have built reputations for quality that match, if not exceed, original standards. This ensures that restorers do not sacrifice quality for availability and maintain authenticity.
Importance of Fit and Finish
The fit and finish of body panels heavily influences the entire restoration appearance. Inconsistent fits can result in visible gaps or misalignment with adjacent panels. Such imperfections detract significantly from the overall look of a project and often hinder the integrity of the car's body structure. Precision during installation is crucial whether you're working with original or reproduction parts.
People must take meticulous care at each junction. If bolts donโt line up, or if the lap between panels appears uneven, it signals potential future maintenance and headaches. Achieving a flush and seamless look requires investments in tools and sometimes patience in adjusting panels to conform.
Paint Compatibility
Achieving a flawless finish also means considering paint compatibility with the chosen panels. Certain materials respond differently to various types of paint, and careful selection is necessary to avoid unforeseen complications. For example, bonds made with fiberglass may react differently with paint solvents. This attachment leads to blistering or peeling over time.
Modern paint technology can nevertheless be an ally for restorers. Use of high-durability clear coats, appropriate primers, or epoxy-based paints addresses necessary compatibility issues. This level of consideration reduces long-term maintenance needs and enhances visual appeal.
As a best practice, always consult material master data sheets provided by paint manufacturers as well as the technical specifications for body panels. This research helps in making educated choices.
"Restoration is not merely a recreation of the past; it is a dedication to preserving history."
Thorough attention to these factors contributes immensely to a successful restoration project. Automotive enthusiasts, students, and professionals must recognize the multifaceted nature of restoration. Striking a balance between quality output and understandable processes reinforces why these considerations must be seen as foundational in any car restoration endeavor.
Material Advancements
In the restoration and customization of the 1969 Dodge Charger, understanding the advancements in materials is crucial. This section reviews the shifts in materials, their impact on longevity, performance, and aesthetic outcome. The earlier steel panels are now often compared to modern replacements made from lightweight and composites. These advancements not only influence the character of the Charger but also its practicality as a reliable vehicle in today's environment.
Steel vs.
Fiberglass
Steel has been the traditional choice for automobile body panels due to its strength and ability to absorb impact. Many enthusiasts argue for the authenticity and weight distribution of steel. However, fiberglass has emerged as a popular alternative. Fiberglass is much lighter, enhancing vehicle performance by improving speed and fuel efficiency.
- Benefits of Fiberglass:
- Challenges with Fiberglass:
- Reduced overall weight
- Increased customization options
- Easier to mold into complex shapes
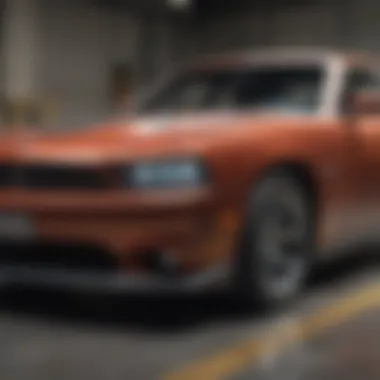
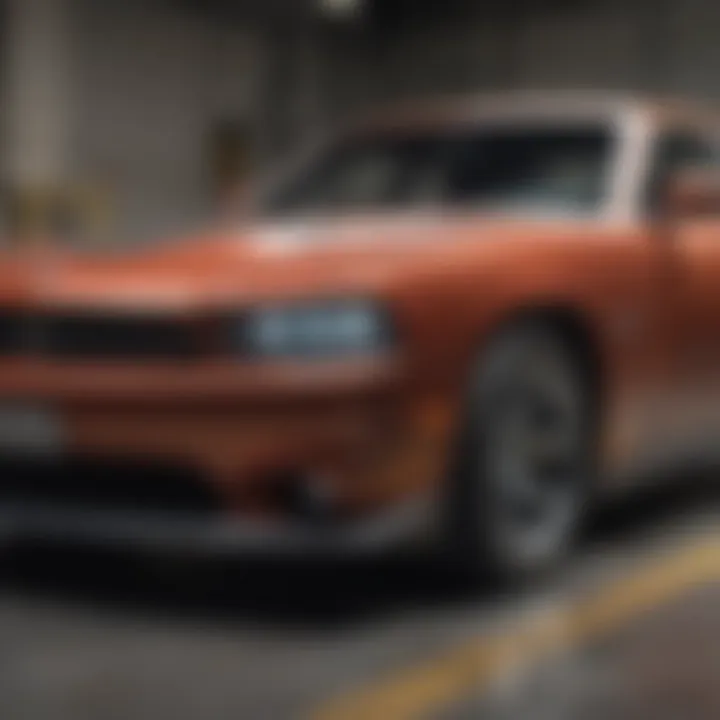
- Traditional look not replicated
- Potential for stress cracking over time
When choosing between the two, one must weigh the significance of originality versus the benefits of performance.
Impact of Lightweight Materials
The introduction of various lightweight materials beyond just fiberglass offers new avenues for the practical aspect of vehicle design. Composites and aluminum alloys are replacing heavy components. The shift towards these materials results in improved handling and efficiency.
The benefits include:
- Enhanced maneuverability
- Reduced strain on engine components
- Better fuel economy preferences
Furthermore, lightweight panels assist in customization, as they can follow modern design trends without compromising the classic look an owner desires.
Corrosion Resistance Technologies
The performance and longevity of body panels largely hinge on how well they resist environmental challenges. Corrosion resistance has witnessed significant development, driven by the goal to extend lifespan and maintain aesthetic appeal. Current coatings include a mix of zinc-based treatments and innovative paint technologies that promote durability.
While steel is susceptible to rust, new techniques enhance its resilience against moisture and salt. In comparison, fiberglass is naturally resistant to corrosion but may fail under significant stress.
- Key Technologies in Corrosion Resistance:
- Advanced galvanization processes
- Alma Pontifex paints that repel moisture
- Nanotechnology-enhanced coatings
Bean counters and hobbyists alike must consider these various aspects when selecting materials, as they envision their Charger either on display at a car show or navigating rainy roads.
This attention to corrosion resistance can discern between a winning restoration project and prolonged maintenance headaches.
Emphasizing future trends in materials over mere historical significance forms the foundation of intelligent customization and restoration strategies. Each automotive enthusiast is encouraged to remain informed about these developments to enhance their vehicles selectively.
Installation Processes
The installation processes for the 1969 Dodge Charger body panels form a crucial part of restoration or customization work. Understanding the steps involved ensures a proper fit, enhances the vehicle's aesthetic appeal, and maximizes durability. This section covers the necessary tools, the step-by-step procedures, and highlights common pitfalls with their solutions.
Required Tools
When undertaking any installation task, having the right tools is essential. For body panel installation, a well-stocked toolkit can significantly improve efficiency and quality. Essential tools include the following:
- Socket set: For removing and securing bolts with various sizes.
- Wrenches: Adjustable or fixed wrenches are necessary for tight spaces.
- Drill: Necessary for fastening new panels, utilizing the appropriate drill bits.
- Rivet gun: Ideal for applying rivets if required.
- Sealant and adhesives: To ensure non-contaminated seams preventing rust.
- Measuring tape: For accurate measurements of panels.
- Jacks and stands: Needed to lift the vehicle safely while working underneath.
These tools yield a systematic workflow, leading to a solid installation of each panel.
Step-by-Step Procedures
Installing body panels is as detailed and requires meticulous attention. Hereโs a simplified procedure:
- Preparation: Ensure that the workspace is clear and that any old or damaged panels are removed.
- Fit Testing: Test fit the new body panel. Align it with existing panels to check the fit's accuracy.
- Cleaning Surfaces: Properly clean contact points on both the vehicle frame and the new panel to promote superior adhesion if using sealant.
- Attachment: Secure the panel using bolts or screws following OEM specifications.
- Final Checks: After all panels are installed, double-check all connections and ensure no tools are left inside. Test the movement of any functional features like doors or hoods.
- Make adjustments as necessary; some panels may require trimming.
- Apply sealant around edges where applicable to prevent moisture ingress.
This detailed approach mitigates mistakes and enhances the longevity of the installation.
Common Pitfalls and Solutions
While installing body panels, several mistakes can crop up, but being aware of these can make your effort more smooth:
- Misalignment: If panels do not align correctly, they often become a stock issue. Measure and adjust frequently before fastening.
- Over-tightening Fasteners: This can warp materials. Always tighten nuts and bolts on new panels gently using specified torque settings.
- Ignoring Rust Prevention: Skipping on sealants leads to corrosion in seams over time. Always use quality sealants for duldurability.
Ensure measurements are accurate at each step of installation.
By identifying potential pitfalls in advance, installers can better maneuver through common challenges while enhancing the final quality assurance of their work. A thoughtful approach can make even complex processes manageable, ensuring the Charger retains its iconic power and look for years to come.
Legal and Regulatory Aspects
The legal and regulatory elements surrounding 1969 Dodge Charger body panels are crucial for both restoration and customization projects. As automotive enthusiasts and professionals dive into working with these classic vehicles, understanding compliance with safety standards and emissions requirements becomes essential. This ensures that the restorations are not only aesthetically appealing but also adhere to legal requirements, providing a safer experience for both drivers and the public.
Compliance with Safety Standards
Compliance with safety standards is paramount when restoring or modifying body panels on a 1969 Charger. Various organizations, such as the National Highway Traffic Safety Administration (NHTSA) in the United States, establish guidelines that automotive restorations must follow.
These regulations are designed to ensure the safety of vehicles on the road, influencing suitable materials, structural integrity, and design features.
For instance, the integrity of crumple zones and seatbelt anchors are very critical. When sourcing or installing new body panels, owners must ensure they meet safety specifications to pass inspection and guarantee the protection of passengers.
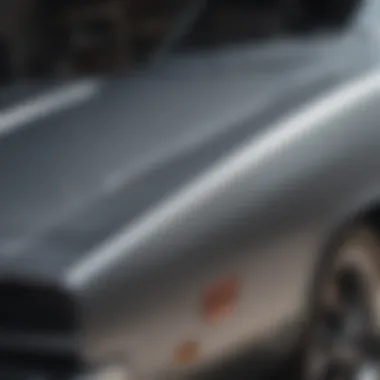
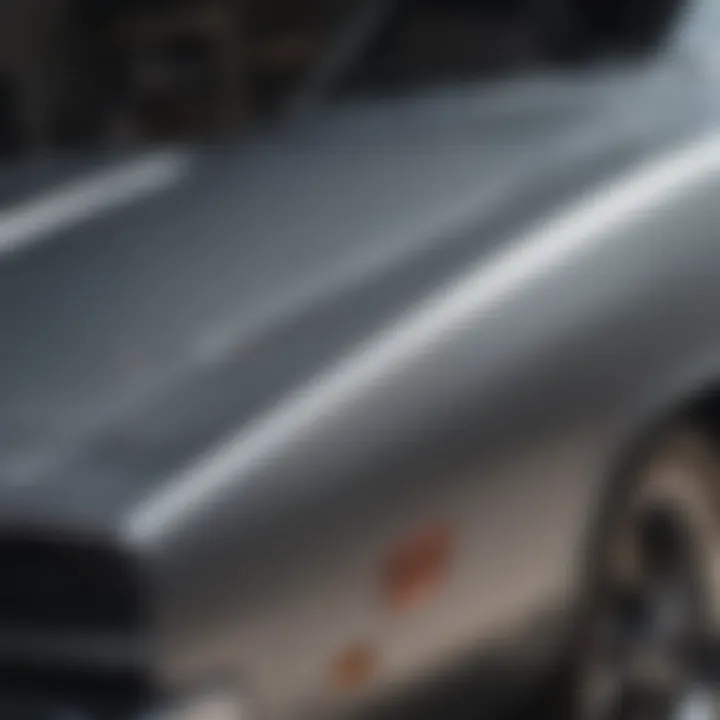
Bu using parts that are certified and approved, restorers maintain the necessary level of safety and may also increase the resale value of their classic car investment. Often, aftermarket suppliers provide documentation regarding compliance, making it easier for car owners to validate that their choices are safe and legal.
Emissions Requirements for Classic Cars
The emissions requirements applicable to classic cars, especially the iconic 1969 Dodge Charger, impose another layer of responsibility for owners and restorers. Regulations aimed at reducing harmful emissions can influence both the type of materials used in body panel replacement and the overall design of the vehicleโs systems.
Federal and state regulations on emissions control cover various aspects. A common requirement includes having systems that manage exhaust harmful emissions, such as catalytic converters and proper exhaust plumbing. When restoring a classic Charger, it might be tempting to use original parts or design aspects that have not changed in decades. However, ignoring updated emissions standards may result in fines, decreases in vehicle value, and potential problems during inspections.
When considering the restoration process, car owners should assess their state emissions laws. Research is crucial using multiple resources to neb extensive knowledge. Some states have stricter requirements than others, affecting what is permissible during restoration.
Expert Recommendations
In the realm of restoring or customizing a 1969 Dodge Charger, making sound decisions is crucial. In this section, we provide expert recommendations that underscore the significance of selecting the right suppliers and contemplating whether to opt for professional installations or DIY approaches. Proper choices can vastly influence the end result of any restoration project, ensuring both quality and satisfaction.ย
Choosing the Right Supplier
The landscape of body panel suppliers can be overwhelming for automotive enthusiasts. It is paramount to assess suppliers based on their reputation, quality of materials, and customer feedback. High-quality panel suppliers provide materials that not only match the original specifications but also align with the standards of durability and performance expected from restoration projects. The right supplier can often mean the difference in whether a restoration stands the test of time or has insurmountable issues down the road.
When researching potential suppliers, consider the following aspects:
- Materials used: Ensure that their panels are made from high-quality materials that enhance durability.
- Certifications: Look for industry certifications that ccan indicate adherence to safety and quality standards.
- Return Policies: Suppliers should offer flexible return options for unmatched or defective panels.
- Expertise: Suppliers with a history in classic car restoration tend to have superior knowledge about specific needs.
It is wise to connect with fellow enthusiasts, keeping an eye on forums and social media for discussions about trusted suppliers.
An informed choice yields considerable long-term benefits.
Professional Installation vs.
DIY
Deciding between professional installation and a DIY approach hinges on several crucial factors. A professional installer has the paid experience and shiny track record, often leading to superior fit and finish. Fractions in fitting can occur without expert knowledge, and missteps can prove costly.
However, DIY can also appeal significantly to the focused enthusiast. Previous projects can provide joy and a strong sense of achievement. Even so, a lack of knowledge could lead to undesirable outcomes. Factors to consider include:
- Skill Level: Are you confident in your mechanical skills? If unsure, professional help may save you concerns down the line.
- Tools and Equipment: Check if you have the right tools at your disposal; professional installs typically need more specialized kit than most homes manage.
- Time Investment: Assess how much time you can devote to the project. Professionals can often complete work quicker and more efficiently.
- Budget: Weigh the costs of hiring a professional setup versus the potential costs of trial-and-error mistakes in DIY installation.
Ultimately, both options come with their advantages and challenges. Choosing wisely can reflect positively on the outcome of your beloved Charger, whether you go professional or handle it personally.
Future Trends in Body Panel Technology
Understanding future trends in body panel technology is essential for those invested in the restoration and customization of classic vehicles, like the 1969 Dodge Charger. As the automotive landscape evolves, the introduction and adaptation of new materials and manufacturing techniques become not only impactful but vital. This article will examine two significant areas within this future trend: sustainable materials and 3D printing applications, both of which offer substantial benefits and considerations for enthusiasts and professionals alike.
Sustainable Materials
The shift toward sustainable materials represents a promising trend in the automotive sector. Traditional materials like steel and aluminum are effective but often lack in environmental accountability. Newer alternatives such as biodegradable composites and recycled materials are now being considered for body panels. These materials significantly reduce the carbon footprint associated with manufacturing.
A key importance of sustainable materials lies in their lower environmental impact. Not only midifying the upfront costs of production wll benefit suppliers, but it resonates well with customers who prefer eco-friendly choices.
A few notable advantages of sustainable materials include:
- Lower environmental impact: Using renewable resources minimizes ecological damage.
- Weight reductions: Many sustainable options reduce vehicle weight, significantly affecting performance and fuel efficiency.
- Regulatory advantages: Compliance with increasingly stringent regulations for vehicle emissions is more feasible with sustainable materials.
As the automotive community watches for widespread adoption, enthusiasts should consider these materials indispensable when embarking on restoration projects.
3D Printing Applications
3D printing technology stands at the intersection of innovative manufacturing processes and automotive restoration. It presents a revolutionary approach to producing body panels. This manufacturing advancement allows for rapid prototyping and the opportunity to create complex shapes and forms that traditional methods cannot easily replicate.
The significance provides a glimpse into its diverse applications, which range from prototyping individual components to producing entire panels tailored to fits. Employing 3D printing reduces waste and significantly cuts down on lead times. These elements contribute to the overall efficiency of automotive restoration, providing a clear user-centric advantage. Furthermore, customizability is dramatically elevated. Affected specific needs can lead to more personalized approaches to restoration.
Some aspects of 3D printing benefits include:
- Cost-efficient small production runs: Enthusiasts or shops can avoid the higher costs of mass production simply tideworks to their runner-new approach.
- Rapid prototyping capabilities: Encourages further custom features made to consumer desires rather than settles with market typicality.
- Waste reduction: Minimal material waste compared to traditional methods fetches zers wastes while decreasing overall production impacts.
In summary, embracing these trends can fundamentally change how restorations are approached, ensuring vehicles like the 1969 Dodge Charger receive technologically advanced upgrades that honor their legacy yet accommodate modern standards and aesthetics.
Finale
The conclusion of this article emphasizes the paramount importance of understanding the body panels of the 1969 Dodge Charger. Recognizing the various components and their implications on restoration and customization significantly affects the success of any automotive project. By delving into these elements, enthusiasts and professionals acquire crucial insights necessary for making informed decisions, whether regarding sourcing original equipment or opting for aftermarket options.
Recap of Important Points
Throughout this examination, we have highlighted several key aspects:
- Types of Body Panels: The identification and differentiation of numerous body panels, such as fenders, hoods, and quarter panels, each with unique attributes and restoration requirements.
- Aftermarket Options and OEM Parts: Discussed the reliability and benefits of specific aftermarket sources against original manufacturers.
- Material Innovations: Illustrated advancements in materials used to make body panels, considering weight reduction and corrosion resistance.
- Installation and User Compliance: Covered essential procedures for installation and adherence to legal safety standards that affect vehicle operation and ownership.
- Restoration Guidelines: Emphasized the importance of matching original specifications that preserved the car's authentic feel and value.
"Understanding both the technical and the practical elements of body panel restoration not only keeps the vehicle's legacy alive but also enhances its overall reliability."
Final Thoughts on Restoration and Customization
Restoration of a 1969 Dodge Charger must not be carried out lightly. Each decision taken during this process, such as panel selection or type of paint, holds the weight of affecting the vehicle's overall performance and appearance. The combination of creativity with methodical approaches will determine the outcome.
Compiling knowledge from expert recommendations and the evolving landscape of materials helps in crafting a charger that meets personal anxieties while staying true to its iconic roots. Essential steps include gathering precise information from reliable suppliers and staying updated with industry practices, all while acknowledging the cultural significance the Charger embodies in automotive history.
In sum, careful consideration of all these aspects will undoubtedly lead to more fulfilling enhancements for both personal passion and automotive historical fidelity.