Exploring the Advantages of Ceramic Coated Pistons
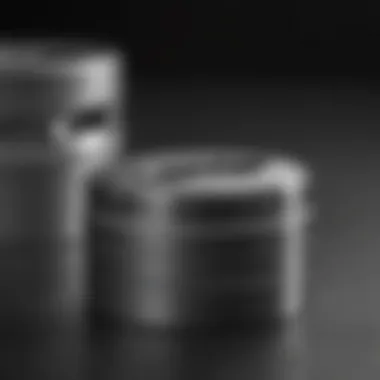
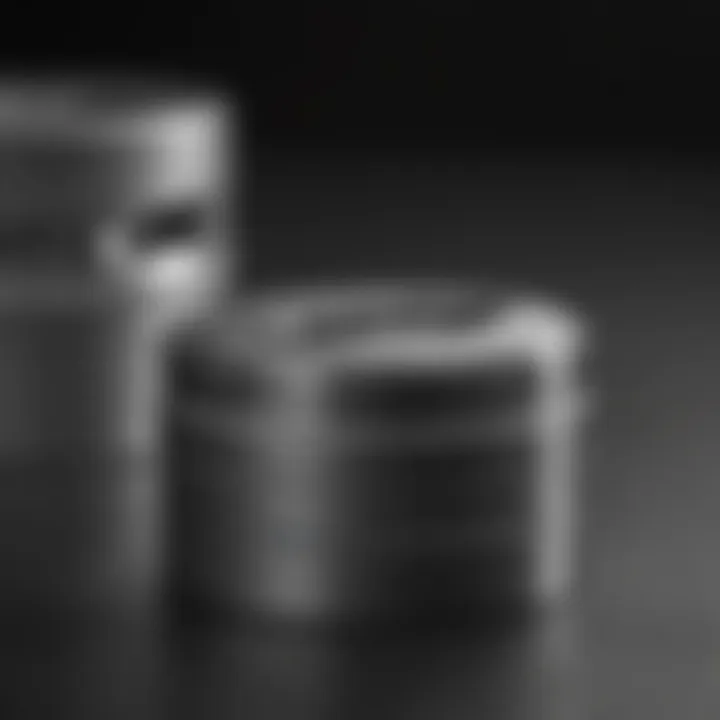
Intro
The advancement of automotive technology has led to significant improvements in engine performance and durability. One of these advancements is the development of ceramic coated pistons. These components provide numerous advantages over traditional pistons, such as enhanced thermal resistance and improved wear properties. This article aims to provide a comprehensive examination of ceramic coated pistons, focusing on their benefits, applications, and technological progress.
Automotive Features and Innovations
As the automotive industry evolves, features and innovations are increasingly integral to achieving efficiency and performance. Ceramic coated pistons represent a step forward in automotive technology. Their ability to withstand high temperatures and pressures makes them ideal for modern engines which require high performance and reliability.
Overview of Latest Technologies
Ceramic coatings have emerged as advanced solutions for improving engine components. The application of plasma spray techniques is common for these coatings, allowing for precise deposition. In addition, the use of zirconia ceramics in these applications permits high resistance to thermal shock, which is valuable in sports and performance vehicles.
In-Depth Look at Electric/Hybrid Vehicles
Electric and hybrid vehicles are also benefiting from the application of ceramic coated pistons. The need for efficiency in energy conversion translates into innovations in piston technologies. Ceramic coatings can reduce friction and improve thermal management, thereby enhancing the overall performance of electric motors.
Analysis of Autonomous Driving Systems
While ceramic coatings relate more closely to engine performance, their contribution to efficiency may indirectly impact autonomous driving systems. Enhanced engine performance allows for better power management and smoother operation of autonomous vehicles.
Evaluation of AI in Automotive Solutions
Artificial intelligence plays a role in optimizing engine performance, including the integration of ceramic coated pistons. AI can monitor engine parameters and provide data for the most effective use of these advanced components, ensuring their performance is maximized.
Trends in Automotive Industry
The automotive landscape is changing. Ceramic coated pistons are part of this shift, influencing various trends in the industry.
Market Analysis and Forecasts
The market for ceramic coated parts is growing, driven by increased demand for high-performance engines. Analysts predict continued growth in this segment as manufacturers seek to enhance engine efficiencies to meet strict emissions regulations.
Electric Vehicle Adoption Rates
With the shift towards electric vehicles, the need for advanced materials like ceramic coatings becomes even more significant. These materials not only enhance efficiency but also extend the life of engine components, making them critical for electric drivetrain development.
Growth of Ride-Sharing and Mobility Solutions
Ride-sharing services are increasing the demand for durable automotive components. Ceramic coated pistons can contribute to longer service intervals, making them attractive for fleet operators who prioritize cost-efficiency.
Consumer Preferences Shifts and Impacts
Consumers are increasingly looking for high-performance vehicles that do not compromise on efficiency. Ceramic coated pistons align with these preferences and represent a valuable addition for manufacturers aiming to satisfy discerning buyers.
Educational Resources
Understanding the significance of ceramic coated pistons requires knowledge of automotive engineering.
Technical Knowledge Base
Established resources, such as en.wikipedia.org, provide a solid foundation for understanding ceramic coatings in automotive applications. Academic articles and journals are also valuable for more in-depth analysis.
Insights Into Automotive Engineering
Courses in automotive engineering frequently cover advanced materials, including ceramics. Students and professionals alike can benefit from staying updated on these innovations.
Certifications and Training Programs
Organizations like sae.org offer training programs focused on modern automotive technologies, preparing individuals for careers in a competitive landscape.
Future Trends in Automotive Education
As the automotive industry evolves, educational institutions are adapting their curricula. Future programs will likely emphasize innovative materials and technologies, including ceramic coatings.
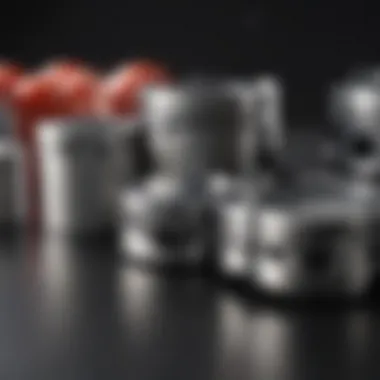
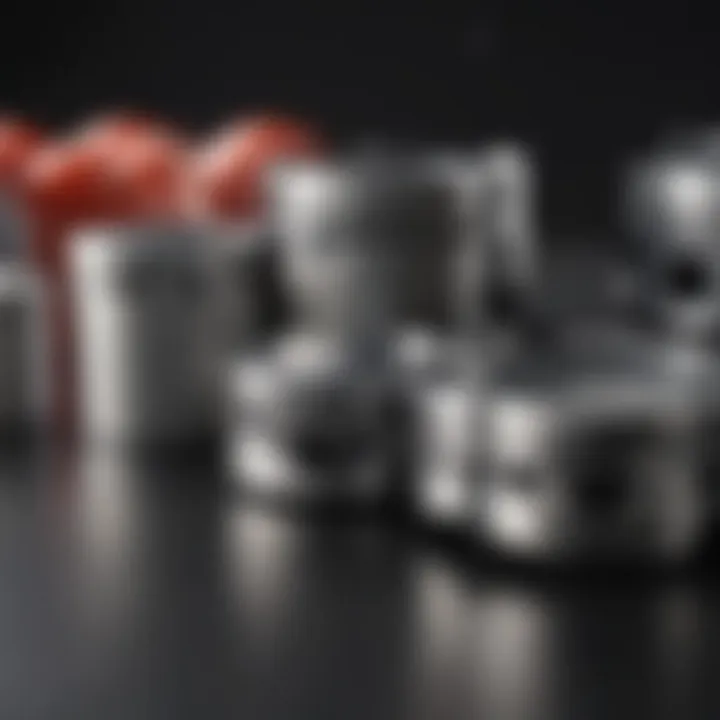
Ceramic coatings are not just a trend; they are a vital innovation that supports the next generation of automotive performance and sustainability.
Foreword to Ceramic Coated Pistons
The automotive industry continually evolves, seeking new methods to enhance engine performance and durability. Ceramic coated pistons have emerged as a significant innovation in this domain. This article will comprehensively examine their introduction, effectiveness, benefits, and broader implications in automotive applications. Understanding this topic is crucial for automotive enthusiasts, car owners, and those directly involved in engine performance optimization.
Definition and Overview
Ceramic coated pistons are pistons that are coated with a layer of ceramic material, which acts as a barrier between the piston and the cylinder wall. The primary aim of this coating is to improve the thermal and mechanical properties of the piston. Ceramic materials can withstand high temperatures and exhibit excellent corrosion resistance. Thus, applying a ceramic coating enhances the overall performance and longevity of the piston.
These coatings help in reducing friction, improving thermal efficiency, and increasing resistance to wear. This makes ceramic coated pistons particularly beneficial in high-performance engines where conventional pistons may fail to perform satisfactorily under extreme conditions.
Historical Development
The use of ceramic materials in engineering has been explored for many decades. Initially, ceramic coatings were implemented in aerospace and industrial applications. Their attributes, such as high-temperature stability and resistance to corrosion, made them suitable for environments that demand exceptional performance.
In the automotive sector, the application broadened in the late 20th century. The push for higher performance and greater fuel efficiency led manufacturers to consider ceramic coatings on pistons. As technology advanced, methods for applying ceramic coatings became more refined, making them more accessible for various automotive applications.
Many automotive brands quickly recognized the potential benefits and slowly integrated ceramic coated pistons into their designs. This has paved the way for further innovations and has become a staple for motorsport applications, enhancing both the competitive edge and reliability of performance vehicles.
Such developments signify an important step forward in engine technology, illustrating how the marriage of material science and engineering can yield significant advancements in automotive efficiency.
Understanding the Composition of Ceramic Coatings
The composition of ceramic coatings is pivotal in determining their effectiveness and performance in various applications. Ceramic coatings provide significant enhancements in durability, heat resistance, and overall engine efficiency. By understanding these materials, one can appreciate why ceramic coated pistons are becoming increasingly popular in the automotive industry. This section breaks down the types of ceramic materials used and the essential properties they possess.
Types of Ceramic Materials
Ceramic coatings are often made from several types of materials that offer unique benefits. Common materials include zirconium oxide, aluminum oxide, and silicon nitride. Each of these plays a distinct role in performance:
- Zirconium Oxide: Known for excellent thermal shock resistance and durability, zirconium oxide helps maintain the integrity of pistons under high-temperature conditions.
- Aluminum Oxide: This material is favored for its hardness which contributes to the overall wear resistance of the coated pistons.
- Silicon Nitride: Valued for its mechanical properties, silicon nitride is excellent at high temperatures and provides additional strength and stability in demanding environments.
Choosing the correct ceramic material for piston coatings can greatly influence performance and longevity.
Properties of Ceramic Coatings
Understanding the properties that ceramic coatings bring to pistons is essential. Key characteristics include:
Thermal Resistance
Thermal resistance is critical in applications exposed to significant heat. This property allows ceramic coatings to withstand high temperatures without degrading. The key characteristic here is the ability of ceramics to maintain their structure while reducing heat transfer to the underlying material. This is a crucial benefit in engines where excessive heat can lead to failure. The unique feature of thermal resistance in ceramics is that they can efficiently dissipate heat while protecting the substrate. This helps in maintaining optimal operating conditions, which is essential for engine longevity and performance.
Corrosion Resistance
Corrosion resistance is another vital property of ceramic coatings. It helps protect pistons from various corrosive agents, including moisture, fuel, and other chemicals. The key characteristic of corrosion resistance in ceramic materials is their ability to form a protective barrier over metal surfaces. This is beneficial because it reduces the rate of wear, ensuring a longer lifespan for the components. The unique feature of ceramic coatings in this regard is that they can significantly minimize maintenance needs and costly repairs in the long run.
Mechanical Strength
Mechanical strength indicates how well the ceramic coatings can resist deformation under stress. This property is essential since pistons undergo massive forces during operation. The key characteristic of mechanical strength in ceramics is their capacity to withstand repeated impact and stress without cracking or failing. This makes ceramic coated pistons reliable in high-performance scenarios. The unique feature of mechanical strength is its contribution to structural integrity, which enhances performance and reduces the likelihood of mechanical failure.
"In summary, understanding ceramic materialsโ types and their properties is essential for realizing the benefits of ceramic coatings in automotive applications."
Advantages of Ceramic Coated Pistons
The advantages of ceramic coated pistons extend beyond simple enhancements to performance; they mark a significant evolution in automotive technology. Understanding these benefits provides insights into why ceramic coatings are increasingly adopted in various applications. Each aspect contributes to the overall improvement of engine functionality and longevity, making the investment in such technology valuable for many vehicle owners.
Enhanced Durability
Ceramic coated pistons exhibit remarkable durability compared to traditional piston designs. This durability arises from the unique properties of ceramic materials which resist wear and fatigue under challenging operating conditions. For instance, ceramic coatings can withstand high pressures and temperatures, leading to a longer lifespan of engine components.
Additionally, the ruggedness of ceramic coatings means fewer replacements and repairs are needed. This translates into lower maintenance costs over the vehicle's life cycle. Users can expect significant reduction in wear rates, particularly in high-performance applications where piston failure is a critical concern.
Reduced Friction
Another crucial advantage of ceramic coated pistons is their ability to significantly reduce friction during engine operation. The smooth surface properties of ceramic materials help in decreasing surface contact areas and consequentially, friction losses. Less friction leads to improved efficiency and allows the engine to run smoother with less energy wasted on heat generation.
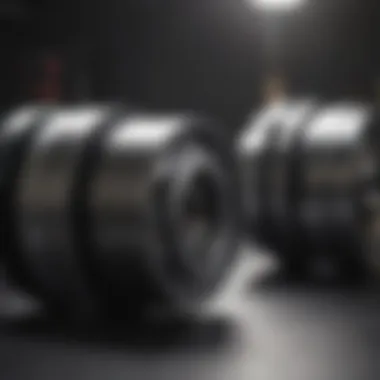
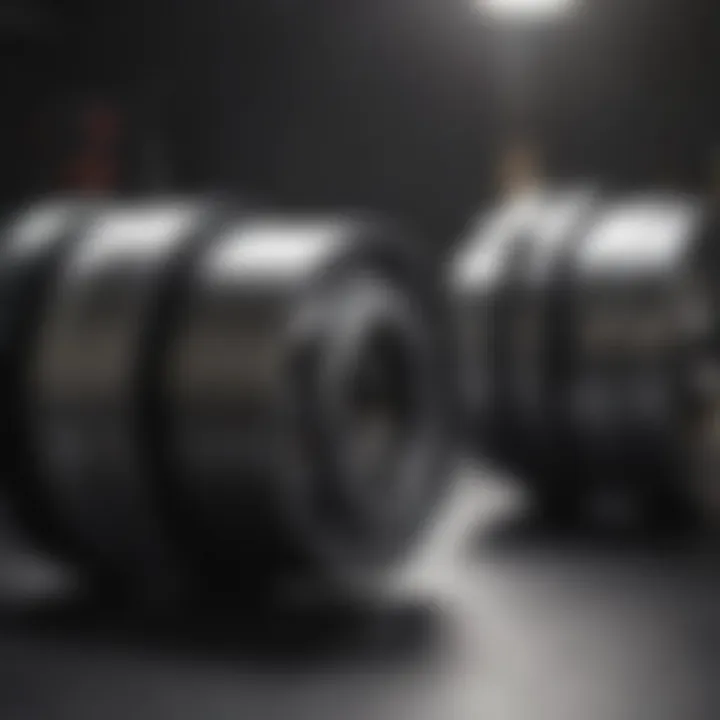
This reduction in friction not only enhances engine performance but also alleviates stress on moving parts. As a result, components such as connecting rods and crankshafts experience less wear, potentially extending their operational lifespan. Some studies suggest that friction reduction can lead to fuel savings of several percent, adding to the economic benefits of investing in ceramic coated pistons.
Improved Thermal Management
Ceramic coatings offer superior thermal management capabilities compared to traditional piston designs. They help to control heat transfer within the engine, ensuring that pistons maintain optimal operating temperatures. By reflecting heat away from critical areas, these coatings can minimize the risks of heat-induced damage, such as warping or cracking.
Furthermore, effective thermal management means that the engine operates within designated temperature ranges more consistently, enhancing overall efficiency. This consistent temperature control can also improve combustion efficiency and lower emissions, aligning with modern regulatory standards. As vehicles continue to evolve with more stringent emissions guidelines, such advancements in thermal management will be increasingly relevant.
"Investing in ceramic coated pistons can increase performance while significantly reducing the risk of engine failures due to thermal and mechanical stresses."
In summary, the advantages of ceramic coated pistons are considerable. They present an opportunity not only for performance enhancement but also for better efficiency, durability, and operational economy in various vehicular applications. As automotive technology advances, the benefits associated with these specialized coatings will likely play a pivotal role in reshaping engine designs.
Comparative Analysis with Traditional Pistons
The comparative analysis of ceramic coated pistons versus traditional pistons is crucial for understanding the advancements in engine technology. By examining the differences in materials and performance metrics, readers gain insight into why many automotive manufacturers opt for ceramic coatings. This analysis highlights the unique benefits offered by ceramic coatings that can significantly enhance engine performance and durability, as well as the considerations that come with adopting this technology.
Material Differences
Material composition is a defining factor in the performance of pistons. Traditional pistons typically use alloys like aluminum or cast iron, known for their good mechanical properties but limited thermal management capabilities. These materials can sometimes warp under extreme temperatures and stress conditions.
In contrast, ceramic coated pistons are constructed with a core material that can withstand higher temperatures and pressures and are further enhanced with a ceramic layer. This ceramic layer provides added protection against thermal fluctuation and corrosion, making them more resilient in demanding environments. The primary materials for ceramic coatings include zirconia and alumina, which offer superior thermal insulation and hardness compared to traditional alloys. This enables ceramic coated pistons to operate at higher levels of efficiency, especially in performance-driven applications.
Performance Metrics
When evaluating performance metrics, a few key factors stand out in the comparison between ceramic coated and traditional pistons. These include:
- Thermal Efficiency: Ceramic coatings enable better heat dissipation, leading to improved thermal efficiency. Traditional pistons may suffer heat buildup, which can affect engine performance.
- Friction Reduction: The smooth surface of ceramic coatings results in lower friction against cylinder walls. This reduction in friction not only enhances fuel efficiency but also prolongs engine life.
- Wear Resistance: Ceramic coated pistons demonstrate lower wear rates than their traditional counterparts, which can extend service intervals and reduce maintenance costs over time.
In summary, the comparative analysis reveals that while traditional pistons have served their purpose, ceramic coated pistons present significant advancements in material science, supporting higher performance and longevity. In an industry focused on efficiency and durability, understanding these differences is essential for anyone interested in automotive technology.
Applications of Ceramic Coated Pistons
The application of ceramic coated pistons plays a crucial role in various sectors of the automotive industry. It is essential to explore how these coatings elevate performance and longevity, offering significant advantages over traditional materials. The benefits encompass enhanced durability, improved thermal efficiency, and reduced friction. These characteristics are particularly critical in high-performance environments such as motorsport as well as regular consumer automotive use.
Motorsport Use
In the realm of motorsport, ceramic coated pistons are not just a luxury; they are a necessity. High-performance engines undergo extreme stresses where heat generation is substantial. The ceramic coatings effectively mitigate thermal expansion, which is a common issue in competitive racing. By maintaining stability at higher temperatures, these pistons help prevent mechanical failure. Additionally, the reduced friction leads to better energy efficiency, allowing racers to push their vehicles to limits without compromising reliability.
Applying ceramic coatings in motorsport engines often results in lower overall weight and enhanced responsiveness. These factors can provide a competitive edge, contributing significantly to a team's success on the track.
Consumer Automotive Applications
For everyday drivers, the integration of ceramic coated pistons represents a leap forward in engine technology. Many modern vehicles aim to balance performance and fuel efficiency, and ceramic coatings play a pivotal role. The smooth surface of the coated pistons minimizes friction during operation, promoting better fuel utilization. This efficiency is advantageous for consumers looking to save on fuel costs while maintaining satisfactory performance levels.
Moreover, the added corrosion resistance from ceramic coatings extends the lifespan of pistons, which is particularly valuable in regions where environmental conditions can be harsh. The enhanced durability means fewer replacements and reduced maintenance costs, making it an appealing feature for potential car buyers.
Industrial Machinery
Ceramic coated pistons are not limited to automotive applications; they also find a place in industrial machinery. High-stress environments in various industries require components that can withstand wear and heat without failure. Ceramic coatings contribute to improved mechanical strength in pistons used in industrial engines. This application ensures operational efficiency, particularly in sectors like construction and manufacturing where machinery run for extended periods and under high loads.
The application of such coatings in industrial settings also demonstrates adaptability and versatility. As industries advance, the need for durable and efficient components continues to rise. Therefore, ceramic coated pistons are increasingly relevant, leveraging their properties to meet the demands of modern engineering challenges.
"The use of ceramic coated pistons signifies a transformation in material science, enhancing performance across various fields."
In summary, the applications of ceramic coated pistons extend far beyond traditional expectations. Be it in motorsport, consumer vehicles, or industrial machinery, these innovations are reshaping how we envision engine performance and efficiency.
Technology Behind Ceramic Coating Applications
The application of ceramic coatings to pistons involves precise and advanced technology that enhances the performance of these engine components. This section delves into the methods of coating application, focusing on the benefits and considerations associated with these technologies. Understanding these processes is essential for automotive enthusiasts and professionals alike, as they directly impact the effectiveness of ceramic coatings on piston durability and efficiency.
Spray Coating Techniques
Spray coating is one of the most prevalent methods used to apply ceramic coatings to pistons. This technique involves the use of a spray gun that atomizes ceramic material into fine particles before they are deposited onto the surface of the piston.
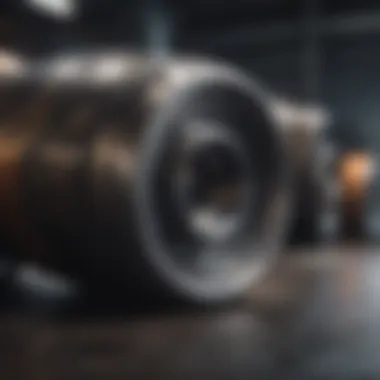
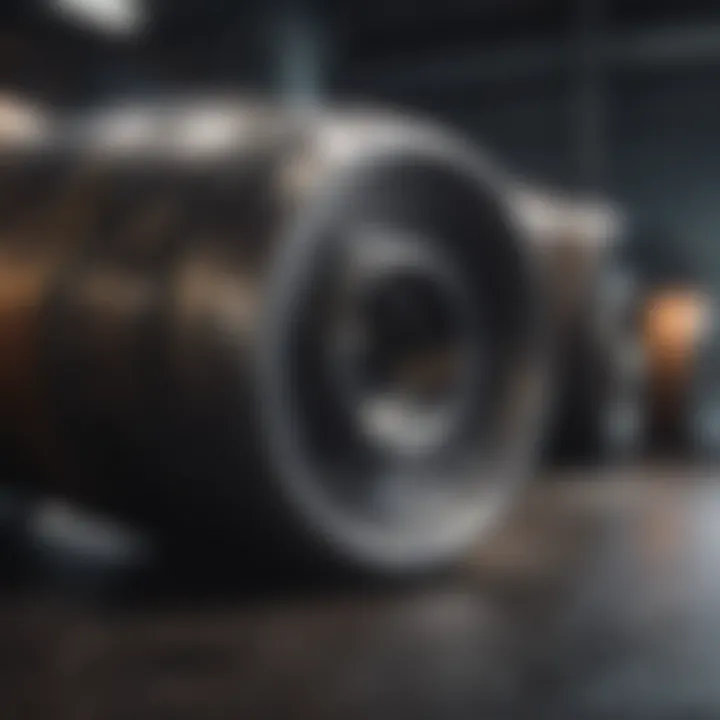
The importance of spray coating lies in its ability to provide an even and controlled application of the coating material. This ensures a uniform thickness, which is critical for optimizing the thermal and mechanical properties of the piston. Furthermore, spray coating can effectively cover complex geometries without compromising the integrity of the base material. The process can also be tailored for various ceramic compositions, allowing for the selection of specific coatings suited for different operational conditions.
Some common methods within spray coating include the Plasma Spray, HVOF (High Velocity Oxygen Fuel) spray, and APS (Atmospheric Plasma Spray). Each of these methods presents its own set of advantages, with variations in temperature control, bond strength, and surface finish.
"The selection of spray method greatly impacts the final performance of ceramic coatings on pistons."
Electrostatic Coating Methods
Electrostatic coating serves as another sophisticated method to apply ceramic coatings to pistons. This technique uses electricity to charge the ceramic particles, which are then attracted to the negatively or positively charged surface of the piston. This method greatly increases the efficiency of coating application and enhances adhesion, resulting in a smoother finish.
A significant benefit of electrostatic coating is its ability to minimize material waste. The charged particles adhere only to the targeted areas, which is not only cost-effective but also environmentally friendly. This method works well for creating a uniform coating layer, accommodating various ceramic materials like zirconia or alumina.
In industries where precision is paramount, the controlled application provided by electrostatic methods ensures high-quality coatings that can withstand extreme temperatures and pressures. Understanding how this technology works is essential for those interested in improving engine performance through advanced coating applications.
Challenges and Limitations
The integration of ceramic coatings in piston technology offers numerous potential benefits; however, it is crucial to address the challenges and limitations in this field. Understanding these aspects is essential for automotive enthusiasts, engineers, and manufacturers looking to optimize engine performance through advanced materials. Different factors play a role in the deployment and acceptance of ceramic coated pistons.
Cost Implications
Ceramic coated pistons are often associated with higher initial costs compared to traditional piston designs. The materials used in ceramic coatings, such as zirconium oxide or titanium dioxide, are more expensive. The production and application methods, including spray techniques and high-precision machinery, further contribute to the overall costs. This can lead to a significant budget consideration for manufacturers and consumers alike.
Moreover, the cost of replacing traditional pistons with ceramic coated alternatives can also act as a barrier to entry. Many car owners may weigh the performance benefits against the upfront investment. While ceramic coatings can extend the life of a piston and improve thermal efficiency, the initial expense is an important factor in the decision-making process.
Application Process Challenges
The application of ceramic coatings involves specific technical challenges that must be navigated carefully. Achieving a consistent coating thickness is vital for ensuring that performance enhancements are realized effectively. Inconsistent thickness can lead to uneven heat distribution or premature wear, negating the advantages of using ceramic coatings.
Additionally, the bonding between the ceramic layer and the underlying piston material can be problematic. If not applied correctly, the coating may delaminate, resulting in reduced performance or even engine failure. Quality control during the manufacturing process is paramount to ensuring the reliability of ceramic coated pistons.
Proper surface preparation and optimal application parameters are critical to ensure effective adhesion of ceramic coatings.
In summary, while ceramic coated pistons present exciting advancements in engine technology, challenges such as cost implications and application process hurdles remain significant considerations. To effectively harness the benefits of these innovative materials, stakeholders in the automotive sector must address these limitations strategically.
Future Trends in Ceramic Coatings
The field of ceramic coatings is experiencing significant advancements, making it a pivotal aspect of engine technology. Understanding future trends is crucial for automotive enthusiasts and professionals as these innovations can directly impact engine performance and sustainability. With the increasing focus on reducing emissions and enhancing fuel efficiency, the role of ceramic coated pistons cannot be overstated.
Innovations in Material Science
Recent innovations in material science are transforming how ceramic coatings are designed and applied. New formulations are being developed to enhance the mechanical properties of ceramic materials. For example, researchers are now exploring hybrid coatings that combine ceramics with polymers. This approach aims to achieve superior toughness and flexibility while maintaining the hardness inherent in traditional ceramic materials.
Additionally, researchers are investigating nanostructured coatings that provide better performance and reduced weight. Such materials may lead to substantial improvements in heat resistance and durability. The implementation of advanced techniques like additive manufacturing can also facilitate the creation of tailored coatings for specific applications, ensuring that each coating meets the unique demands of different engines.
These innovations promise to extend the lifespan of components, reduce the frequency of maintenance, and improve overall engine efficiency. The investment in R&D within this area is significant, indicating a strong market for ceramic coatings in future vehicle designs.
Automation in Application Techniques
Automation in the application of ceramic coatings is becoming more prevalent, driven by the need for precision and consistency. Advanced robotic systems are increasingly employed to apply coatings uniformly across surfaces. This not only enhances the quality of the application but also reduces human error, leading to better product reliability.
Automation can also speed up the production process. Faster application techniques enabled by robotics mean that manufacturers can meet growing demand for ceramic-coated pistons more efficiently. This is especially relevant in the automotive sector, where speed to market can influence competitive advantage. Moreover, automated systems can better manage the often complex layering processes required for effective coating applications.
New technologies like 3D printing are also being integrated into the application process. This allows for more intricate designs that can maximize coating performance while minimizing weight. As automation technology continues to evolve, it is expected that more sophisticated methods will emerge, making ceramic coatings even more effective and accessible to a wider range of automotive applications.
"The convergence of material science and automation marks a new era in the production and application of ceramic coatings, promising higher efficiency and better performance."
Finale
In the realm of automotive engineering, the inclusion of ceramic coated pistons represents a pivotal evolution. This technology not only promotes enhanced performance but also contributes significantly to the durability and longevity of engines. The insights gathered throughout this article underline the myriad advantages of employing ceramic coatings in piston manufacturing. As the automotive sector continues to advance, the elements discussed are essential for understanding how they influence future developments.
Summary of Key Points
- Durability and Strength: Ceramic coatings provide heightened durability, enabling pistons to withstand extreme temperatures and pressures better than traditional materials.
- Friction Reduction: The smooth surface finish associated with ceramic coatings means reduced friction between piston surfaces and cylinder walls, thus improving engine efficiency.
- Thermal Management: Ceramic coatings offer superior thermal resistance, allowing for more effective temperature control in high-performance engines.
- Cost and Application Challenges: While the benefits are substantial, cost implications and challenges in the application process have been identified, indicating the need for ongoing innovation in coating techniques.
- Future Trends: Innovations in material science and automated application techniques suggest a promising future for ceramic coatings in various automotive applications.
The Future of Engine Technologies
The future of engine technologies appears bright, especially with the implementation of ceramic coatings. As fuel efficiency and environmental sustainability take precedence in the automotive industry, ceramic coated pistons will likely play a crucial role in meeting these demands. The development of new materials that are lighter and stronger could further enhance performance metrics.
Moreover, the advancement of automated application methods for ceramic coatings promises to reduce production costs and improve coating uniformity. This will encourage more manufacturers to adopt this technology.
"The integration of advanced coatings is not just about enhancing performanceโit's about redefining what is possible in engine design and manufacturing for the next generations."