Understanding Compound Turbo Systems in Cummins Engines
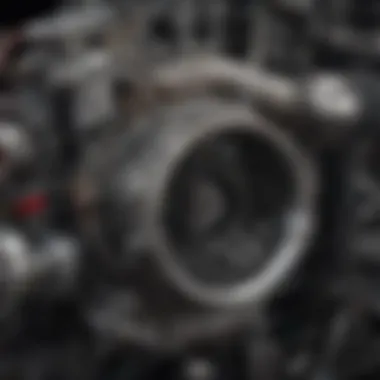
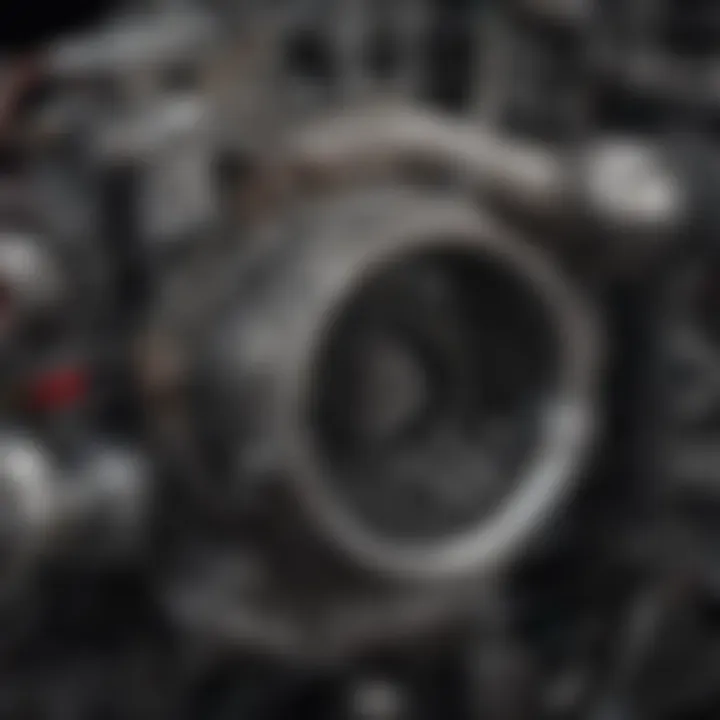
Intro
Compound turbo systems have gained traction in the automotive world as a method for enhancing engine performance, especially for 24 valve Cummins engines. This setup allows for increased airflow, reducing turbo lag while improving power delivery and fuel efficiency. This article intends to delve into the details of compound turbocharging, the operational principles related to Cummins engines, as well as practical aspects involving installation and tuning.
Compound turbo systems utilize a two-stage approach where one turbocharger spools up quickly at lower RPMs, providing immediate boost and torque, while a larger turbo kicks in at higher ranges to supply power. Understanding this mechanism can greatly help enthusiasts and professionals alike to maximize performance.
Throughout the article, crucial components, installation challenges, and maintenance practices will be explored, along with possible pitfalls to avoid. Keeping your Cummins engine in peak performance remains a central focus of this discussion.
Automotive Features and Innovations
In the landscape of automotive advancements, the focus primarily lies on efficiency and performance. The 24 valve Cummins engines have seen impressive innovations, particularly in turbocharging technology.
Overview of Latest Technologies
Recent developments in turbo systems have markedly improved engine efficiency. The advent of variable geometry turbochargers enables dynamic adjustment of turbine geometry, optimizing performance at different speeds. This is especially beneficial for compound turbo setups. Modified compressors and advanced material technology aid in decreasing weight and enhancing durability too.
Evaluation of AI in Automotive Solutions
Automakers are incorporating artificial intelligence into various facets of engine management. AI algorithms can optimize a vehicleโs performance characteristics more precisely. By analyzing real-time data, AI solutions can enhance tuning strategies for compound turbo systems, allowing for a more tailored performance profile based on user driving habits.
With the combination of modern technology and classic engine designs, Cummins users can achieve unprecedented levels of performance and reliability.
Maintenance Tips and Best Practices
To ensure longevity and reliability in compound turbo systems, proper maintenance is key. Keeping a close eye on the engine's health can prevent costly repairs and prolonged downtime.
Regular Maintenance Schedules
- Oil Change: Maintaining regular oil changes is critical. High-performance oils are advisable for optimal running.
- Air Filter Checks: Clean air filters avoid restriction and ensure turbochargers breathe efficiently.
- Boost Pressure Maintenance: The boost pressure should be monitored periodically. Devi dations may indicate a problem.
Addressing Common Issues and Solutions
Common problems in compound turbo systems can range widelyโfrom fitting and installation issues to boost leaks. Here are few solutions:
- Use Quality Gaskets: Quality gaskets minimize leaks where different components meet.
- Regular Inspections: Conduct regular inspections of component seals to check for integrity.
The End
The utilization of compound turbo systems in 24 valve Cummins engines presents a vast array of performance benefits alongside some challenges. Installation, tuning, and maintenance require thoughtful planning and execution. By understanding the principles of these systems and their interaction with the engine, users can significantly enhance the driving experience and power outputs.
This overview serves not only as an informative resource but also aims to inspire enthusiasts and professionals to create high-performing setups. Utilizing advanced turbocharging technologies reflects a true advancement in automotive engineering.
Foreword to Compound Turbo Systems
The integration of compound turbo systems in automotive engineering plays a significant role in enhancing performance, particularly in heavy-duty engines like the 24 valve Cummins. Understanding these systems involves more than just knowing their function; it is essential to grasp their design philosophy, which markedly differs from standard single turbo configurations. By diving into compound turbocharging, we can uncover the nuances that make this technology compelling, not only for racing enthusiasts but also for those seeking dependable power for daily tasks.
Definition of Compound Turbocharging
Compound turbocharging refers to the use of two or more turbochargers in a sequential manner to increase an engineโs intake airflow and boost pressure. This system is engineered to overcome limitations found in traditional single turbo setups. In essence, one turbo charger (the primary) tends to handle low RPMs, while the additional unit (the secondary) specializes in managing the higher RPM bands. This dual-stage method enhances power delivery across the spectrum and optimizes overall engine efficiency. The beneficial outcomes include more power at lower RPMs and sustained power during high-performance operations.
Historical Context of Turbocharging
Turbocharging itself has a rich history that goes back many decades. Originally developed in the early 1900s, the intention was to improve performance in aviation engines. The inception of this technology found a fertile ground during World War II, paving the way for faster and more capable military aircraft. As the need for increased engine efficiency and performance trickled into automotive applications, diesel engines began to capitalize on turbocharging technologies in the 1980s.
The evolution of turbocharging technologies means the transition from simple, single-unit systems to complex configurations like the compound turbo setup seen in the contemporary 24 valve Cummins engines. These developments highlight advancements achieved in engineering know-how, materials capable of withstanding higher temperatures and overall performance enhancements contributing directly to both efficiency and reliability in a myriad of driving conditions.
โUnderstanding compound turbo systems is crucial for enthusiasts who seek to maximize their engineโs potential without sacrificing durability.โ
Technical Overview of the Valve Cummins Engine
The Technical Overview of the 24 Valve Cummins Engine offers a pivotal understanding of how its unique architecture and features influence overall engine performance. A thorough examination of this system provides insight into why integrating a compound turbocharger configuration is particularly beneficial. Itโs important to note that the Cummins 24 valve engine is renowned for its robustness and efficiency, factors that lay the groundwork for advanced modifications like compound turbocharging.
Engine Specifications
When discussing the engine specifications of the 24 valve Cummins, we must consider elements such as displacement, horsepower, torque ratings, and procedural expectations from the turbo systems attached. Commonly, the engine is offered in a 5.9-liter displacement, and some models extend up to 6.7 liters. Horsepower often varies, ranging from 200 to 350 depending on specific iterations. Torque, critical for towing and performance in truck applications, can reach 800 lb-ft or more.
Moreover, here are some specifics relevant to the engine:
- Common Rail Fuel System: Allows for precise fuel delivery.
- B95 High-Pressure Injectors: Designed for enhanced meal flow and combustion.
- Heavy-Duty Construction: Blocks made of iron that can withstand higher temperatures and pressures.
These specifications illustrate that the 24 valve Cummins engine is engineered to perform under heavy loads, which is particularly fitting for turbocharging enhancements. Instantly noticeable is the remarkable power-to-weight ratio and efficiency figures that are appealing for performance enthusiasts.
Design Features of Valve Systems
The design attributes of the 24 valve configuration distinctly influence combustion characteristics and airflow. Unlike traditional configurations, it utilizes a single camshaft that actuates both intake and exhaust valves. This design results in a compact head layout that significantly supports high-speed operation and efficient airflow pathways.
Several features stand out:
- Four-Valve Layout: Increases the area for intake and exhaust operations, consequently boosting airflow.
- Intercooler Compatibility: Often designed to work alongside intercoolers which reduces air temperature and increases density, vital elements for turbocharged setups.
- Enhanced Cooling: Block and head designs with better heat dissipation capabilities.
In summary, the design ensures optimal airflow dynamics control during various engine loads. Any compound turbo installation requires acknowledging these systematic features to enhance engine performance through more sophisticated turbocharging schemes.
Utilizing the 24 valve Cummins engine opens a pathway for increasing horsepower through enhanced design features and superior cooling.
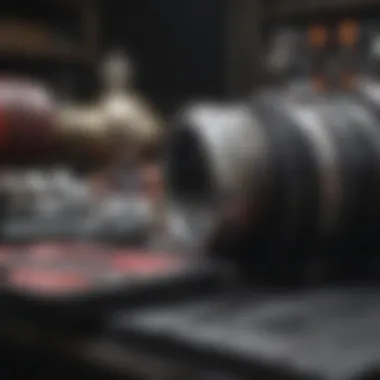
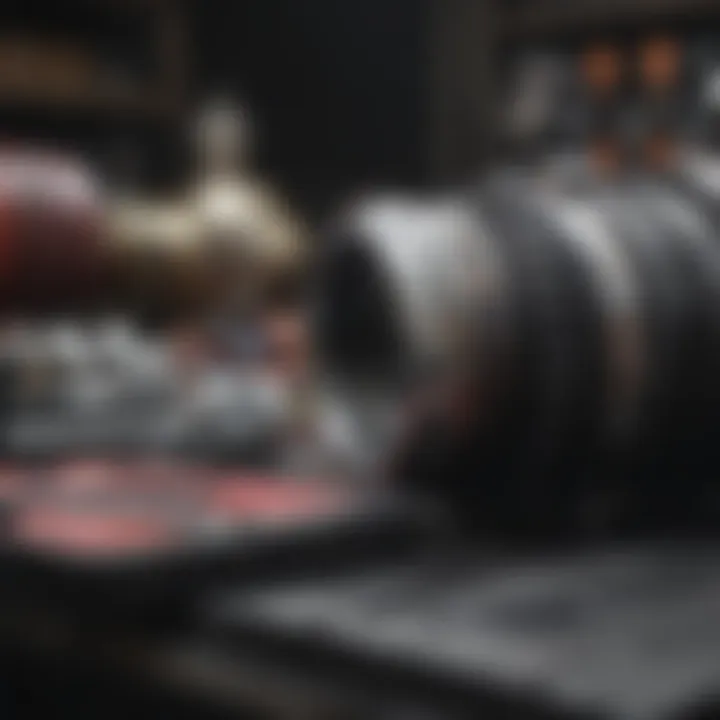
These specifications and robust designs form a framework for further modifications. Understanding them lays a solid base for comprehending how turbo systems can optimize performance for Cummins engines, especially in compound configurations.
Benefits of Compound Turbocharging for Cummins Engines
Compound turbocharging offers a myriad of advantages, tailored specifically for 24 valve Cummins engines. These benefits contribute to enhanced performance, efficiency, and drivability. Understanding these elements is essential for automotive enthusiasts, technicians, and students alike. By elaborating on aspects such as increased power output, improved efficiency, and reduced turbo lag, we can appreciate the significant role compound turbocharging plays in modern engine designs.
Increased Power Output
The most notable benefit of compound turbocharging is the dramatic increase in power output. With a dual-turbo configuration, power availability increases, especially at higher RPMs. The smaller turbo operates efficiently at lower RPM, attaching to the larger one for enhanced pressure in the higher range.
This power gain primarily arises due to several factors:
- Increased air density leads to more oxygen for combustion, enhancing power.
- Better thermal management results from staging, maintaining stable temperatures and avoiding overheated components.
- Community forums on platforms like Reddit and Facebook highlight experiences of users showcasing significant power gains.
Top-tier setups can push a 24v Cummins to output levels that might be difficult with a traditional setup. Thus, enthusiasts can reliably depend on their vehicles for demanding tasks, such as towing or racing.
Improved Efficiency
Another pragmatic benefit of compound turbocharging centers around efficiency. Efficiency includes both fuel usage and thermal processes. The dual configuration allows the Cummins engine to extract more energy from the same fuel volume, effectively improving miles per gallon (mpg).
Key points reflecting this improvement are:
- Enhanced air-fuel mixture improves fuel combustion ratios.
- Reduced engine load leads to optimised fuel expenditure at various driving conditions.
- Many users have argued about their experiences achieved through increased fuel efficiency shared on groups and forums.
By improving the air intake and supply dynamics, itโs clearer how compound systems refine overall functionality in 24 valve Cummins engines, appealing specifically to those valuing cost-saving operational aspects.
Reduced Turbo Lag
Turbo lag can be a frustrating aspect of traditional single-turbo systems. Compound turbocharging effectively reduces it. In standard turbo systems, noticeable delays occur before power delivery. With compound systems, the smaller turbo comprises the duty cycle at low RPM, allowing for quick and responsive acceleration.
Reasons contributing to reduced lag include:
- Fast spool-up due to reduced inertia of the smaller turbine.
- Consistent boost pressure maintained across a larger RPM range, avoiding dips in power performance.
- User reviews consistently highlight responsiveness improvements gained post-installation through brake checks and device alignments.
Engines equipped with compound turbocharging systems mean a more pleasurable driving experience devoid of latency, marking the transition of the vehicle as swift and responsive at various speeds.
In summarization, compound turbocharging brings notable improvements in performance metrics surrounding 24 valve Cummins engines including power production increases, enhancing efficiency while tackling turbo lag challenges. These combined features offer solid reasons for any enthusiast to consider this sophisticated technology in their performance endeavors.
Operational Principles of Compound Turbo Systems
Understanding the operational principles of compound turbo systems is crucial for anyone looking to enhance the performance of a 24 valve Cummins engine. This section delves into how compound turbochargers function and the significant benefits they provide.
How Compound Turbochargers Work
A compound turbocharger system typically consists of two or more turbochargers utilized in sequence to maximize air intake and boost pressure. The process begins with the low-pressure turbo, which is responsible for compressing the air before it reaches the high-pressure turbo. This design allows for more efficient airflow and better management of combustion.
Key Elements of Operation:
- Air Compression: As air enters the first turbo, it is compressed and heated. This compressed air is then directed to the second turbo, where further compression occurs.
- Boost Pressure Elevation: The sequential nature of these turbos significantly elevates boost pressure, driving more air into the engine. The added air allows for improved fuel combustion, leading to greater power output.
- Power Efficiency: By optimizing airflow, compound turbo systems enhance the overall efficiency of the engine, reducing wasted energy and lost horsepower.
This dual-turbo arrangement not only improves performance but also effectively minimizes turbo lag, a common issue found in single turbo systems. By delivering quicker response times and increased overarching boost, compound systems become highly advantageous.
Stages of Turbocharging
Turbocharging involves distinct stages that contribute essential functions to the performance of a vehicle. Understanding these stages helps users recognize how to implement and adjust their turbo systems for optimal results.
Stages include:
- Low-Pressure Stage: Primarily serves to provide initial boost, operating at lower RPMs.
- High-Pressure Stage: Takes the airflow from the low-pressure turbo and applies significant additional pressure, driving it into the engine at higher RPMs.
- Wastegate Control: Acts as a regulating mechanism to prevent excessive overhaul conditions that could damage the system by diverting excess boost back to the intake.
- Fuel Air Management: Enhanced fuel injection strategies work in conjunction with variable boost levels to ensure comprehensive fuel mixing and effective ignition timing.
Combining these stages allows the engine to utilize boost more effectively, improving drivability and overall performance without compromising path mechanics.
Knowledge of the stages of turbocharging will empower enthusiasts to make informed choices about performance dynasty moving forward.
The operational principles behind compound turbo systems reveal a wealth of opportunities for users of 24 valve Cummins engines. Understanding the intricate workings and stages of turbocharging underscored in this section is essential for achieving the desired balance between power, efficiency, and reliability.
Installation Considerations
Whether upgrading or building a compound turbo system for 24 valve Cummins engines, focusing on installation considerations is critical. This phase impacts performance, reliability, and lifespan of the turbo system. Correctly preparing the engine bay, choosing suitable components, and establishing proper wiring and control systems cannot be overlooked. Each aspect plays a role in ensuring optimal functionality and safety of the overall setup.
Preparing the Engine Bay
An organized and clean engine bay is fundamental for any successful installation. Removing any obstacles and ensuring there is sufficient physical space for the turbo components can improve airflow and heat dissipation. Start by disconnecting the battery and clearing the space around the engine. Pay attention to any existing parts that may hinder access to the turbos.
Following this, inspect the engine bay for signs of wear. Look for outdated components, leaks, or connections that need attention. Ensuring the area is clean not only helps in physical access but also aids in preventing any contaminants from compromising the performance of your brand-new turbo setup.
Selecting Appropriate Components
Once the engine bay is ready, the next step is to select the right components for your compound turbo system. Compatibility of each part is crucial for achieving maximum efficiency. Key components include turbochargers, intercoolers, exhaust manifolds, and waste gates. One should carefully consider the specifications ููroperties of these components and how they work together.
When choosing turbochargers, it is essential to match them with your desired power output and performance goals. Some commonly recommended brands for Cummins upgrades include BorgWarner and Garrett, known for providing reliable turbo solutions. Properly sized parts cater to specific power demands and are vital to avoid bottlenecks in the system. Consult with professionals or communities focused on Cummins engines for recommendations.
Wiring and Control Systems
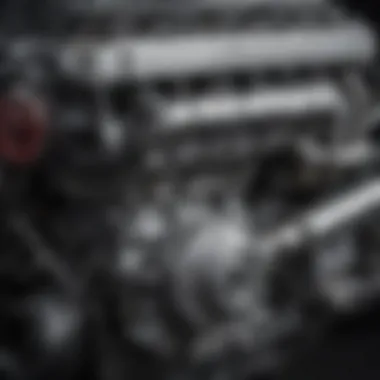
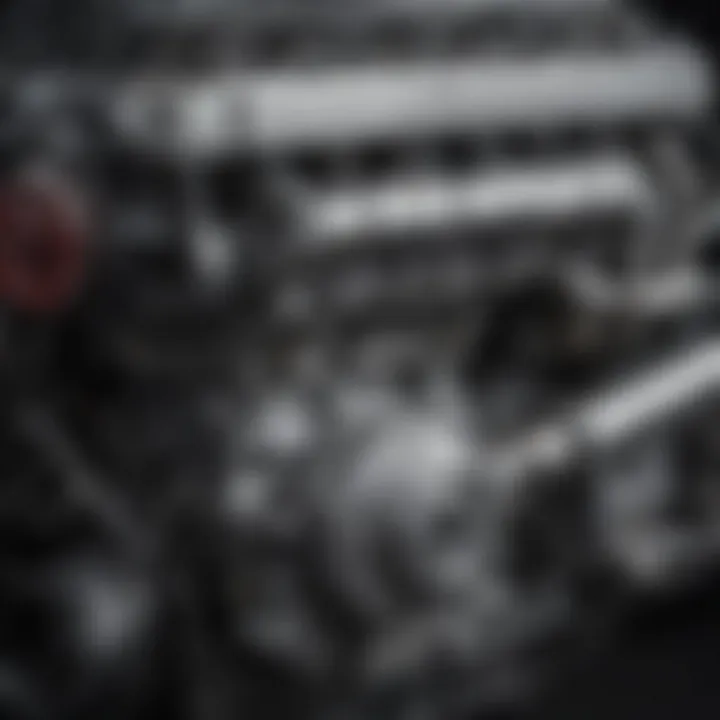
Lastly, the wiring and control systems require meticulous attention during this installation phase. Good control systems play a significant role in maximizing turbo performance while ensuring safety. Your ECU will need remapping to accommodate the changes resulting from the compound turbo setup. Todayโs systems can offer a range of tuning abilities that are critical for adjusting fuel delivery times and boost levels.
Make sure to secure all wiring in a way that avoids heat damage or mechanical failure over time. Status lights and gauges can also help you monitor the status of your turbo system in real-time. If additional wiring for sensors is needed, credit those feature for enabling future troubleshooting and performance evaluation.
Proper installation not only optimizes engine performance, it also upholds safety and reliability in your vehicle.
By taking these installation considerations into account, automotive enthusiasts can expect a smoother performance and truly enjoy the benefits that compound turbocharging offers for their 24 valve Cummins engines.
Performance Tuning for Compound Turbo Systems
Performance tuning is a critical aspect when working with compound turbo systems in 24 valve Cummins engines. These engines are designed for high efficiency and power output, and when pairing them with compound turbos, tuning can maximize their potential. Tuning etiquette makes sure that the engine functions optimally without causing damage. This section explores two main components: ECU remapping techniques and Boost management strategies.
ECU Remapping Techniques
ECU remapping is a fundamental step when tuning a Cummins engine with a compound turbo system. This process involves altering the factory settings of the engine's control unit to optimize performance according to the specific turbo configuration. Elegantly tuned ECU parameters can augment fuel delivery and timing, which directly affects power output. Here are some techniques to consider:
- Understanding Factory Limits: Familiarize yourself with the engine's stock parameters. Taking note of the maximum allowed fuel pressure and boost levels is crucial before modifications.
- Single vs. Dual Maps: Providing a choice between performance and fuel-efficiency tuned maps is valuable. Having dual setups allows flexibility depending on the needs.
- Iterative Testing: After new settings are applied, rigorous testing is required. It helps to ensure the changes deliver expecte performance without causing detrimental side-effects.
- Using Real-Time Data: Monitoring system performance gives insight. You can use tools to display engine parameters during operation to help fine-tune settings on-the-fly.
This method does not only achieve better performance metrics such as horsepower or torque but also accounts for drivability and fuel efficiency. Thus, ECU remapping increases power without compromising reliability.
Boost Management Strategies
Effective boost management is essential for maintaining performance integrity in compound turbo systems. The goal is to harness power while avoiding excessive strain on engine components. This part delves into important strategies for adept boost management:
- Controlled Boost Levels: Set limits on the maximum boost pressure to prevent compressor surge or engine knock. A gradual vs. sudden ramp-up can provide smoother throttle responsiveness.
- Wastegate Calibration: Calibrating wastegates fulfills the proper functions of redirecting exhaust flow. Ensuring it opens at the right boost levels contributes to overall engine efficiency.
- Boost Control Systems: Installing devices that can monitor and adjust boost quickly can help manage engine performance more dynamically. Systems like aftermarket electronic boost controllers offer more precision compared to stock components.
- Testing and Adjustment: The best results come from a continual cycle of testing and refinements. Changing an engine's operation control sometimes may be needed as conditions or builds evolve, requiring a revisit to boost parameters.
Proper performance tuning enhances engine reliability and maximizes the benefits of compound turbo charging systems, leading to boosted usability in different driving conditions.
When combined, effective ECU remapping techniques and rigorous boost management strategies create a potent synergy of enhanced engine performance and mechanical efficiency, allowing 24 valve Cummins engines equipped with compound turbos to truly shine.
Common Challenges and Solutions
Understanding common challenges in compound turbo systems specifically for 24 valve Cummins engines is crucial for optimizing overall performance. This section examines prevalent issues faced during implementation and operation alongside effective solutions to mitigate them. Such insights prove valuable not only for car owners but also for automotive enthusiasts and students who aim to understand or innovate turbocharging technologies.
Identifying Performance Bottlenecks
Performance bottlenecks can significantly hinder the efficiency of compound turbo systems. Identifying these obstructions is first step towards a effective resolution. Bottlenecks can emerge from various areas:
- Turbocharger sizing: If the primary turbo is too small, it cannot harness optimal airflow. Conversely, an excessively large turbo can lead to turbo lag, affecting throttle response and performance.
- Airflow restrictions: Air filters, intercoolers, and exhaust systems must allow unrestricted airflow. Blockages in these components impact performance.
- Fuel delivery: An inadequate fuel supply can lead to lean conditions where the engine does not receive enough fuel to match the air intake, risking damage.
Addressing Compatibility Issues
Compatibility between various components is vital when integrating a compound turbo system into a 24 valve Cummins engine. Ensuring seamless coordination can lead to a more reliable and efficient setup. Some key attributes to consider include:
- Aftermarket Parts Adaptation: Not all aftermarket components are designed to work with each other. Choosing the right injectors and exhaust systems tailored for a specific turbo configuration is imperative.
- Control Systems: The engine's control unit (ECU) must be capable of supporting both turbochargers. Mismatched systems can lead to performance losses. Tuning adjustments are often necessary to ensure that all components function harmoniously.
Aftermarket Components and Enhancements
In the realm of high-performance automotive engineering, aftermarket components play a significant role in enhancing the capabilities of 24 valve Cummins engines equipped with compound turbo systems. These enhancements can dramatically improve engine performance, fuel efficiency, and reliability. Aftermarket modifications allow enthusiasts and professionals alike to customize their vehicles according to specific needs. Additionally, understanding the synergy between these components can facilitate a more effective tuning process.
Key elements to consider include injectors and exhaust system modifications, both of which significantly affect overall performance.
"Aftermarket components can elevate your turbocharging setup by complementing the existing systems and improving efficiency."
Choosing the Right Injectors
Selecting the correct injectors is critical for achieving optimal fuel delivery in compound turbo applications. The performance of an engine is closely tied to the fuel-air ratio, which can vary greatly between stock and modified setups. In 24 valve Cummins engines, the injectors must match the power goals and flow requirements dictated by the chosen turbo configurations.
When evaluating injectors, factors such as
- Flow rate
- Spray pattern,
- Electrical resistance
can make considerable differences in engine performance. A higher flow rate can lead to greater power output, as the engine can consume additional fuel to match the generated air volume by the turbochargers. Properly matched injectors reduce misfires and enhance throttle response, promoting a smoother operation.
Investing in quality aftermarket injectors, specifically designed for compound setups, also mitigates potential wear and failure. It is essential to evaluate injectors from reputable manufacturers to ensure fidelity to performance specifications.
Exhaust System Upgrades
Upgrading the exhaust system is another vital component in optimizing compound turbo setups. A high-performance exhaust system can minimize backpressure, allowing turbochargers to spool more efficiently. This benefits the engineโs output, especially in high-efficiency or high-boost applications.
Key considerations for exhaust upgrades include:
- Materials: Stainless steel or similar materials resist corrosion and maintain strength at high temperatures.
- Design: Larger diameter pipes decrease restriction, optimizing gas flow.
- Muffler Choices: Performance mufflers can balance sound levels while protecting against excessive backpressure.
The right exhaust system is instrumental in promoting proper airflow, essential for supporting increased turbo pressure. By being strategic with aftermarket enhancements, one can unlock profound potential within the 24 valve Cummins engine, yielding particularly significant improvements in performance and efficiency ranges.
Maintenance Practices for Compound Turbo Systems
Maintaining a compound turbo system in a 24 valve Cummins engine is essential for ensuring optimal performance and longevity. Regular maintenance not only extends the life of turbochargers but also enhances overall engine efficiency. Neglecting maintenance can lead to several issues, reducing the efficacy of the turbo system. Key elements of maintenance practices include inspections, oil management, and performance checks.
Regular Inspection Routines
Inspections play a crucial role in preserving the health of compound turbo systems. A routine inspection helps identify potential problems before they escalate. This includes checking for wear and tear on various components.
Key Inspective Elements

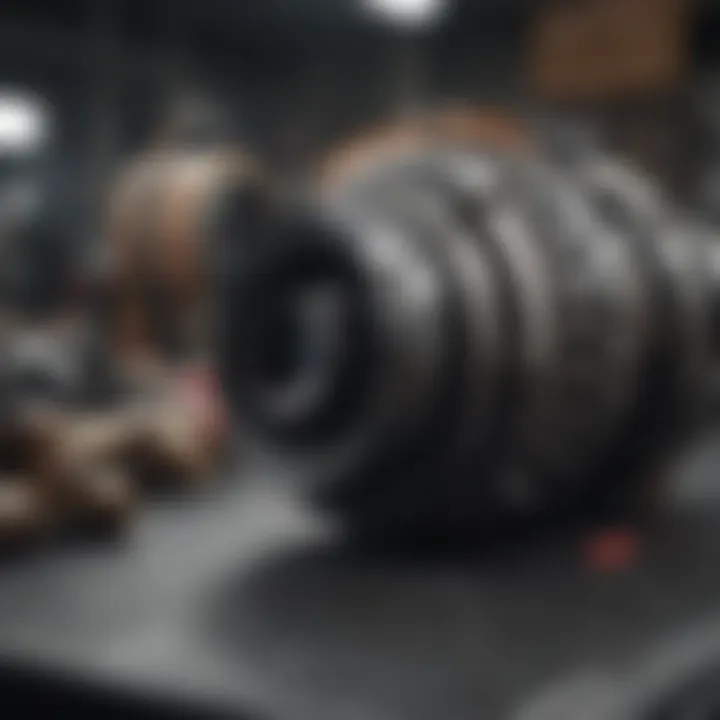
- Physical Damage: Look for cracks or dents on the turbocharger and associated castings.
- Leak Free Environment: Ensure piping and connections are tight, preventing boost leaks.
- Gaskets and Seals: Check for signs of wear. Leaky gaskets can jeopardize performance.
- Intake System: Inspect the intake manifold and pipes for debris and obstructions.
Take note that regular inspections should coincide with any oil changes and scheduled maintenance intervals to ensure comprehensive system care. Adjustments to inspection frequency may rely on performance demands and driving conditions, with frequent usage calling for more rigorous checks.
Good maintenence practices are always needed when working with complex systems to avoid damage down the line.
Oil Change and Management
Proper oil management is vital in any turbocharged application, particularly for a compound turbo system. The oil serves not just as a lubricant but also absorbs and dissipates heat generated during operation.
Steps for Effective Oil Management
- Choose the Right Oil: Using high-quality synthetic oils can enhance lubrication and increase overall system life.
- Regular Changes: Adhering to strict oil change intervals prevents sludge buildup. Most manufacturers recommend oil changes every 5,000 to 7,500 miles.
- Monitor Oil Temperature: Excessively high oil temperatures may indicate other mechanical failures.
Best Practices
- Inspect oil filters regularly and replace them during oil changes to maintain efficiency in oil flow.
- While checking oil levels, always top up with appropriate grades compatible with turbo systems that support optimal thermal handling adapters.
By systematically applying these maintenance practices, the reliability and performance of compound turbo systems can be maximized, thus serving car owners and automotive enthusiasts well in their mission to enhance Cummins engine capabilities.
Case Studies of Successful Implementations
Case studies are vital to understanding the effectiveness of compound turbo systems, especially in 24 valve Cummins engines. They provide real-world examples that emphasize specific advantages and options available to automotive enthusiasts. These implementations help illustrate how particular configurations perform under various conditions. By examining these cases, one can grasp the direct benefits including power enhancement, efficiency improvements, and practical scalability.
The actual equipment involved provides useful insight. Different applications may call for unique adjustments or setups. They reveal how collective experience leads to better technology, ultimately serving as a guide for new efforts and innovations.
High-Performance Applications
In many high-performance applications, using compound turbo systems has shifted the power curve significantly. Case studies show how trucks in truck pulls, competitive racing, and off-road performance have been advanced by these systems. Improved airflow leads to higher boost and an increase in overall horsepower, a diagrammatic view of this scenario reveals how quick spooling twin turbos work in coordination. Various setups can provide continuous power levels, even under extreme load conditions.
Some noted successes include vehicles modified specifically for racing. Many Cummins enthusiasts take pleasure in pushing these engines close to their limits. Taking lessons from track experience shows how intricate tuning led to favourable setups.
Benefits often include:
- Enhanced throttle response
- A drastic reduction in turbo lag
- Efficiency in maintaining stable operating temperatures
Real examples include individuals achieving 1,200 horsepower easily, achieving acceleration feats that once seemed unattainable for stock engines.
Daily Driver Conversions
Daily driver conversions present a more unique case of compound turbo systems usage. The primary objective here is balancing between performance and livability. Many users have adopted these complex systems in standard vehicles, able to achieve additional performance while responsibly managing the engineโs everyday functionality.
Key issues involve gains in torque and overall usability-solving the common problem of sluggish pickups in larger passenger vehicles. Average reports of improved fuel efficiency anchor the common claims circulating in the automotive community.
Aspects worth exploring in daily driver case studies include:
- Increased towing capacity
- Responses that offer excitement without sacrificing daily practicalities
- Well-balanced settings to avoid problematic turbo noise or heating issues
A noteworthy example would be augmenting a standard Dodge RAM delivering more than adequate results for city drives and occasional road trips. From average fuel efficiency marks rising to 22 mpg unexpectedly opens a revealing light on expected future growth of such systems.
With the steady advancements in technology and installation practices, these case studies underline achievable potential and practical applications of compound turbo systems, personifying the durability and suitability akin to 24 valve Cummins engines.
Future Trends in Turbocharging Technology
The automotive industry is undergoing significant changes, especially regarding engine performance technologies such as turbocharging. In the context of 24 Valve Cummins engines, future trends will define both efficiency and enhancement. Exploring innovation in turbocharging is crucial for enthusiasts, car owners, and professionals seeking to maximize the performance and reliability of their engines.
One area of interest is the promise of energy efficiency coupled with performance gains. Adapting new technologies is relevant, driven by regulations and consumer interest. Engineers and automotive developers are focusing on enhancing systems without sacrificing any core aspects like power delivery.
Electric Turbocharging Innovations
Electric turbocharging is one of the most talked-about innovations in turbo technology. It addresses turbo lag, a common failure point in traditional setups. By utilizing an electric motor to spool up the turbocharger as needed, performance can be optimized for different driving conditions. This way, peak power delivery is feasible with minimal lag.
When integrated with the respective engine management systems, these electric turbos can redefine the driving experience, offering higher reliability and responsiveness. Companies are investing in this technology for several reasons:
- Instantaneous Boost: Achieving boost pressure quickly ensures better performance right from the start.
- Engine Downsizing Compatibility: Supporting smaller engines, electric turbos enable characterizition power output despite their reduced size.
- System Control: Enhanced controls can regulate power output intricately, matching any conditions requiring adjustment.
There is ongoing research to further refine these electric systems, making them lighter and more effective over time.
"The transition to electric turbocharging technology may eliminate issues that hampered traditional systems, granting higher performance capabilities."
This sentiment outlines the confidence surrounding future developments. Hence, enthusiasts should keep an eye out for standard implementations in off-the-shelf performance upgrades in the near future.
Integration with Hybrid Systems
Integrating turbo systems with hybrid technology is another emerging trend. The hybridization of powertrains allows for dual sources of propulsion - meaning increased fuel efficiency. Turbocharged engines can significantly benefit from partnering with electric power concepts. Battery-assisted power can repeatedly meet varying demands without compromising performance. Benefits include:
- Enhanced Performance: Combining the energy boost from both setups can lead to significant power specifications beyond conventional limits.
- Improved Emissions Control: With hybrids, it is possible to intercross energy from electric and traditional engines, creating a harmonized structure focused on lesser emissions.
- Operational Flexibility: Vehicles can tap into power as necessary according to driving needs, offering versatility not commonly found in traditional systems.
Research must continue in creating seamless communication between electrical and turbocharged power systems. Developers are beginning to address the challenges including system weight, cost, and data management/training integration.
Overall, the future of turbocharging technology, especially for 24 Valve Cummins engines, points toward improvements that will enhance performance, maintain efficiency, and reduce environmental impact. Continuous advancements and a paradigm shift toward adopting better technologies will gradually reshape the way these systems are developed and perceived.
Epilogue
Several factors must be taken into account to optimize the potential of compound turbocharging. These include the proper choice of components, tuning strategies, and thoughtful maintenance practices. Not only do they prolong the life of the engine, but they also ensure its reliability when pushing performance limits.
"Proper tuning and maintenance are integral for sustaining enhancement gained from compound turbocharging in high-performance applications and daily drivers alike."
The exploration of case studies featuring successful implementations enriches the narrative. Learners, automotive enthusiasts, and professionals can draw valuable experiences from these examples, which highlight both the challenges faced and the solutions employed.