Understanding the Forged 383 Crankshaft: Benefits & Uses
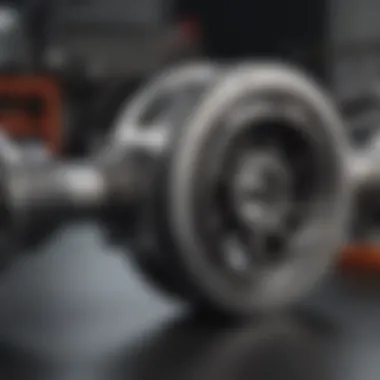
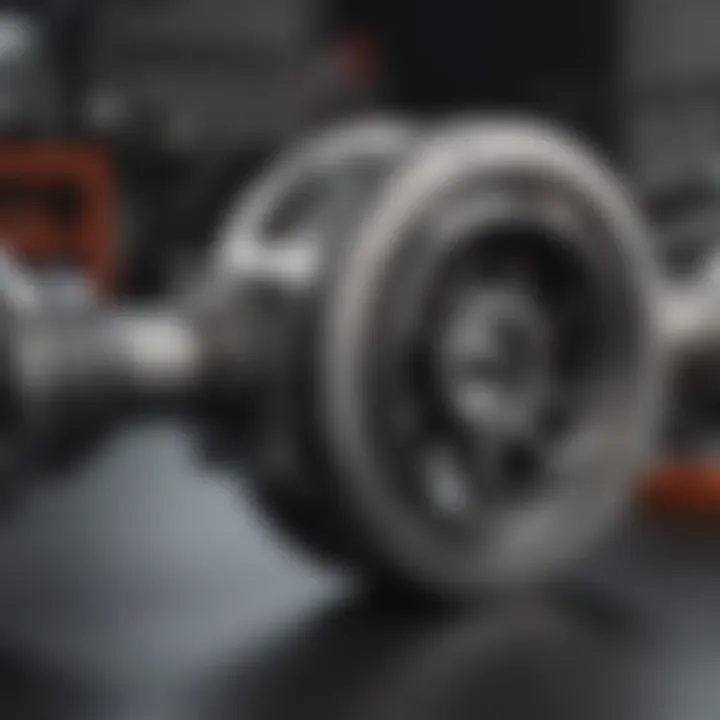
Intro
In automotive engineering, the quality and performance of components are pivotal. Among these essential parts, the crankshaft stands out. It transforms linear motion into rotary motion, playing a vital role in how engines operate. This is particularly true for high-performance engines that demand durability and efficiency. The forged 383 crankshaft is one such component that has gained traction among automotive enthusiasts.
This section serves to outline the critical attributes and functions of the forged 383 crankshaft, emphasizing its manufacturing process and distinguishing features. It examines the differences that set forged crankshafts apart from their cast analogs due to factors like fabrication methods, material selection, and resultant benefits. Understanding these aspects provides insights that can aid in achieving optimal automotive performance, especially for those venturing into aftermarket modifications.
As we proceed, we will delve deeper into how the forged 383 crankshaft enhances engine performance in various applications, making it a notable choice for both casual and professional users.
Automotive Features and Innovations
The landscape of automotive technology evolves continuously, impacting features and functionalities within engines, including the often-overlooked but crucial component: the crankshaft. This context not only encapsulates innovations surrounding high-performance engines but also reflects broader shifts within the automotive industry.
Overview of Latest Technologies
In recent years, advancements in material science have influenced the development of automotive components, particularly crankshafts. The forged 383 crankshaft utilizes high-strength steel alloys, lending it enhanced durability compared to traditional cast versions. With precision machining techniques honing these parts, a lower weight often accompanies these innovations without compromising performance metrics.
In-Depth Look at Electric/Hybrid Vehicles
While discussing forged components, it's essential to also glimpse at the growing significance of electric and hybrid vehicles. The design requirements for traditional internal combustion engines, compared to those of electric motors, diverge significantly. Understanding how innovations in performance parts can crossover into this sphere will be crucial for future applications and modifications.
Analysis of Autonomous Driving Systems
With the rising prominence of autonomous vehicles, the mechanics of high-performance components like the 383 crankshaft require analysis as well. Many changes in automotive architecture influence existing components, placing performance parts in different scenarios than traditionally encountered. Balanced consideration of these innovations is necessary for design transitions into fully automated cars.
Evaluation of AI in Automotive Solutions
Artificial Intelligence plays a transformative role in enhancing operational efficiency, particularly in the automotive workspace. The integration of AI in manufacturing processes involves predictive analysis and dynamic simulations, improving the forging and machining of crankshafts. This continuous feedback loop ensures that industry trends inform engineering advancements, fostering an environment where performance potential is consistently refined.
“The significance of quality materials in performance engineering cannot be overstated. Forged components show reliability where it matters most, especially under extreme conditions.”
The detailed approach toward understanding technologies that enhance automotive features leads directly into broader discussions to be covered in subsequent sections, contributing to a more focused perspective on aspects such as the benefits of well-designed substitution components like the forged 383 crankshaft.
Preamble to the Forged Crankshaft
The forged 383 crankshaft stands as a centerpiece in the realm of high-performance automotive engineering. Understanding its significance requires a dive deep into its characteristics, benefits, and applications. Engine efficiency, measurable durability, and overall performance improvements often hinge upon the choice of crankshaft, and the forged 383 does not disappoint in any regard.
Firstly, the method of fabrication plays a central role. Unlike cast crankshafts, the forging process involves heating and shaping metal, a technique that produces a denser and stronger end product. This strength translates directly into performance enhancements, resulting in higher power outputs and torque. Additionally, forged crankshafts can handle greater stress loads, leading to a more resilient engine, particularly under high-pressure conditions.
A common consideration in any automotive upgrade or build is compatibility. The 383 crankshaft, specifically designed for Small Block Chevy engines, exemplifies adaptability. Its construction vitally supports various applications ranging from street performance to racing dynamics, which resonates positively with automotive enthusiasts.
Moreover, while performance enhancement is critical, insights about maintenance and installation cannot be overlooked. Knowing how to properly install and care for a forged crankshaft is essential for maximizing its productivity and lifespan.
In summary, the importance of the forged 383 crankshaft is underscored by its robust performance capabilities, adaptability across different engine types, and vital role in effective automotive engineering. The following sections of this article will expand on the anatomy of a crankshaft, distinguish forged and cast options, and analyze performance characteristics—all pivotal components for anyone serious about optimizing vehicle performance.
The Anatomy of a Crankshaft
The crankshaft is a fundamental component of any internal combustion engine. Understanding its anatomy is vital for comprehending how it contributes to overall engine performance. The configuration and design significantly affect parameters like efficiency, power distribution, and tire traction. A deeper insight into the components and functionalities of a crankshaft helps automotive enthusiasts make informed decisions when selecting parts for upgrades or modifications.
Basic Components
The crankshaft consists of several crucial elements that work together synergistically. Each part has its unique role in delivering performance:
- Crank Pins: These pins connect the connecting rods to the crankshaft. They convert the linear motion of the pistons into rotational motion.
- Main Journals: These are positioned along the crankshaft where it remains supported within the engine block. They are integral to ensuring smooth rotation and minimizing wear.
- Crankshaft Throws: The throws correspond to the location of the crank pins and determine the angle of rotation, impacting the engine's firing order.
- Counterweights: These are designed to balance the rotational inertia, giving the crankshaft a smoother operation and reducing vibration.
- Flanges: These features are affixed at both ends for securing additional driveline components, such as pulleys and flywheels.
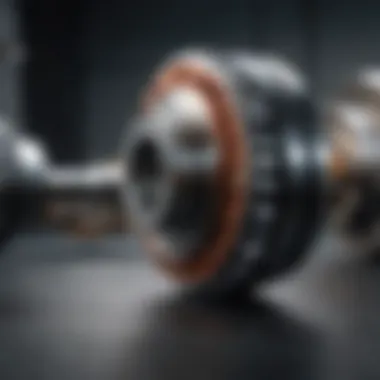
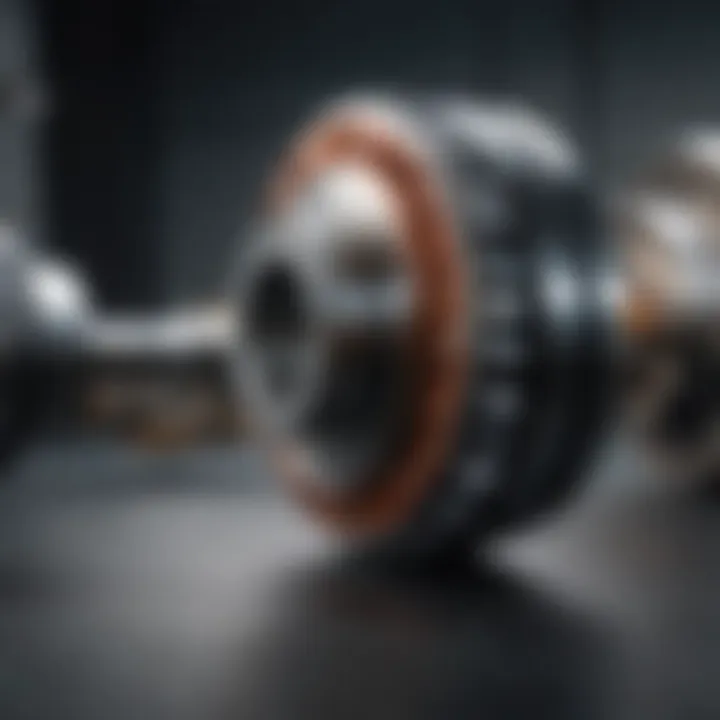
Each of these components must withstand significant forces under varying operational conditions. Hence, the choice of materials like forge steel for 383 crankshafts becomes important.
Functionality in Engine Cycles
In an engine cycle, the crankshaft plays a vital role in the conversion process essential for producing power. This process can be broken down into several stages:
- Intake Stroke: During this phase, the crankshaft rotates, allowing the piston to draw in air and fuel into the combustion chamber.
- Compression Stroke: The rotating crankshaft moves the piston upwards to compress the air-fuel mixture, increasing efficiency.
- Power Stroke: Following ignition, the rapid increase in pressure forces the piston down. The crankshaft converts this vertical movement into rotational motion, which is what ultimately drives the vehicle's wheels.
- Exhaust Stroke: Finally, the relocated crankshaft assists in expelling the burnt gases from the combustion chamber, preparing for the next intake cycle.
Overall, the crankshaft’s design dramatically influences engine responsiveness and horsepower, key factors for many automotive applications.
The efficiency of a crankshaft can significantly change the performance and experience behind the wheel.
An understanding of both the basic components and their functions in the engine cycle lays a solid foundation for choosing the right crankshaft, especially the forged variants generally known for their enhanced durability and performance.
Forged vs.
Cast Crankshafts
Understanding the distinction between forged and cast crankshafts is essential for anyone involved in performance engines. Both types serve the same basic function as part of an engine's rotating assembly, but the differences in the manufacturing process result in significant variances in strength and durability. These distinctions directly impact performance and longevity.
Manufacturing Process Overview
The core difference between forged and cast crankshafts lies in how they are created. A forge crankshaft undergoes a shaping process using high-pressure techniques that change the grain structure of the steel, providing enhanced overall strength. This method results in a tighter molecular alignment in the material.
On the other hand, cast crankshafts are produced by pouring molten metal into a mold, allowing it to solidify into the desired shape. This method is less costly and quicker compared to forging but compromises the strength and shock resistance of the final product. Therefore, while forged crankshafts are heavier on initial investment, they are often seen as more reliable for high-performance applications.
Material Strength and Durability
Material strength is one of the most compelling reasons why forged crankshafts are preferred in performance driving. The forging process produces a part that can endure higher strains and stresses typically present during racing or heavy highway driving conditions.
A forged crankshaft often features enhanced fatigue resistance, which is imperative for high-revving engines. In contrast, the smoother and more consistent structure of a cast crankshaft can experience microfractures under similar stress, leading to potential failure.
Cost Implications
Cost is always a consideration. Cast crankshafts are generally cheaper to manufacture, which makes them attractive for budget-conscious builds. However, the investment in a forged crankshaft pays off in terms of performance and reduced risk of failure.
The long-term value of forged crankshafts becomes clear when considering engine durability. They have a consistent track record of better performance under extreme conditions. In immediate terms, a forged crankshaft may cost several hundred to thousands of dollars more, but this expenditure can often save on repairs or replacements down the line, allowing for a more cost-effective approach in serious applications.
In summary, while both types of crankshafts have their place, the benefits of choosing a forged crankshaft are starkly clear for those looking for enhanced resilience, performance, and overall engine efficiency.
Specifications of the Crankshaft
Understanding the specifications of the 383 crankshaft goes beyond just numbers and figures. It encompasses aspects that affect the performance, durability, and compatibility of the engine. These specifications are critical to anyone looking to enhance engine efficiency and reliability.
Dimensions and Weight
The dimensions and weight of the 383 crankshaft play a vital role in its overall function and effectiveness. Typically, the stroke on a 383 crankshaft measures 3.75 inches. The configuration also affects how the engine will perform in different scenarios.
The diameter of the main and rod journals should also be considered. Generally, crankshafts are available with main journal diameters of 2.5 inches and rod journals of 2.10 inches. These dimensions impact the rotational mass and engine balance, essential for avoiding vibrations.
In terms of weight, a forged 383 crankshaft usually weighs around 100 to 110 pounds. This lightweight nature offers significant advantages in terms of engine responsiveness and performance, primarily when compared to heavier cast alternatives. A lower weight reduces the overall inertia, leading to improved acceleration and throttle response.
Understanding the mass and dimensions lets engine builders tailor their setups more effectively for performance goals.
It’s vital to match these specifications not just to the engine but with the overall vehicle dynamics as well. Not doing so can lead to inefficiencies or even performance setbacks. Summarizing, precise dimensioning and optimal weight are critical to maximizing performance.
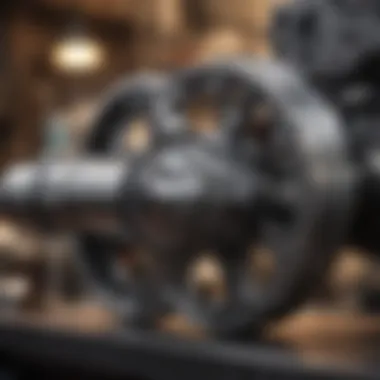
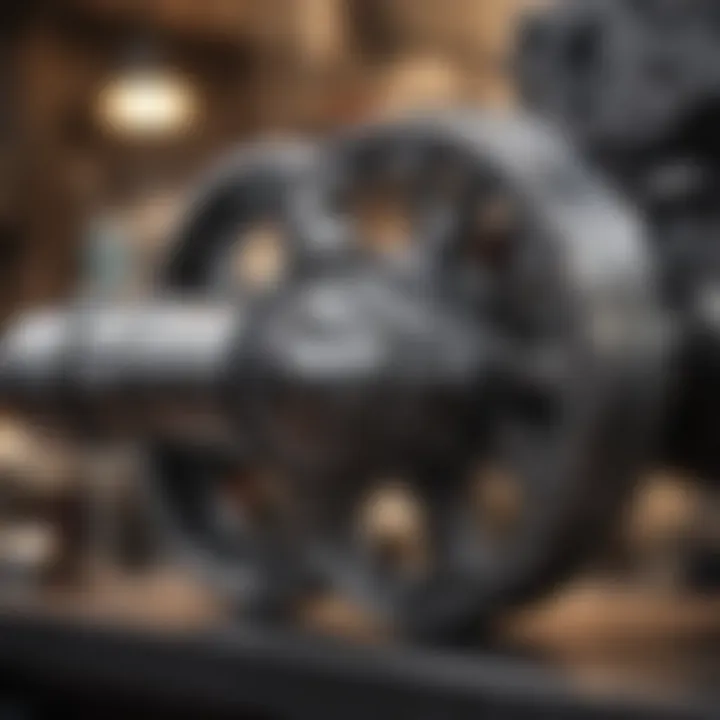
Compatibility with Engine Types
The compatibility of the 383 crankshaft is noteworthy for enthusiasts who seek to upgrade or customize their engines. The 383 can fit various block configurations, primarily the small block Chevy engines, enhancing its appeal.
When utilizing the 383 crankshaft, one must consider the specific build of the engine block. Most commonly, it is suitable for the Chevy 350, but care must be taken when implementing it into other engine platforms. Torque specifications, as well as the arrangement of components, play crucial roles in how well the crankshaft integrates within different applications.
Additionally, builders often have a choice between standard and high-performance options. This can dictate the performance limits of the setup. Remember, using a model not meant for your engine type can produce negative results, leading to potential engine failure or poor driving performance.
Performance Characteristics
Performance characteristics of the forged 383 crankshaft are paramount for understanding why this component is essential in high-performance engines. Forged crankshafts are known for their superior strength and reliability, which directly affect engine efficiency, power output, and response times. By discussing various aspects, such as power output enhancements, torque considerations, and engine responsiveness, we present a cohesive view of how these characteristics improve overall performance in automotive contexts.
Power Output Enhancements
The ability of the forged 383 crankshaft to enhance power output is one of its most significant advantages. When installed in an engine, this crankshaft allows for increased efficiency in transferring energy from fuel into mechanical motion. The improved rigidity of a forged crankshaft over a cast one means it can handle higher RPMs without risking structural integrity, thus allowing the engine to produce more power without compromising stability.
In practical terms, a high-quality forged crankshaft can contribute to an increase in horsepower metrics. For example, in performance modifications or aftermarket enhancements, using a forged crankshaft can increase the potential of the engine to push beyond factory performance limits. The result can be noticeable boosts in race or street applications where every horsepower is desired.
"Forged crankshafts deliver performance that meets both the casual driver’s expectations and the racer’s unyielding demands."
Torque Considerations
Torque is another vital performance metric where the forged 383 crankshaft plays a key role. Torque translates to the rotational force that powers the vehicle. A forged crankshaft typically enables greater torque compared to its cast counterparts, especially in low to mid-range RPMs. This characteristic can lead to sharper acceleration, offering a discernible advantage in spirited driving or racing conditions.
It’s essential to note how this crankshaft modification works in harmony with other engine components. For instance, pairing a forged crankshaft with appropriate gearing and powertrain setups amplifies torque output even further. In short, the comprehensive performance benefits become especially apparent when evaluating how a forged crankshaft interacts with overall vehicle dynamics.
Engine Responsiveness
Engine responsiveness is crucial for any performance vehicle, influencing how quickly an engine reacts to throttle inputs. The responsiveness largely depends on the mechanical stability and weight of the crankshaft. The forged 383 crankshaft's increased durability means it can maintain inertia better without significant losses.
Moreover, the structural properties inherent in a forged construction lead to a lighter-weight design that also enhances responsiveness. This design facilitates quicker acceleration and improved throttle response, leading to more engaging driving experiences. Drivers can feel subtle shifts in dynamic performance, where typical reactions might lag with cast options.
To sum up, the performance characteristics of the forged 383 crankshaft illustrate why this component remains a favored choice in the automotive performance world. By allowing greater power output enhancements, delivering higher torque levels, and fostering optimal engine responsiveness, it not only enhances enjoyment behind the wheel but also supports engine longevity and reliability.
Applications of the Forged Crankshaft
The applications of the forged 383 crankshaft are critical to its role in high-performance engines. This section outlines how this component enhances different aspects of automotive performance. By understanding its specific applications, automotive enthusiasts can make informed choices when considering performance upgrades. Forged crankshafts bring significant advantages over cast ones, including improved strength, weight reduction, and vibration dampening.
Street Performance Vehicles
Street performance vehicles benefit greatly from established durability of a forged 383 crankshaft. These engines require enhanced power output and torque, and a forged crankshaft easily meets these demands due to its robustness. Drivers looking for improved throttle response also find it valuable as the weight-to-power ratio alters positively. In street performance applications, stability at various RPM ranges proves crucial. Investing in a high-quality forged crankshaft helps optimize engine efficiency while retaining everyday driveability.
Racing Applications
In competitive racing environments, components such as the forged 383 crankshaft are often indispensable. Races require maximum performance with minimum risk of failure. The forged crankshaft’s design inherently offers greater tensile strength. Therefore, it can withstand substantial stress and high-rev situations without deformity. Reliability in harsh conditions translates to fewer failures and subsequent costs. Additionally, the light weight improves acceleration and fuel efficiency, giving racers a crucial edge on the track.
Custom Builds and Modifications
For car enthusiasts engaging in custom builds or modifications, selection of the right components is vital. A forged 383 crankshaft is often the center of performance enhancements, allowing for more power while maintaining a level of safety against potential failures. When building a high-performance engine, incorporating a forged crankshaft is necessary for compatibility with other upgraded parts such as forced induction systems.
Always remember that working with high-performance engines requires similar considerations around balance and alignment, especially as added power leads to additional forces that could influence other components. This trade-off means investing extra time in installation will eventually yield better-engineered results.
“In modifying vehicles, the choice of crankshaft can make or break the entire build.”
Installation and Maintenance
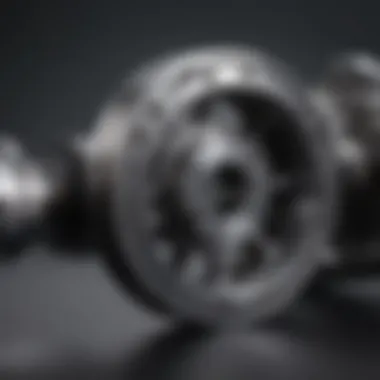
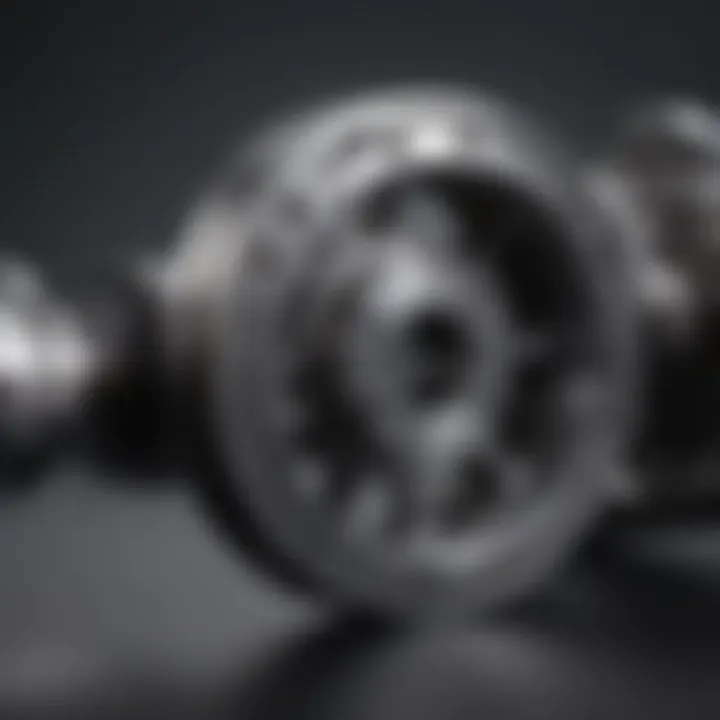
Installation and maintenance of the forged 383 crankshaft are pivotal for a high-performing engine. Proper installation ensures the crankshaft operates smoothly and seamlessly with the engine components. In contrast, neglecting installation best practices can lead to performance issues, unnecessary wear, or even catastrophic failures. Therefore, automotive enthusiasts must pay attention to detail in both processes.
The ongoing maintenance of the crankshaft post-installation also warrants discussion. Routine checks and maintenance can significantly extend the lifespan of this component. It not only enhances performance but also contributes to overall engine efficiency. Below, we delve deeper into best practices and maintenance tips that can assist in maintaining the integrity of the forged 383 crankshaft.
Installation Best Practices
To achieve optimum performance and longevity from a forged 383 crankshaft, adhering to the correct installation procedures is essential. Key practices include:
- Clean the Engine Block: Before installation, ensure that the engine block is clean. Any debris can affect the sealing and function of the crankshaft.
- Use Quality Components: Invest in quality bearings and lubrication. This allows for smooth operation and minimizes wear.
- Follow Torque Specifications: Adhere to the manufacturer’s torque specs for all bolts involved in the installation. This ensures the crankshaft sits properly and is properly aligned.
- Check Alignment: Ensure the crankshaft is properly aligned with the surrounding components. Misalignment can lead to premature wear or damage.
- Inspect Before Sealing: Always inspect the crankshaft before sealing. Look for dents, scratches, or any form of wear.
These installation practices, while essential for the** new crankshaft, should also be reviewed if removing and re-installing during repairs or upgrades.**
Routine Maintenance Tips
Maintaining a forged 383 crankshaft involves simple yet effective practices that prevent unforeseen problems:
- Regular Oil Changes: Consistent oil changes help lubricate the crankshaft and prevent sludge build-up. Always use the engine oil recommended by the manufacturer.
- Inspection of Components: Regularly inspect connecting rods, bearings, and seals for wear. Ensure that no detritus interrupts the crankshaft function.
- Monitoring Engine Performance: Be attuned to any changes in engine performance, such as unusual sounds or vibrations. These could signal issues with the crankshaft.
- Keep the Engine Cool: Exposure to excessive heat hinders performance. Use a reliable cooling system and ensure functionality to protect the crankshaft and the entire engine assembly.
Following these tips can help ensure the longevity of the forged 383 crankshaft, solidifying its position as a key element in high-performance engines.
Regular maintenance is designed to avoid costly repairs later, ensuring reliability as well as enhanced engine performance.
Automotive enthusiasts and mechanics should make these practices a regular part of their routines to protect their investments and keep their vehicles performing at optimal levels.
Future Trends in Crankshaft Design
The landscape of crankshaft design continues to evolve, driven mainly by advancements in performance requirements and material technologies. In this section, we will examine key trends that are shaping the future of crankshafts, focusing specifically on the forged 383 model, which is essential for achieving high performance and durability.
Advancements in Materials Science
Material science has seen significant innovations in recent years. One crucial trend is the use of lightweight, high-strength materials that enhance both performance and durability in forged crankshafts. These advancements include:
- Alloyed Steels: The development of specialized steel alloys provides a balance between weight and strength. The composition can be tailored to withstand higher stress loads while minimizing fatigue failure.
- Titanium Alloys: Though more expensive, titanium offers excellent strength-to-weight ratios. This material is particularly attractive for racing applications where every gram counts in performance metrics.
- Composite Materials: Emerging technologies in composites may allow integration into crankshaft design. These materials can potentially leverage both strength and weight benefits, although they require more research before full adoption in high-demand applications.
The evolution of these materials leads to crankshafts that are not only stronger but also lighter, contributing to improved engine efficiency and power output.
Technological Advances in Manufacturing
Manufacturing technologies in crankshaft production are accelerating at a rapid pace. The methods currently being adopted transform how forged crankshafts are made, which offers exciting prospects for the industry. Consider:
- 3D Printing: This technology allows for precise control over the design and manufacturing process. With 3D printing, complex geometries that maximize performance can be achieved without the restrictions of traditional manufacturing.
- CNC Machining: More manufacturers are using Computer Numerical Control (CNC) to improve accuracy and efficiency during crankshaft machining. This leads to better surface finishes and dimensional accuracy, ensuring that forged crankshafts are of the highest quality.
- Robotics in Assembly: Automation is increasingly utilized in assembly processes. This can reduce human error, enhance production speeds, and ensure consistent quality across the manufacturing line.
While these trends are notable, adhering to precision engineering and maintaining high quality remains essential. With time and investment, these technological advances promise to revolutionize crankshaft production, ultimately benefiting the performance and reliability of high-performance engines.
“The integration of advanced materials and manufacturing technologies signifies a paradigm shift in automotive engineering, crucial for maximizing performance in modern engines.”
Epilogue
In summarizing the discussion about the forged 383 crankshaft, its critical role become evident in both performance enhancements and longevity of high-performance engines. Throughout this article, we have shed light on aspects governing design, materials, and their resulting benefits. The forged 383 crankshaft is engineered from premium-grade steel, effectively increasing tensile strength compared to traditional cast crankshafts.
Main Points Addressed:
- Manufacturing Techniques: As observed, forging offers a structural integrity not present in cast alternatives. This also increments durability and overall resilience under stress.
- Performance Attributes: Enhanced power output and torque deliver impressive responsiveness, a key expectation for many performance-oriented endeavors.
- Versatile Applications: The discussions encompass its application in various segments, notably street performance, racing, and custom builds. This versatility extends across broad user bases, whether amateurs or seasoned professionals.
After understanding these elements, consideration of a forged 383 crankshaft goes beyond just a choice; it aligns with a commitment to quality and efficiency. In the dynamic landscape of automotive engineering, where each component plays a pivotal role, investing in a forged crankshaft signifies foresight into robust performance product. Evaluation of cost versus longevity from high-quality synthetics should also contribute to decision-making process ensuring value remains intact over extended use.
In closing, the insights presented form a solid grounding for automotive enthusiasts, from novice car owners to seasoned professionals. Given this understanding, the fabricated nature of the crankshaft emerges not merely as a choice for strength but a cornerstone for enhancing vehicle potential. Engaging with the content within this article grants not just knowledge but strategic approach, geared to elevate subsequent performance installations.
"Selecting the right crankshaft is a decision that shapes your vehicle's entire performance landscape."
This arms you with the clarity necessary to confidently navigate the automotive domain.