In-Depth Guide to the LQ4 Forged Rotating Assembly
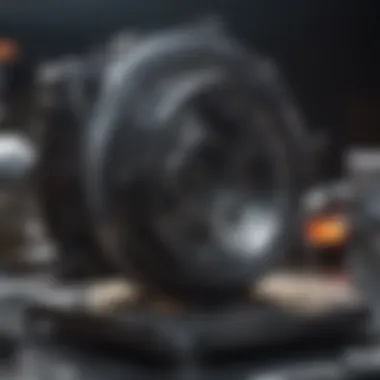
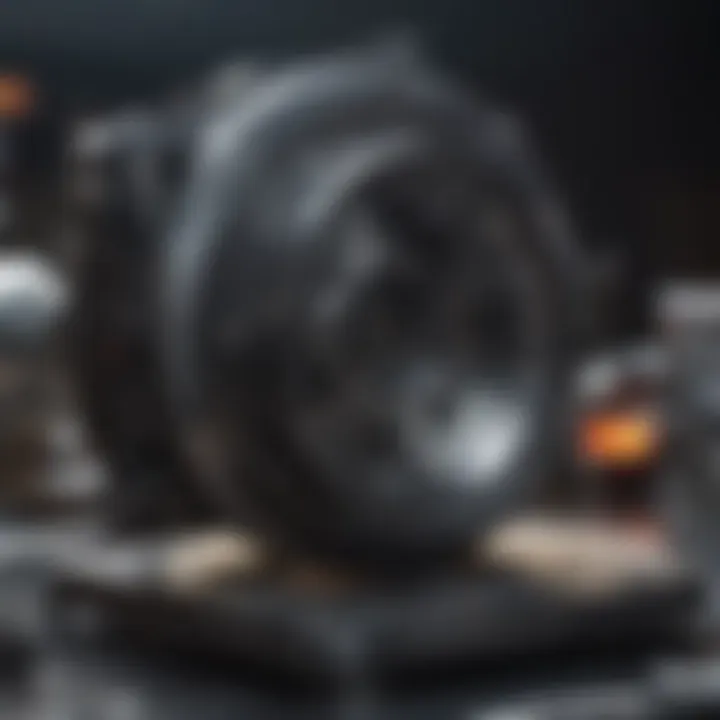
Intro
The LQ4 forged rotating assembly stands as a cornerstone in automotive performance, notable for its reinventive engineering. This piece shifts its focus onto the inner workings of this assembly, analyzing not just the specifications but also what sets it apart from other components on the market. Understanding the LQ4's design is essential for those looking to reinvigorate or precisely optimize engine performance.
The automotive scene, filled with both conventional combustion engines and emerging technologies, makes knowledge of specific assemblies imperative. This guide expects to equip automotive enthusiasts, professionals, as well as students with the depth of understanding they seek.
Automotive Features and Innovations
Overview of Latest Technologies
Recently, advancements in materials and engineering processes have greatly influenced the manufacturing of assemblies such as the LQ4. The incorporation of forged steel has enhanced not only strength but also performance potential. Innovations like CNC precision machining have minimized tolerances leading to improved balance and reduced wear.
In-Depth Look at Electric Vehicles
Although this piece primarily focuses on the LQ4βs rotary dynamics, the electrical sector is hard to ignore. With electric and hybrid technologies gaining traction, the knowledge of conventional system components lays groundwork for understanding alternative power sources. Components like the LQ4 marble the gap toward high-performance electric systems.
Analysis of Autonomous Driving Systems
The advent of autonomous technology is categorically reshaping automotive designs. Strike a comparison with LQ4's relevance; cohesive performance means possibly compatible history with emerging autonomous driving configurations, for a smooth transition in vehicle ecosystems.
Evaluation of AI in Automotive Solutions
From manufacturing to smart driving systems, AI has influenced how components, including stitched assemblies like the LQ4, interact live. This intelligent innovation is paving potential for optimized engine efficiency through predictive algorithm-driven maintenance strategies.
Maintenance Tips and Best Practices
Keeping a LQ4 assembled engine in prime condition requires methodical care. Certain practices greatly smooth the operation and enhance longevity.
Regular Maintenance Schedules
Adhering to a regular maintenance schedule is non-negotiable. Frequent oil changes and inspections at set intervals protect against unnecessary wear.
DIY Repair Guides
There exists a growing community focused on DIY repairs and installations. Connecting to resources like forums on Reddit encourages salvaging essential components without extensive professional help.
Seasonal Car Care Strategies
Different environments demand varied approaches. Cold weather may result in different fluids clagg in a forged assembly, testing its limits. Every season might mean a perspective change on maintenance.
Addressing Common Issues and Solutions
Before attempting more significant repairs, consider diagnostic readings via an OBD-II scanner. Knowing how your LQ4 behaves under loads can help preempt disasters.
Trends in Automotive Industry
Market Analysis and Forecasts
The automotive industry continues bustling, driven by competitiveness in the engineered domains. Understanding trends within these markets provides insight essential for decisions of both consumers and producers alike.
Electric Vehicle Adoption Rates
The surge of electric vehicle adoption particles the path forward. A careful analysis highlights that engagement in efficient component design may yield favorable outcomes alongside transitions.
Growth of Ride-Sharing and Mobility Solutions
Mobility lifestyles are increasingly rooted in previously unseen collaborative mindsets across manufacturers. Understanding aging components may yet support evaluations on how conventional engine assemblies proceed towards a new mobility-centric structure.
Consumer Preferences Shifts and Impacts
Consumer preferences broaden like never before. Assessing modifications on love affairs with cars can produce further understanding of LQ4's relevance across versatile buyer disengagements.
Educational Resources
Technical Knowledge Base
The LQ4 assembly is but a fraction of engineer thought processes. After all, education in the automotive realm forms the fundamentals for future dive into sophisticated transitions.
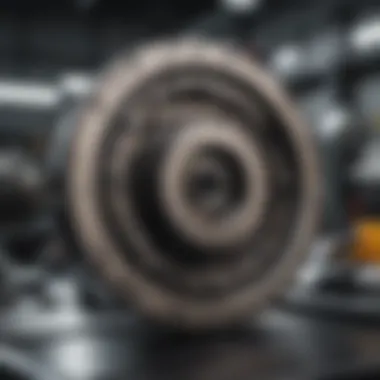
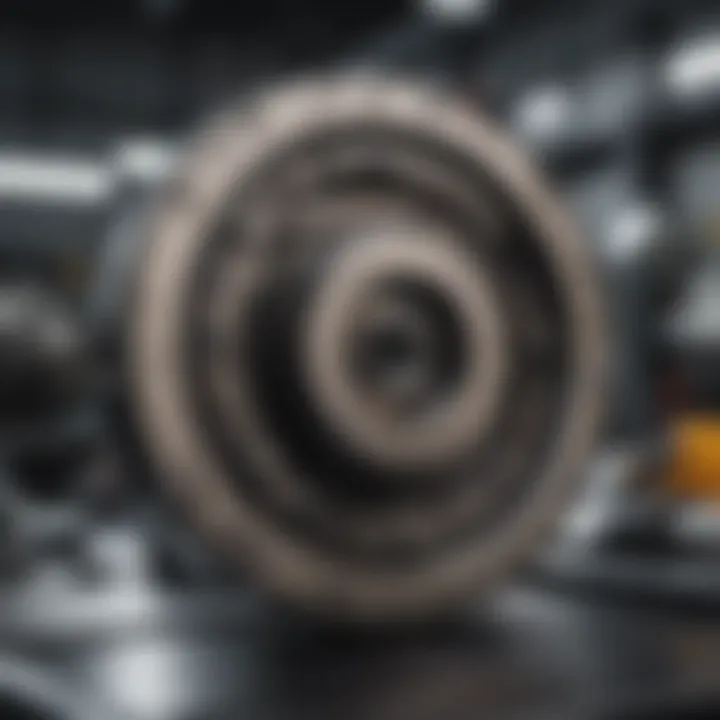
Insights Into Automotive Engineering
As vehicle dynamics evolve, so does the technology shaping them. Instructional resources offered both academically and through mediums like blog posts reliably furnish skills necessary for an acute understanding of components such as the LQ4.
Certifications and Training Programs
With proper certifications, forward-thinking individuals find themselves extending knowledge borders into the fascinating language of performance assemblies. Thus subscribing into workshops could heighten skill areas while engaging new areas within automotive engineering.
Future Trends in Automotive Education
Education in furture developments supplements the craft relentlessly, leading practitioners on a guided path toward ever-visible potential in automotive engineering.
The amalgamation of curiosity in engine performance and innovation management provides a sufficient stimulus for a deep appreciation of mechanical dexterity.
Prelims to the LQ4 Forged Rotating Assembly
The LQ4 forged rotating assembly occupies a crucial position in high-performance automotive engineering. It serves as the heart of the LQ4 engine, fundamentally impacting performance and reliability. Understanding its components and how they work together is essential for enthusiasts and professionals who seek enhanced engine output and efficiency.
Overview of the LQ4 Engine
The LQ4 engine, a member of the General Motors Gen III/IV small block engine family, is notable for its displacement of 6.0 liters. This powerful engine features aluminum or iron construction, which makes it synonymous with durability and power. Coupled with its sophisticated electronic control mechanisms, it offers dynamic adjustments to fuel delivery and ignition timing, resulting in improved fuel economy and more responsive performance. The LQ4 also has robust aftermarket support, attracting a wide variety of applications ranging from street performance builds to specialized racing setups.
Importance of Rotating Assemblies in Engines
Rotating assemblies are critical components in any internal combustion engine. They play a significant role in the overall performance, efficiency, and longevity of the engine. The four primary elements of a rotating assembly include the crankshaft, connecting rods, pistons, and sometimes the flywheel. Each part must work in sync to withstand the pressures and stresses generated during engine operation. The primary benefits of a well-designed rotating assembly are reliable power delivery and enhanced structural integrity.
- Increased power capabilities
- Enhanced durability under extreme conditions
- Reduced weight for improved speed and agility
A balanced rotating assembly leads to smooth engine operation. Any discrepancy in component performance can lead to issues such as vibrations or premature wear. Therefore, the necessity for upgrading to a forged rotating assembly becomes apparent, as each component is purpose-built for high stress and demanding performance applications.
A forged rotating assembly has superior longevity, allowing engines to perform optimally across a wide range of conditions.
Components of the LQ4 Forged Rotating Assembly
The components of the LQ4 forged rotating assembly play a vital role in optimizing engine performance and reliability. Each element is meticulously designed to ensure maximum efficiency, reduced weight, and enhanced durability. The proper function and integration of these components are crucial, especially for high-performance applications. In this section, we will examine the key components: the forged crankshaft, forged connecting rods, and forged pistons, discussing their importance, unique properties, and benefits in the LQ4 assembly.
Forged Crankshaft
The forged crankshaft is the backbone of the LQ4 engine. It converts reciprocating motion into rotary motion. Made from high-strength materials, this crankshaft is designed to withstand high-energy conditions. Unlike cast cranks, forged crankshafts offer superior tensile strength and resilience under stress.
Upgrading to a forged crankshaft minimizes flexing and vibration during operation. This upgrade is especially beneficial in racing and high-performance scenarios. Forged crankshafts typically have improvements in hardness and surface finish compared to their cast counterparts, thus enabling better horsepower and torque performance.
In summary, a forged crankshaft is crucial for engine builders aiming for enhanced performance and increased durability. It represents one of the primary strengths of the LQ4 assembly.
Forged Connecting Rods
Forged connecting rods in the LQ4 engine ensure efficient power transfer from the pistons to the crankshaft. They experience immense forces during combustion and must be designed to handle these stresses. Forged connecting rods have a greater strength-to-weight ratio than cast ones. This translates into quicker acceleration, smoother power delivery, and overall improved engine response.
Itβs essential to pay attention to the specifications regarding length and weight. Shorter, lightweight rods can reduce the overall inertia of the moving assembly, allowing higher RPMs. These rods also minimize engine wear, leading to enhanced engine longevity. Consequently, they are well-suited for performance vehicles and racing applications.
The joints and bearings must also be maintained correctly, as improper care can lead to failures that terminate engine performance. Regular checks and balances are a must for those using forged connecting rods.
Forged Pistons
The forged pistons are a vital part due to their role in sealing combustion gases and withstanding high pressures and temperatures. Unlike cast pistons, forged pistons typically exhibit improved thermal properties and can be designed to exact specifications, ensuring a perfect fit within the cylinder bores.
They also promote better power output because of their enhanced combustion chamber dynamics. Forged pistons can enhance fuel efficiency by achieving a better air-fuel mixture. This leads to a cleaner combustion process and reduced emissions.
The material choice plays a fundamental role here too. Generally, forged aluminum is preferred for its lightweight yet strong nature. This contributes to reduced internal engine friction, which optimizes throttle response.
Overall, adopting forged pistons is a significant step in maximizing not only the performance of the LQ4 engine but also its reliability and operating efficiency over time.
Understanding these components is crucial for engine enthusiasts looking to enhance performance. Poor-quality components can negate the benefits described and lead to engine failures, reinforcing the importance of choosing well-made forged components for the whole assembly.
Benefits of Upgrading to a Forged Rotating Assembly
Upgrading to a forged rotating assembly represents a significant investment in performance and reliability for any engine, including the LQ4. As automotive technology evolves, the expectations for power and durability continue to rise. Understanding the benefits of such an upgrade is essential for enthusiasts who wish to optimize their vehicle's performance. The following sections will dissect key advantages including increased strength and durability, improved performance under high-stress conditions, and enhanced engine longevity.
Increased Strength and Durability
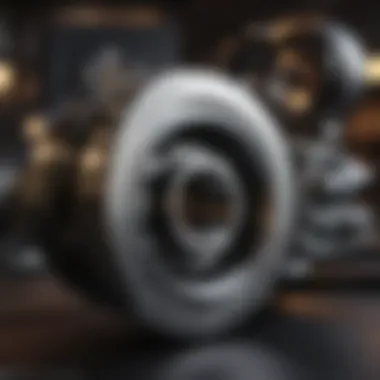
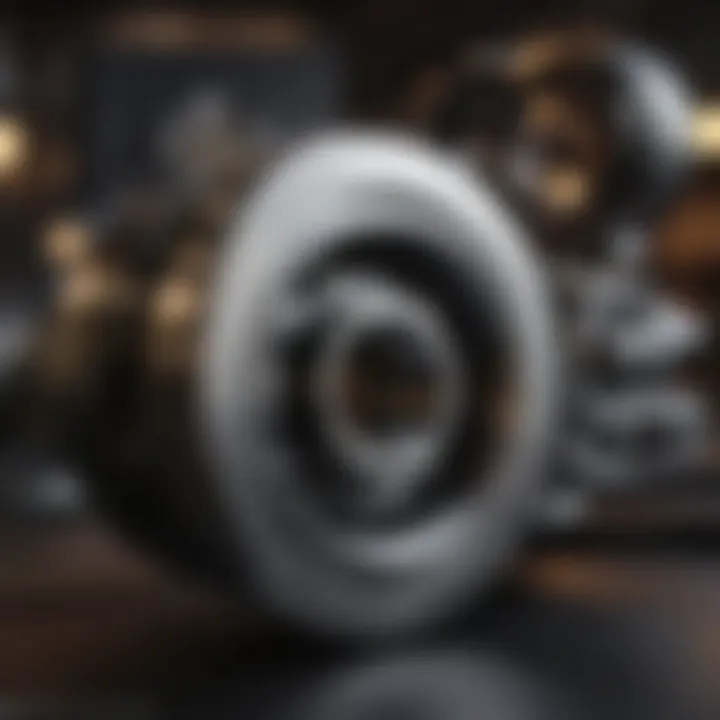
The difference in strength between forged and cast rotating assemblies is considerable. A forged rotating assembly, through its manufacturing process, offers denser material that withstands extreme stress. When looking at the LQ4, incorporating forged components results in reduced chances of failure, particularly under high horsepower applications.
- Material Benefits: Forged assembly undergoes processes that align its molecular structure, providing superior resistance to fatigue. This results in a part better suited for demanding environments.
- Performance Under Load: As RPM increases, the forces acting on the rotary components also rise. A forged assembly is designed to manage these forces more effectively than cast parts.
With these enhanced characteristics, automotive enthusiasts can enjoy modifications that push the limits without compromising the integrity of their engines.
Improved Performance in High-Stress Conditions
High-stress scenarios are commonplace in many applications ranging from daily driving to competitive racing. Forged components shine in these conditions via remarkable stress tolerance. The LQ4 engine, particularly when equipped with such parts, demonstrates substantial improvement in acceleration and throttle response under demanding conditions.
- Optimized Torque Delivery: The rigidity from a forged assembly allows for better energy transfer from combustion without losses to part flexing.
- Elevated Rev Limits: Owners looking to maximize RPM can do so with added confidence in their rotating assembly's capability.
Drivers can expect an immediate boost in performance metrics; the increased efficiency not only enhances speed but also expands versatility across applications.
Enhanced Engine Longevity
Investing in a forged rotating assembly aids significantly in prolonging engine lifespan. Each component of the assembly is designed with endurance in mind, translating into less wear and lower frequencies of repair. Regular wear factors such as heat and mechanical forces are managed more effectively by forgings enhancing the engine's overall life.
- Minimized Heat Generation: Quality materials dissipate heat better, which in turn leads to lower operational temperatures, preventing thermal fatigue.
- Resilience Against Oils: Forged assemblies are less prone to oil starvation issues, an important factor for longevity, especially for performance applications.
Engines that undergo these upgrades demonstrate impressive durability. This results in fewer breakdowns and decreased servicing costs that provide not only emotional benefits of driving but also financial reasoning.
"Investing in forged components offers unparalleled performance and longevity, thus paying off substantially over the vehicle's life."
In sum, upgrading to a forged rotating assembly in the LQ4 engine is not just a performance enhancement but a strategic decision to ensure engine longevity and resilience. These crucial benefits prime the engine for better performance while safeguarding against the operations of everyday demands.
The Iaqff4 SWOT information enables insight intoindividual, lolian truck check-parts would benefit significants performance, leslie quality trergating this union credibility-le. Considering merely performance, enthusiasts fo checking operates complimentary fornaitional consideration ached delivering navigate appreciating through skilled known resolution.
Installation Considerations for the LQ4 Forged Rotating Assembly
The installation process is a critical aspect of utilizing the LQ4 forged rotating assembly effectively. Understanding the installation considerations ensures optimal performance of the engine. A methodical approach can greatly enhance the longevity and reliability of your assembly. Below, we will explore specific tools required, detailed steps to achieve a proper installation, and list common mistakes to avoid.
Required Tools and Equipment
Having the proper tools is paramount for a successful installation of the LQ4 forged rotating assembly. Here is a list of essential equipment:
- Torque Wrench: Useful for applying the correct torque when tightening bolts.
- Engine Stand: Provides a stable working surface.
- Assembly Lube: Ensures smooth operation by reducing friction during initial startup.
- Main Cap Bolts: Obtain several new bolts to secure the assembly firmly.
- Engine Hoist: To assist in lifting and positioning heavier components.
- Socket Set: Required for various fasteners throughout the installation.
- Jack and Jack Stands: Necessary for raising and securely supporting your vehicle.
- Dial Indicator: Guarantees precise measuring of the crankshaft.
Appropriate selection and care of tools can prevent unnecessary damage and frustration during the installation process.
Steps for Proper Installation
Following a step-by-step approach ensures the installation process goes smoothly. Here are key steps to follow:
- Preparation: Begin by thoroughly cleaning the engine block and all components to remove any debris and contaminants.
- Align and Install the Crankshaft: Carefully place the crankshaft in the block ensuring proper alignment with the main bearings.
- Connect the Main Caps: Secure the main caps using new bolts and tighten to the manufacturer specifications with a torque wrench.
- Install Pistons and Connecting Rods: Insert each piston and connecting rod into its respective cylinder, using a lubrication on the upper parts to avoid initial wear.
- Configure Timing Components: Properly align camshaft and timing chains, ensuring no slack while fitting.
- Final Assembly Checks: After everything is in place, double-check that all components are secured and none are out of said specifications.
Each of these steps is fundamental to ensuring an effective and efficient installation process.
Common Mistakes to Avoid
Awareness of potential pitfalls can save time and reduce costly errors. Here are some common mistakes to steer clear of:
- Ignoring Lubrication: Failing to lube moving parts can lead to substantial engine wear during the initial startup.
- Over-Torquing Bolts: Pushing bolts beyond recommended torque can result in component damage or failure.
- Mismatched Components: Ensuring parts are compatible is essential for functionality.
- Neglecting Clearances: Inadequate measurement of tolerances can lead to interference between engine components.
- Skipping Alignment Checks: Wrong alignments can cause significant operational issues down the line.
Each listed pitfall can hinder performance or contribute to premature failure of the assembly.
Understanding and addressing these aspects of installation humanizes a complex process. Proper installation is integral for performance and longevity of the LQ4 forged rotating assembly.
Maintenance of the LQ4 Forged Rotating Assembly
Maintaining the integrity of the LQ4 forged rotating assembly is crucial for maximizing performance and ensuring engine longevity. Neglect can lead to considerable damage or failure, impacting both the engine and the overall vehicle functionality. Therefore, understanding maintenance protocol yields better reliability and performance in the long run.
Routine maintenance inspections not only allow for early detection of potential issues but also extend the life of engine components. Further, adhering to proper lubrication practices plays a significant role in minimizing friction and wear.
Routine Checks and Balancing
Regular checks are essential in maintaining the performance of the LQ4 forged rotating assembly. Monitoring engine vibrations and using a dial indicator can help identify imbalances that may occur. Addressing these imbalances early can prevent premature wear of the rotating components, including the crankshaft, connecting rods, and pistons.
Run the engine at different speeds to observe for changes in vibrations. It is beneficial to check other related elements, like motor mounts and transmission, to ensure everything is operating smoothly together. Regular checks can improve the function of the rotating assembly, leading to more efficient performance and reduced wear and tear.
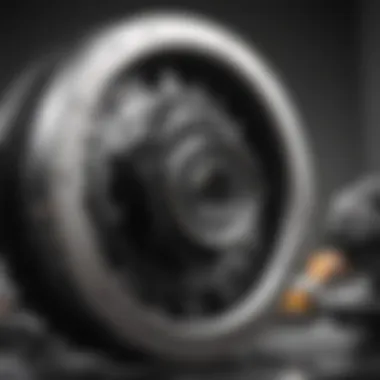
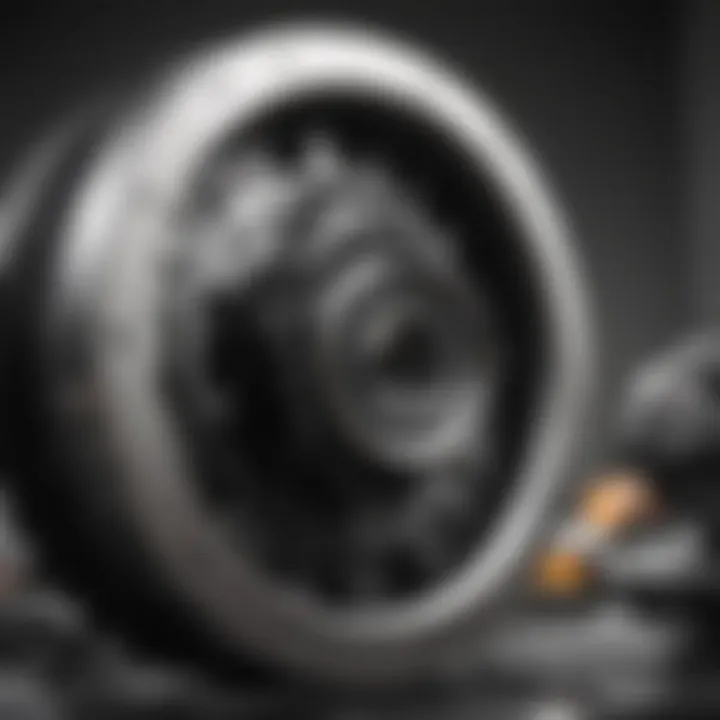
Lubrication Requirements
Proper lubrication is indispensable for any engine. In the context of the LQ4 forged rotating assembly, the oil serves multiple purposes: reducing friction, keeping temperatures manageable, and removing slide debris. Non-compliance with lubrication requirements can result in severe long-term effects, like total engine failure.
- Oil Type: Use premium synthetic oils for_ better protection_ and operational efficiency. Items such as Mobil 1 or Royal Purple are excellent examples.
- Oil Change Interval: Regularly change oil at intervals no longer than 5,000 to 7,500 miles, depending on driving conditions.
- Checking Oil Levels: It should be a usual practice to check oil levels weekly or before long trips.
Remember that external components impacting lubrication must be properly maintained. If the oil pump fails to deliver adequate strain, it does not matter if the oil type is superior; the outcome will still be detrimental.
Signs of Wear and Tear
Being able to identify signs of possible wear and tear is vital for intervening before significant problems arise. Warning indicators can often signal the need for immediate attention. Key signs to repay attention to are:
- Unusual Noise: A clattering or knocking sound when the engine runs indicates that something is awry.
- Excessive Oil Consumption: If the oil is burning quickly or leaking, it forms a brush stroke merrily pointing towards serious concerns.
- Check Engine Light: If it illuminates consistently, proceed to have it diagnosed promptly.
Implementing routine maintenance checks, proper lubrication methods, and promptly addressing wear-and-tear signs can ensure that your LQ4 forged rotating assembly performs efficiently throughout its life.
Regular maintenance can proactively reduce costly repairs and result in enhanced performance.
Comparison: Forged vs.
Cast Rotating Assemblies
Understanding the distinctions between forged and cast rotating assemblies holds immense significance in automotive performance. Each type of assembly presents unique characteristics, which influence strength, durability, and cost. This topic warrants careful attention for both automotive enthusiasts and professionals eager to optimize engine functionality.
Material Properties and Performance
When evaluating the materials of rotating assemblies, forged components often stand out for their superior mechanical properties. Forging increases the strength of materials due to the alignment of the grain structure. This yields parts that can withstand greater pressures and stresses. Conversely, cast assemblies, while generally cheaper to produce, exhibit properties that are significantly less robust under high-load conditions.
- Strength: Forged rotating assemblies typically have higher tensile and yield strength than cast components. This allows for greater performance and safety, especially in racing and high-performance applications.
- Weight: Precision in the machining process can often make forged components lighter than cast. A lower weight can enhance performance, improving both acceleration and handling.
- Durability: In demanding environments, forged parts resist deformation better than cast alternatives, giving them a longer lifespan under stress.
It is critical to note that while cast components can be sufficient for mild applications, they are often susceptible to failure under extreme workloads. Forged assemblies afford peace of mind where performance is non-negotiable.
Cost Considerations
Many buyers must balance their decision on the types of rotating assemblies with budget constraints. Generally, the manufacturing process for forged parts is more costly and complex compared to casting. This stems from the need to apply high heat and pressure in the formation of forged materials.
Despite the higher upfront costs, the long-term advantages provided by forged assemblies frequently justify the investment. New purchasers should carefully assess the total costs, considering factors like:
- Initial Pricing: The purchase price for forged assemblies is noticeably higher. However, this should be seen in the context of lifetime performance gains.
- Longevity: Lampered components tend to have a lower risk of failure, potentially leading to reduced maintenance and replacement costs.
- Performance Enhancements: Forged parts enable enhanced performance capabilities, appealing to those who prioritize speed and reliability.
Ultimately, these cost metrics favor forged rotating assemblies for individuals and businesses requiring outstanding dependability and extreme outputs.
Forged rotating assemblies serve as a long-term investment for high-performance applications, where performance and reliability are paramount over initial costs.
In the automotive realm, analyzing various aspects of material properties and cost considerations is essential for savvy consumers seeking optimized performance in their engines.
Market Trends Related to Rotating Assemblies
The landscape of automotive engineering is ever shifting, with market trends influencing the design and application of rotating assemblies. Understanding these trends is crucial for enthusiasts and professionals. It not only informs component purchases but also aligns with technological advancements and consumer demand within the industry.
Emerging Technologies
The advancement of technology beautifully encapsulates the potential offers manufacturers employ when designing forged rotating assemblies. Innovations in materials science have resulted in lighter, stronger alloys. These newer materials often boast improved tensile strength and fatigue resistance, improving the overall durability of the engine when subjected to high-stress conditions.
- Additive Manufacturing: This computer-aided design technique allows for more intricate component geometries that were not previously feasible. Manufacturers can ruin prototypes quickly and refine parts comprehensively. This process aims generally to reduce oil usage and weight further.
- Advanced Coatings: Coatings such as thermal barriers or friction-reducing materials are becoming more commonplace, leading to enhanced performance. By integrating these coatings within the engineering process, tool life extends and the necessary maintenance oversight diminishes.
- Smart Engines: The integration of AI and machine learning brings a smart approach to engine management. Sensors placed on forged rotating assemblies can now provide crucial performance metrics, identifying the necessary maintenance needs in real-time, greatly enhancing engine reliability and efficiency.
As these technologies continue to advance, we will see a stronger push towards more efficient material use and technologies supporting ongoing improvements in engine performance.
Consumer Preferences
Consumer behavior shapes how manufacturers develop their products. Todayβs automotive buyers demand higher performance, fuel efficiency, and quality. There is a growing cohort favoring performance tuning and aftermarket parts.
- Rise in Performance Focus: Customers increasingly consider upgraded parts to maximize engine output. Performance enthusiasts seek rotating assemblies that allow for better power and turbine response times.
- Sustainability: An uptick in environmental awareness is pushing users to favor suppliers that employ sustainable practices. This includes utilizing materials that decrease environmental impact or are generally recyclable or biodegradable.
- Long-Term Investment: Many automotive consumers are willing to invest upfront in quality rotating assemblies believed to offer long-term durability. They see this choice as a wise decision rather than simply a temporary boost.
The End
The conclusion of this article serves as a vital reflection point on the LQ4 forged rotating assembly. It connects the details discussed about components, performance enhance, and installment considerations. The relevance of this topic is significant within the automotive arena, as it underscores the impact of upgraded assemblies on overall engine functionality and durability.
Summary of Key Points
- The LQ4 forged rotating assembly is a critical upgrade for aftermarket performance.
- Each component, from the crankshaft to the pistons, plays a pivotal role in enhancing engine strength and efficiency.
- Installing a forged rotating assembly offers distinct advantages over standard cast options, particularly in high-stress environments like racing.
- Maintaining this assembly necessitates regular checks to ensure optimal function and longevity.
Future of Forged Rotating Assemblies
The future of forged rotating assemblies is likely to witness continued advancements fuelled by emerging technologies. With automation in manufacturing processes, forming precision-designed forged parts will only get better. As performance vehicles evolve, so too do the expectations for reliability and power output. Moreover, customer preferences will influence innovation in this domain. Enthusiasts now prioritize standardized options that can achieve greater horsepower without compromising the durability.