In-Depth Insights on Sheet Metal for Car Flooring
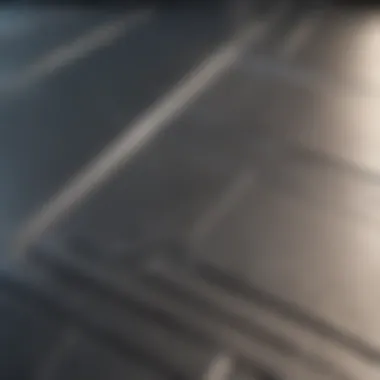
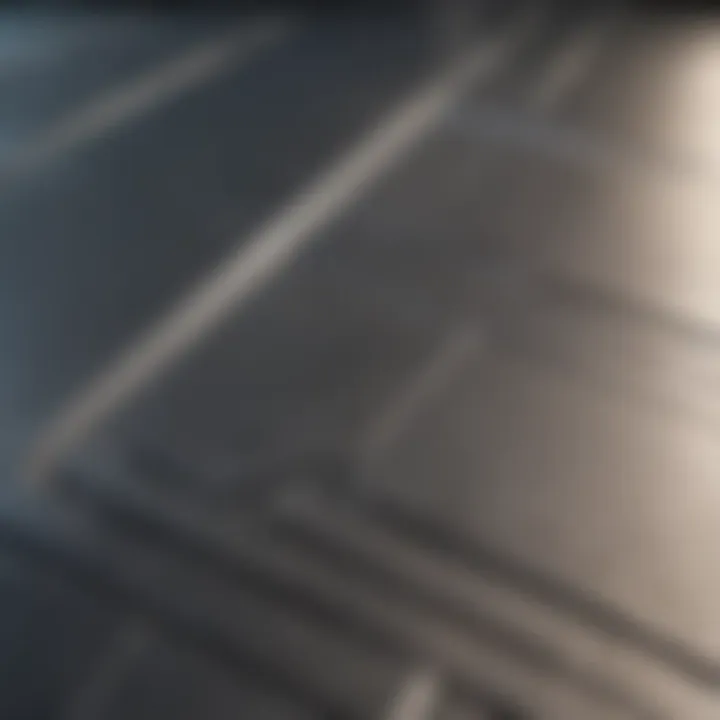
Intro
The use of sheet metal for car floors represents a fundamental aspect of automotive engineering. Its characteristics and applications are crucial for understanding vehicle safety, design, and overall functionality. This discussion outlines key points that define sheet metal's impact in the automotive industry, providing insights relevant to car owners, enthusiasts, and those involved in automotive education.
Automotive Features and Innovations
Overview of Latest Technologies
The realm of automotive sheet metal has experienced significant advancements due to the introduction of innovative technologies. For instance, high-strength steel and various aluminum alloys present improved durability while contributing to reduced weight. These materials enhance fuel efficiency and bolster crash safety, addressing the industry's evolving regulatory and consumer demands.
In-Depth Look at Electric/Hybrid Vehicles
In electric and hybrid vehicles, sheet metal construction not only underpins the car floor but also serves to shield the battery systems and electronic components. The demand for lightweight materials in this category illustrates how critical introducing advanced manufacturing techniques is to optimize performance. Many manufacturers employ techniques such as advanced laser welding and innovative stamping processes, which further aid in achieving the precision required in this high-tech segment.
Analysis of Autonomous Driving Systems
As the automotive industry ventures into autonomous driving, sheet metal's role evolves once again. Structural fortifications via strategic placements of sheet metal contribute to both crash safety and sensor support. Planners incorporate these critical elements to ensure vehicle safety and reliability.
Evaluation of AI in Automotive Solutions
Artificial intelligence is fundamentally changing how sheet metal is used in vehicle design. Through simulation software and predictive analytics, manufacturers can optimize layouts and material usage, producing parts that abide by stringent regulatory standards while maximizing safety.
Emphasizing The Importance of Sheet Metal in Car Floors
Sheet metal plays a vital role in the integrity of automotive structures. The composition and treatment processes used directly influence a vehicle's overall safety, performance, and longevity.
Consider the structural implications of adequately designed car flooring — it serves as more than just a base; it is integral to the entire vehicle architecture.
Trends in Automotive Industry
Market Analysis and Forecasts
The automotive sheet metal sector is projecting steady growth driven by increasing vehicle production demand worldwide. Consumer trends are shifting toward sustainable and smart vehicle technologies, further fortifying the necessity for improvements in sheet metal applications.
Electric Vehicle Adoption Rates
Sheet metal usage in electric vehicles involves understanding battery storage designs and heat dissipation needs. These considerations underscore how sheet metal is adapting to modern demands, including lightweight construction processes.
Growth of Ride-Sharing and Mobility Solutions
The growth of ride-sharing services necessitates durable and flexible automotive solutions. Sheet metal’s adaptability allows vehicles to conform to the rigors of shared use while ensuring user safety.
Consumer Preferences Shifts and Impacts
Changes in consumer preferences also affect vehicle design. This trend contributes to how manufacturers approach sheet metal utilization, focusing on both performance and cost-effectiveness.
Educational Resources
Technical Knowledge Base
An understanding of sheet metal factors prominently in automotive education. Students studying automotive engineering should familiarize themselves with its properties, forming a foundation for their future careers.
Insights Into Automotive Engineering
Discourses on automotive engineering practices will focus on metallurgy. Knowing how different sheet metals behave under various conditions is vital.
Certifications and Training Programs
Many training programs emphasize EPA standards in vehicle design alongside sheet metal use, ensuring continual compliance with evolving regulations.
Future Trends in Automotive Education
Trends in education are shifting toward interdisciplinary studies merging mechanical, electrical, and software engineering. This holistic approach prepares students to tackle challenges in innovative automotive solutions pertinent to sheet metal applications.
Through this comprehensive exploration, it is evident that sheet metal is more than a mere component; it is central to the very essence of modern automotive design and manufacturing, reshaping alongside technology and consumer needs.
Understanding Sheet Metal


Understanding sheet metal is critical for those involved in the automotive industry, especially concerning car floors. There are various factors involved, from selection to application. Knowledge of sheet metal helps in achieving optimal structural strength while ensuring overall vehicle efficiency and safety. Selecting the right type of sheet metal can have lasting effects on performance, cost, and weight of vehicle components.
Definition and Properties
Sheet metal refers to thin, flat pieces of metal formed by various processes such as shearing and rolling. The thickness of sheet metal is typically less than 6mm. It displays unique properties like durability, malleability, and electrical conductivity depending on the chosen material. Companies prioritize material properties to suit specific automotive requirements. Sheet metal can be finished in several ways, including coatings for increased resistance to corrosion. Materials such as steel, aluminum, and stainless steel are predominant in car manufacturing.
Types of Sheet Metal
The category of sheet metal primarily consists of three materials: steel, aluminum, and stainless steel. Understanding the characteristics of each is important for automotive applications.
Steel Sheet Metal
Steel sheet metal is renowned for its strength. This aspect makes it a popular choice for automotive frames and bodies. Steel's significant tensile strength can contribute to overall vehicle durability. One of its unique features is the availability of different grades of steel, allowing for variations in strength and weight. However, steel is prone to corrosion unless effectively treated with coatings or galvanizing. Additionally, steel may add more weight compared to alternatives, which can influence vehicle fuel efficiency.
Aluminum Sheet Metal
Aluminum sheet metal is known for its lightweight and high strength-to-weight ratio. This property makes it ideal for anodized surfaces in modern vehicles. It resists corrosion as compared to steel. Hence, aluminum, in turn, can use less material thickness for durability improvement. However, the production cost is typically higher than that of steel. Also, aluminum may not provide as much structural integrity as steel in high-stress applications.
Stainless Steel Sheet Metal
Stainless steel sheet metal combines the best attributes of steel and aluminum. With excellent corrosion resistance and durability, it is suitable for both aesthetic components and structural applications. The unique feature of stainless steel is its ability to maintain appearance over time due to its chromium content, which forms a protective layer. However, one disadvantage is its cost, which is usually higher than carbon steel. Balancing these characteristics is essential for automotive design agreements.
Importance of Sheet Metal in Automotive Applications
Sheet metal serves a critical function in automotive manufacturing. It is not just a material choice; its characteristics can profoundly impact the overall quality and performance of vehicles. The importance of sheet metal can be observed through several specific elements that influence both the functionality and safety of automotive structures. The primary considerations in these applications include structural integrity and weight.
Structural Integrity
Structural integrity is paramount in automotive design. The sheet metal used forms the foundation of various components within a vehicle, including car floors. A properly engineered sheet metal product grants strength and resistance against forces such as impact, corrosion, and wear. High-strength materials can withstand stresses encountered during regular operation, protecting the vehicle’s occupants and ensuring longevity.
By selecting appropriate alloys and thickness, manufacturers can optimize performance features of cars. For example, the addition of various alloys to traditional steel or aluminum can increase strength while making the material more ductile. This balance is essential; if the sheet metal is too rigid, it may crack under stress, whereas if it is too flexible, it may not support the necessary structural demands.
"The choice of sheet metal ultimately shapes the car’s resistance to crashes, which is a core aspect of safety in vehicle operation."
Weight Considerations
Weight reduction is another crucial consideration in the design of automotive applications. The automotive industry constantly seeks to improve fuel efficiency and performance while minimizing the carbon footprint. Lightweight sheet metal materials achieve these objectives without compromising durability or safety.
By integrating aluminum or advanced high-strength steel into areas such as the vehicle floor, engineers can contribute to significant weight savings. Less weight translates into better fuel efficiency due to reduced mechanical work and improved acceleration capabilities.
Some key benefits of prioritizing weight reductions include:
- Enhanced fuel economy: Vehicles consume less energy to transport a lighter load.
- Increased performance: Lower weight accelerates car response times and enhances handling.
- Lower emissions: This reflects positively on environmental standards and regulations.
The continuous innovations in materials science focus on developing lighter materials that stand up to rigorous automotive demands. Consequently, understanding the implications of sheet metal usage in structural integrity and weight is crucial for automotive professionals as they design and engineer modern vehicles.
Applications of Sheet Metal in Car Flooring
Sheet metal is more than just a basic material; it serves vital roles in the construction of car flooring. Understanding its applications is essential for automotive enthusiasts, students, and professionals. This section highlights various critical elements related to application of sheet metal in car floors, emphasizing their benefits and considerations.
Floor Pans and Reinforcements
Floor pans are Structurally significant in vehicles, contributing to the overall rigidity and stability. Sheet metal is the primary material used in the manufacturing of these pans, typically made from steel or aluminum for their high strength-to-weight ratios.
The shape and fit of floor pans are crucial during fabrication. Engineers must consider the vehicle model, ensuring the pans offer protection against road inattention like debris. Furthermore, the material thickness impacts durability and noise dampening capabilities.
Reinforcements are integrated within or in connection to the floor pans. Their role is to absorb energy during collisions, enhancing passenger safety. Depending on the design, this can include cross members or support brackets made of high-strength steel sheet metal.
Manufacturing Processes of Sheet Metal Parts
The manufacturing processes of sheet metal parts are critical in determining the final quality and performance of automotive components. The precision and versatility of these processes stand at the forefront of automotive design and functionality. Understanding the various techniques is essential for automotive engineers and designers, as the choice of method can affect factors such as cost, efficiency, and the structural integrity of the parts used in car flooring.
Cutting Techniques
Laser Cutting
Laser cutting is a highly advanced method used extensively in the production of sheet metal components. It employs a focused laser beam to cut through various types of metals with high precision. One of the main benefits of laser cutting is its ability to create intricate designs and tight tolerances while minimizing waste material. Another notable characteristic is the high speed at which the laser can operate, optimizing production timelines.
A unique feature of laser cutting is its versatility. This technology can cut through materials ranging from lightweight alloys to thicker steel sheets. The accuracy of laser cutting reduces the requirements for secondary operations, making it a popular choice in the automotive sector when producing floor pans and reinforcements.

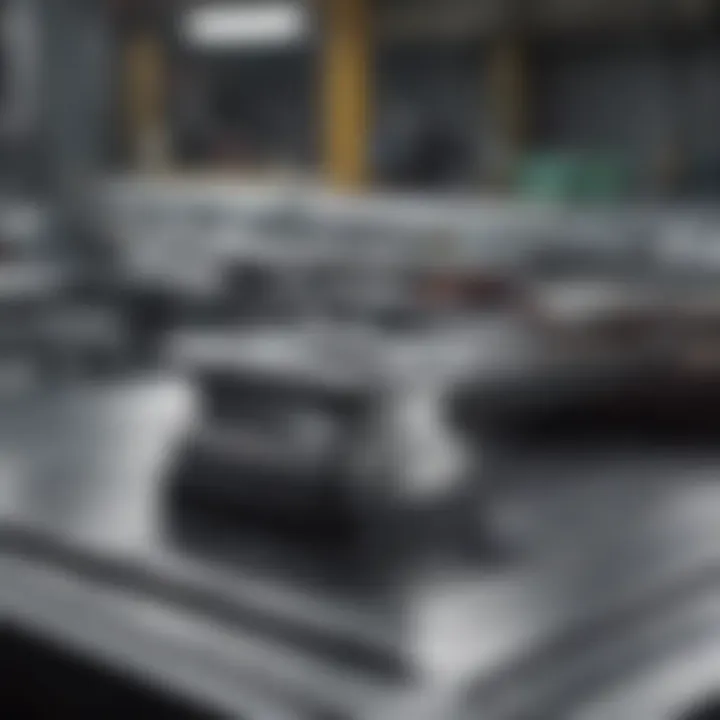
- Advantages of Laser Cutting:
- Disadvantages of Laser Cutting:
- High precision and intricate designs
- Minimal thermal distortion
- Faster production times
- Higher operational costs for small-scale projects
- Requires specialized equipment
Water Jet Cutting
Water jet cutting utilizes a high-pressure jet of water, often mixed with abrasive material, to cut through sheet metal. This method is notable for its ability to cut complex shapes without inducing heat into the material, eliminating the risk of deformation. Water jet cutting is commonly used when working with materials sensitive to high temperatures, making it suitable for various types of metals used in car floors.
The key characteristic that sets water jet cutting apart is its environmentally friendly approach due to the lack of fumes, as compared to traditional cutting methods. This process is also able to work with a wider range of materials without the limitations posed by conventional cutting technologies.
- Advantages of Water Jet Cutting:
- Disadvantages of Water Jet Cutting:
- No heat distortion
- Can cut various materials including softer options like rubber and plastics
- Eco-friendly cutting process
- Slower cutting speeds compared to laser
- Can be more expensive due to operating costs
Forming Processes
Bending
Bending is a vital forming process in which the sheet metal is deformed around a straight axis. This technique provides strength to parts while ensuring they fit part of the automotive design, especially in flooring applications. Bending is advantageous as it ready allows for the straightening of metal sheets to form the desired shapes necessary for proper installation in vehicle structures.
One key feature of bending is that it offers a significant degree of control over the final dimensions of the product. It also has the benefit of requiring less material than other manufacturing processes, thus reducing costs and waste.
- Advantages of Bending:
- Disadvantages of Bending:
- Efficient use of material
- Versatility in design
- Possible area weaknesses where bends are made
- Requires careful planning to avoid incorrect bends
Stamping
Stamping refers to the process of using a die to shape sheet metal through either cutting or forming. This process produces high volumes of identical parts, making it highly useful in mass production for car floors. One of the major advantages is the ability to create consistent and precise features that improve the surface area of parts.
Stamping plays an important role Sk in enhancing product reliability, as it minimizes the need for secondary processes. Its effectiveness in mass production scenarios contributes to lower per-unit costs when dealing with the same design, thus making it favorable for automotive manufacturers.
- Advantages of Stamping:
- Disadvantages of Stamping:
- High production rate
- Low per-part costs in mass production
- Initial tool and die costs can be significant
- Less flexibility for design changes after the die is made
Understanding the manufacturing processes of sheet metal is vital for enhancing car safety, reducing manufacturing costs, and improving precision in vehicle design. Thus, mastering these techniques is crucial for industry professionals.
Through these methods—cutting and forming—a wide variety of robust, efficient, and aesthetically pleasing parts can be created to serve within the complex environment of modern automotive flooring systems.
Advancements in Sheet Metal Technology
Advancements in Sheet Metal Technology play a pivotal role in enhancing the utility and performance of sheet metal in automotive applications. As automakers strive for greater efficiency and safety, the materials used for car floors have become crucial. The development of new alloys and coatings, alongside the integration of smart technologies, underscores a shift toward innovation in this field.
Innovative Alloys and Coatings
The emergence of innovative alloys and coatings significantly influences the durability and performance of sheet metal in vehicles. Traditional materials exhibited limitations in strength-to-weight ratios and resistance to environmental factors. However, advances in metallurgy have led to the creation of specialized alloys that are lighter yet incredibly sturdy.
These alloys include high-strength low-alloy (HSLA) steel, which offers better tensile strength without the added weight. Such innovations have direct implications for vehicle performance, affecting acceleration, fuel efficiency, and handling. Additionally, innovative coatings enhance resistance to corrosion, which is particularly vital for components in contact with moisture and road debris.
Innovative coatings not only protect sheet metal from rust but also reduce maintenance costs over the lifecycle of a vehicle.
The importance of coatings cannot be overstated. Thermal and chemical resistance properties, especially for electric vehicles, are critical to protecting delicate electronic components. Each alloy and coating used contributes uniquely to preparing car floors for various operational environments. This attention to materials ensures longevity in performance and safety.
Integration with Smart Technologies
The integration of smart technologies within sheet metal applications represents a progressive step for the automotive industry. Smart technologies often harness sensors and data systems that enhance vehicle performance and improve user experience.
For instance, manufacturers now develop sheet metal that can sense changes in environmental conditions, helping modify temperature regulation or weight load. This capability potentially helps with personal comfort or overall vehicular efficiency.
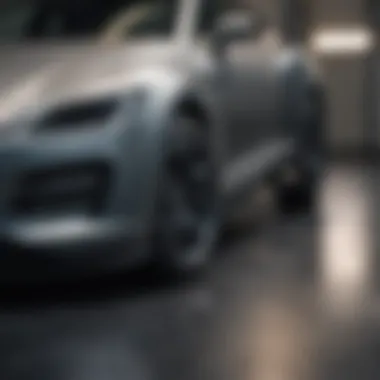
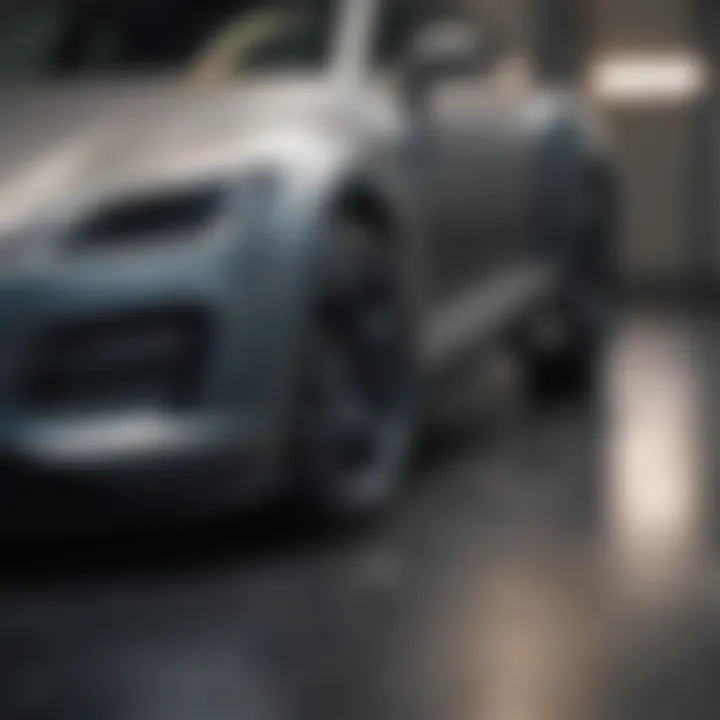
Moreover, advancements allow for better communication between body components and safety systems. As we move toward a future increasingly dominated by connected and automated vehicle dynamics, such integrations will overall impact the design decisions around sheet metal in diverse ways.
In summary, the explorations into ~experimental materials~ and tech integration highlight a clear trend towards adaptability and efficiency in car flooring. As our understanding of suitable materials evolves, so does their role in enhancing vehicle safety and driving experience alike.
Environmental Impact of Sheet Metal Production
The environmental impact of sheet metal production is a critical component in today's automotive manufacturing processes. This aspect is not merely a regulatory compliance issue but also a moral obligation for industry stakeholders. Understanding how the production of this material affects the environment is essential for automotive enthusiasts, car buyers, and industry professionals alike. The industry's shift toward sustainable practices often hinges on these considerations, leading to improvements in both the environment and product efficiency.
Sustainability Considerations
Sustainability in sheet metal production involves various factors ranging from resource extraction to manufacturing practices. Sustainable approaches typically focus on minimizing energy consumption during production and reducing waste generated in the manufacturing process.
- Use of Renewable Energy: Many manufacturers are moving toward renewable energy sources such as solar or wind to power their operations. This approach significantly reduces carbon emissions associated with metal production.
- Water Management: Effective water management practices can reduce the amount of clean water needed for production, essential in metal refining processes where large quantities are typically used. Efforts are increasingly being made to recycle water within plants, treating and reusing it for production needs.
- Chemical Use: Minimizing harmful chemicals used in processes such as coating is another aspect of sustainability. Companies are adopting more eco-friendly materials, reducing toxic substances released into air and water.
These sustainability measures are becoming a marketing point for companies, appealing to the growing sector of environmentally conscious consumers.
Recycling Potential
Recycling offers substantial benefits, both environmentally and economically, when it comes to sheet metal production. The metal recycling industry has developed complex networks to facilitate the reuse of input materials in new products.
- Significant Resource Recovery: Nearly 80 million tons of scrap metal are recycled in the United States alone each year, playing a HUGE role in preventing unused material from ending up in landfills.
- Energy Efficiency: Using recycled metals consumes less energy compared to producing new metal from ore. For instance, recycling aluminum can save up to 90% of energy required for the primary production.
- Closed-loop Recycling: Manufacturers are working towards a closed-loop system whereby scrap materials from one product serve as resources for another, thereby prolonging product life cycles and reducing resource extraction demands.
The recycling and reuse of materials is increasingly recognized as essential in reducing the ecological footprints of manufacturing processes while improving economic efficiency.
These links show more about sustainability and recycling practices:
Safety Regulations and Standards
Safety regulations in automotive manufacturing are crucial. They ensure the protection of passengers and other road users. These standards dictate the acceptable use of materials and processes in the construction of vehicles. This section emphasizes the relevance of adherence to such regulations in the context of sheet metal for car flooring, focusing on two key areas: compliance with material standards and testing methods.
Compliance with Material Standards
Compliance with material standards is fundamental in the automotive industry. Various organizations set these standards to ensure safety, performance, and durability. The use of specific types of sheet metal is often determined by these regulations. For example, thin-gage steel is commonly favored for its strength and resilience. Participants in the industry must acertain that the materials used meet specifications from entities such as the American Society for Testing and Materials (ASTM) or the International Organization for Standardization (ISO).
Some vital points include:
- Material Properties: Material certifications verifying composition and integrity are essential. They ensure that the metal can withstand environmental factors.
- Safety Ratings: The materials must contribute positively to the overall safety rating of the vehicle. This is NOT just about compliance; it affects customer trust.
- Post-Manufacturing Requirements: Regulations demand that businesses do not only meet initial standards but must also ensure continued compliance throughout the lifecycle of the vehicle.
A strong compliance framework helps manufacturers protect liabilties while building vehicles that stand the test of rigorous usage.
Testing Methods and Requirements
Testing methods assess the reliability and safety features of vehicle materials, especially sheet metal used in car floors. Various test types reveal different interaction facets of materials under pressure and their resilience against potential failures. Visibility of critical testing processes includes:
- Tensile Testing: Measures how much force a sample can endure before failing
- Fatigue Testing: Examines how well materials endure repeated flexing over time, a crucial feature for vehicle reliability
- Corrosion Tests: These evaluate how the metal responds to environmental exposure
Testing requirements establish benchmarks for performance. They reinforce material integrity and evaluate whether the sheet metal will effectively protect passengers during unfortunate events, such as crashes.
Understanding the intricate compliance requirements dictates the foundation of dependable automotive engineering, serving both creator and consumer.
Future Trends in Sheet Metal Usage
The use of sheet metal in car flooring is undergoing significant changes due to advancements in technology and evolving automotive designs. It is critical to recognize future trends in this area, as they directly affect vehicle safety, performance, and sustainability.
Emerging Materials and Techniques
In the quest for lighter, stronger, and more cost-effective solutions, automotive manufacturers are beginning to explore new materials and techniques in the production of sheet metal components. Options like high-strength steels and aluminum alloys offer advancements in durability without significantly increasing weight. These materials provide better fatigue resistance, crucial for vehicles subjected to varying loads and stresses.
Furthermore, innovative manufacturing techniques such as additive manufacturing—commonly known as 3D printing—are becoming integral. This change enables manufacturers to create complex designs that were not feasible with traditional methods. Technology like this enhances production speed and reduces waste, making it a preferred choice in modern automotive manufacturing.
- Key Benefits of Emerging Materials and Techniques:
- Improved strength-to-weight ratio
- Cost savings in production
- Potential for reduced environmental impact
Impact of Electric and Autonomous Vehicles
The rise of electric and autonomous vehicles is reshaping the requirements for sheet metal components utilized in car floors. Electric vehicles (EVs) demand designs that accentuate efficiency and lightweight structures. Streamlined chassis made from sheet metal not only ensures better energy efficiency but also increases driving range, a primary concern for electric vehicles.
With autonomous vehicles introducing new safety and performance standards, the role of sheet metal evolves even further. The material must not only fulfill traditional requirements but also support advanced technologies, such as sensors and cameras, vital for safe autonomous operation.
The adaptation of sheet metal in electric and autonomous vehicles promotes not only efficiency but also safety.
Finally, research into integrating materials that are conducive to battery packs is on the rise. Manufacturers aim to develop components that enhance electric power capabilities while ensuring proper heat dissipation and structural integrity, demanding a very specialized understanding of material science in sheet metal applications.