Understanding 110v Aluminum Welders: Features & Benefits
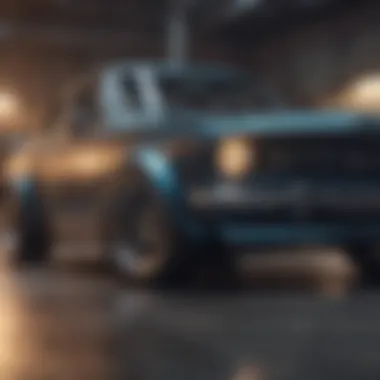
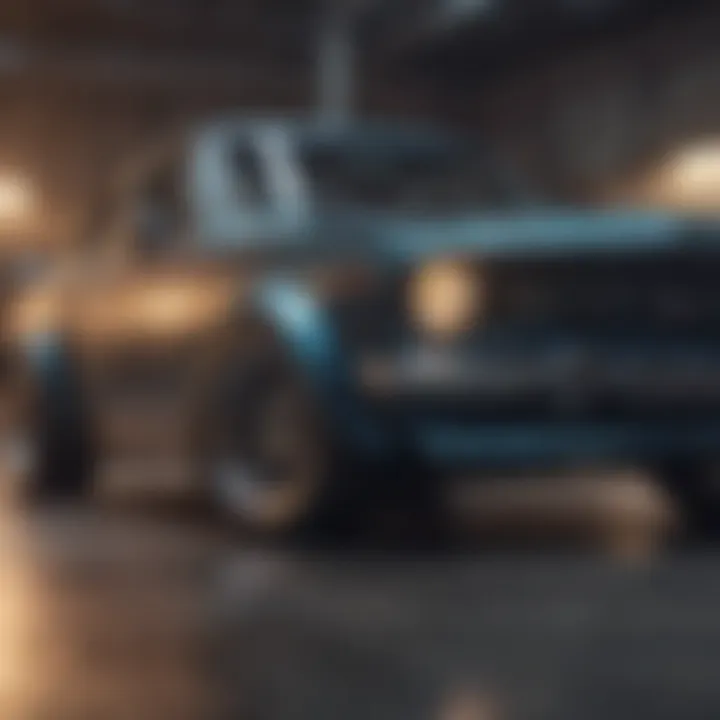
Intro
The usage of a 110v aluminum welder is becoming increasingly prevalent in various sectors. These tools are specifically designed to handle the unique challenges presented by aluminum materials, which require distinct techniques to ensure effective welding. Understanding how these welders work and their advantages makes it easier for both professionals and hobbyists to select the right equipment for their needs.
This article explores the operational attributes of the 110v aluminum welder, along with its applications and benefits. It targets automotive enthusiasts, technicians, and anyone keen on mastering aluminum welding. As you read on, you will find insights into the features that distinguish these welders, how they perform in different contexts, and tips for proper maintenance and safety.
Automotive Features and Innovations
Overview of Latest Technologies
The automotive industry has witnessed rapid advancements, including the rise of welding technologies designed specifically for aluminum. These innovations play a critical role in enhancing the manufacturing of lightweight vehicles, especially in the context of electric and hybrid models.
A 110v aluminum welder typically features advanced electronic control systems, including features like pulse welding and adjustable settings for voltage and wire feed speed. These features allow welders to achieve cleaner and stronger welds, essential for maintaining structural integrity.
In-Depth Look at Electric/Hybrid Vehicles
Electric and Hybrid vehicles utilize lightweight materials to improve efficiency. Aluminum is favored for its strength-to-weight ratio. Hence, effective aluminum welding is key in the assembly of these vehicles. Using a 110v welder can make the process more accessible to smaller workshops and individual enthusiasts, making it easier to engage in electric vehicle projects.
Analysis of Autonomous Driving Systems
While autonomous driving systems focus more on electronics and software integration, the physical components still require meticulous assembly. Using a 110v aluminum welder can facilitate repairs and modifications to the chassis or frame, crucial in maintaining the overall safety and functionality of autonomous vehicles.
Evaluation of AI in Automotive Solutions
Artificial Intelligence is transforming various automotive processes, including manufacturing and repair. One area where AI can impact aluminum welding is in monitoring and controlling the welding variables. Employing AI-driven systems ensures optimal weld quality and reduces the margin of error, thus increasing efficiency.
Applications of 110v Aluminum Welders
Automotive Repairs and Modifications
One of the primary applications of 110v aluminum welders is in automotive repairs. Whether fixing a damaged frame or making modifications for performance upgrades, these welders provide flexibility and ease of use. Mechanics can easily transport them, making on-site repairs more feasible.
DIY Projects and Hobbyist Use
For enthusiasts, owning a 110v aluminum welder opens new avenues for creative projects. Many hobbyists engage in building custom bike frames or automotive parts. The accessibility of these welders makes them an appealing choice for anyone interested in welding aluminum at home.
Industrial Applications
In industrial settings, 110v aluminum welders can be used for lighter fabrication work. Smaller workshops, which may not have the infrastructure for high-voltage welders, can utilize these to complete various tasks effectively.
The accessibility and versatility of 110v aluminum welders make them essential tools across many sectors.
Maintenance Tips and Best Practices
Regular Maintenance Schedules
To prolong the lifespan of a 110v aluminum welder, it is vital to establish a maintenance schedule. Regular inspections of the electrical components and cleaning of the welding nozzles will keep the device functioning optimally.
DIY Repair Guides
Understanding basic repairs can save time and reduce costs. Many resources are available online, offering step-by-step guides to fix common issues encountered with these welders.
Seasonal Car Care Strategies
Welders should be stored properly between uses. Maintaining a dry environment prevents corrosion which can affect performance during the welding season.
Addressing Common Issues and Solutions
Some common problems include inconsistent weld penetration and feeding issues. Investigating the wire feed speed setting and checking for blockages can often resolve these concerns.
The End
Understanding the operational mechanics of 110v aluminum welders enhances both capability and creativity in welding projects. By employing the right techniques and maintaining the equipment properly, users will deliver quality results, whether in professional settings or personal endeavors.
Prolusion
Welding technology plays a crucial role in various industrial and DIY applications. One important area of this field is aluminum welding, which has gained traction due to the material's unique properties and advantages. In this article, we will explore the 110v aluminum welder, a device notable for its portability and efficiency. Understanding its features, applications, and benefits helps automotive enthusiasts, car owners, and students navigate effectively through the world of welding.
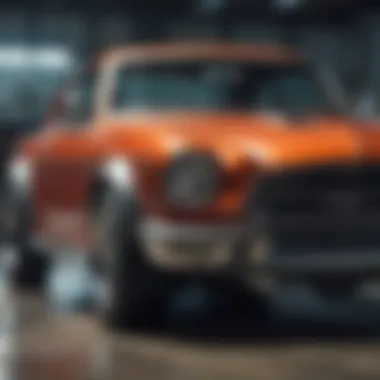
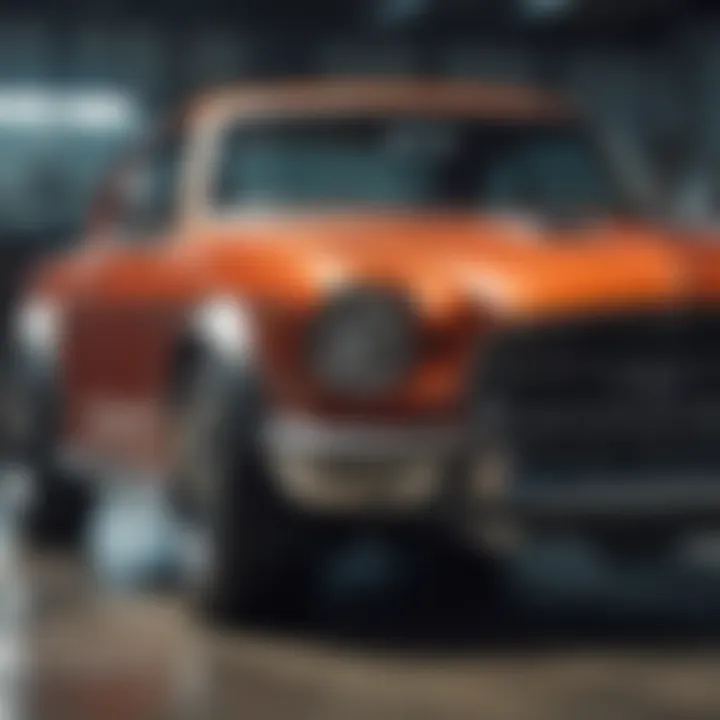
The significance of discussing 110v aluminum welders lies in their growing popularity. With the rise of lightweight materials in automotive design and manufacturing, the need for proficient welding techniques specifically for aluminum has become clear. These welders are particularly useful in home workshops and smaller industrial settings, where conventional 220v welders might be excessive or impractical.
By delving into the salient aspects of 110v aluminum welders, we highlight key features such as portability, ease of use, and versatility. Such insights encourage informed decisions, whether for professional applications or DIY projects. This article aims to present detailed information, enabling readers to understand the practical implications of choosing the right welder for specific tasks.
Overview of Welding Technology
Welding is a method that joins materials, usually metals, through heat. The process requires an understanding of various types of welding techniques, including MIG (Metal Inert Gas), TIG (Tungsten Inert Gas), and stick welding. Each method demonstrates distinct characteristics and suitability for different applications.
In recent years, welding technology has evolved significantly, introducing advancements that enhance efficiency and results. For instance, the development of inverter technology has improved performance and made welding machines lighter and easier to handle. Users must be aware of these developments to leverage the best welding practices in their projects.
Importance of Aluminum in Modern Applications
Aluminum is becoming a favored material due to its unique properties, such as light weight, corrosion resistance, and a high strength-to-weight ratio. These attributes make aluminum particularly suitable for various industries, most notably in automotive and aerospace sectors. As manufacturers seek greater fuel efficiency and overall performance, aluminum continues to be an essential choice.
The versatile nature of aluminum enables its use in both structural and aesthetic applications. In automotive manufacturing, it is commonly used for body panels, frames, and engine components. As automotive technology advances, the demand for effective aluminum welding will likely increase, particularly with more emphasis on electric vehicles and lightweight materials. Understanding how 110v aluminum welders function within these contexts is fundamental for anyone looking to work with aluminum in their projects.
What is a 110v Aluminum Welder?
A 110v aluminum welder is a specific tool designed for welding aluminum materials using a low voltage of 110 volts. This type of welder is significant due to its widespread applications, particularly in industries and tasks that involve lightweight materials. This article section will dissect the essential aspects of the 110v aluminum welder by examining its definition, specifications, and technical underpinnings, allowing readers to appreciate the advantages it brings to various welding contexts.
Definition and Specifications
The 110v aluminum welder functions primarily by supplying a nominal voltage of 110 volts to generate the heat necessary for creating a weld. The lower voltage allows for easier accessibility in homes and smaller workshops where high voltage might not be feasible. Typically, these welders are equipped with functions such as MIG (Metal Inert Gas) welding compatibility, enabling effective and efficient bonding of aluminum materials.
Key specifications can include:
- Power output: While generally lower, many 110v welders can produce adequate amperage for light to moderate welding tasks.
- Weight: Many are lightweight, often ranging between 35 to 70 pounds, making them portable and easy to handle.
- Duty cycle: This is an important metric indicating the time the welder can operate continuously before needing a break. A higher duty cycle means more work can be done without interruption.
Technical Aspects of 110v Welding Technology
Understanding the technology behind a 110v aluminum welder is crucial in realizing how it operates. These welders often utilize a variety of techniques such as:
- TIG Welding: This provides greater precision and control during the welding process. It is commonly used for thin materials, ideal for aluminum.
- MIG Welding: This technique is more popular for aluminum as it allows for faster welding speeds and produces strong joints.
Each method has its strengths, which can be chosen based on specific project requirements. The cooling technology, often built into the welder, also plays a crucial role. It helps maintain optimal temperatures to prevent overheating, ensuring efficiency.
"The choice of welding technique can significantly affect the outcome of an aluminum project, making the understanding of these aspects essential for any operator."
Finally, safety features are integral to the design. Many 110v aluminum welders incorporate built-in thermal overload protection, which automatically shuts off the machine when it overheats. This feature is vital to prolonging the welder's life and ensuring safety during use.
Key Features of 110v Aluminum Welders
Understanding the key features of 110v aluminum welders is crucial for realizing their full potential in various applications. Each feature serves a specific purpose that enhances operational efficiency and user experience. Factors like portability, power requirements and efficiency, and user-friendly controls set these welders apart in the market. This section will delve into these elements, providing insights beneficial for automotive enthusiasts, beginners, and seasoned professionals alike.
Portability and Convenience
One of the standout features of a 110v aluminum welder is its portability. Because these welders are often compact and lightweight, they can be easily transported, making them an ideal choice for both home users and professionals who work on-site. Having the ability to move the welder from one location to another without much hassle is a significant advantage. It allows for flexibility in project locations, whether one is fixing a vehicle or designing custom aluminum parts.
Convenience also comes from the welder's ability to operate on standard household outlets. This means no need to invest in expensive welding setups or modify electrical systems. It enables users to plug in and start welding almost anywhere, provided that a suitable work surface is available. The ease of access to power sources greatly simplifies the welding process, making it more appealing to DIY enthusiasts.
Power Requirements and Efficiency
110v aluminum welders are designed to operate efficiently with 110-volt power outlets. While some may worry about power limitations, these welders have been engineered to maximize output within these parameters. Users often find them effective for light to medium welding tasks, which is sufficent for many automotive applications.
Energy efficiency is another critical aspect. Many models are equipped with inverter technology. This technology enhances the performance while using less power compared to traditional welders. Consequently, it leads to lesser electricity bills, which can be a considerable advantage over time. However, it is essential to understand the duty cycle of the welder being considered. A welder with a high duty cycle can work longer without overheating, making it more suitable for larger jobs.
User-Friendly Controls
Simplicity in operation is a hallmark of 110v aluminum welders. Many models feature intuitive controls and dials that allow for easy adjustment of welding parameters. This is particularly beneficial for beginners who may feel overwhelmed by more complex machines.
User-friendly controls may include presets for various welding settings. These presets help to ensure that the welder operates optimally for specific tasks or materials. Some advanced units even come with digital displays, allowing users to keep track of their settings and make adjustments on the fly.
In summary, the key features of 110v aluminum welders enhance their effectiveness and usability. Portability makes them accessible for various projects, while efficient power use reduces operational costs. Meanwhile, user-friendly controls simplify the experience, catering to both novice and experienced welders.
Applications of 110v Aluminum Welders
The applications of 110v aluminum welders are diverse and significant in various fields. These welders provide unique advantages, making them essential in both professional and home settings. Understanding their applications helps users appreciate their versatility and efficiency.

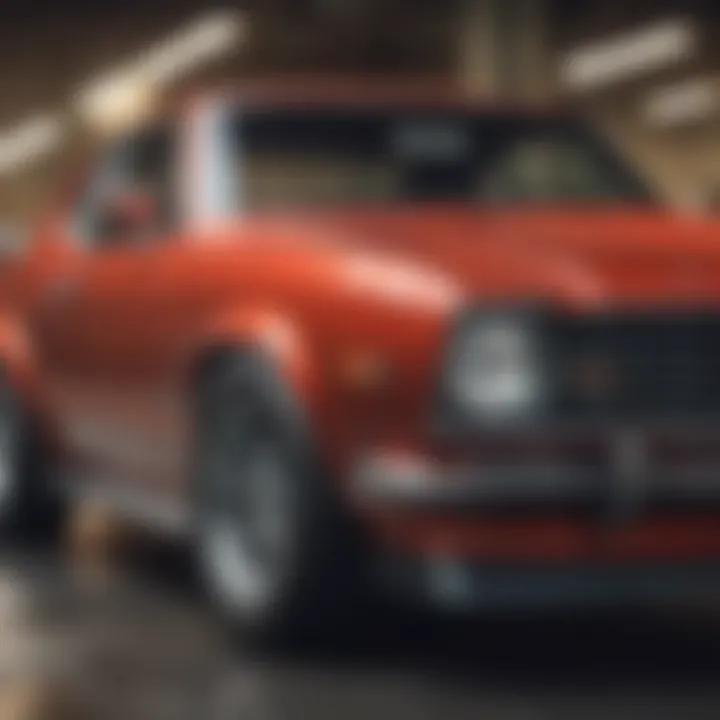
Automotive Industry Usage
In the automotive industry, 110v aluminum welders play a crucial role. Vehicles often use aluminum for parts due to its lightweight and strength. These features enhance fuel efficiency and performance. 110v welders are especially beneficial in automotive repairs, such as fixing aluminum frames or panels. They allow for precise welds, essential in maintaining structural integrity. Moreover, being portable, these devices can be used in shops or directly at job sites.
Home and DIY Projects
For home projects, 110v aluminum welders are ideal for hobbyists and DIY enthusiasts. Many household items are made of aluminum, like furniture, outdoor decorations, or even custom light fixtures. With a 110v welder, creating or repairing these items becomes manageable. The user-friendly controls make it accessible for individuals with limited welding experience. This convenience encourages creativity, as anyone can explore aluminum fabrication without investing in heavy equipment.
Commercial Welding Applications
In commercial settings, the use of 110v aluminum welders extends to manufacturing and production lines. Many businesses, such as sign making and crafting, benefit from these tools. They are suitable for small-scale production where precision is vital. The cost-effectiveness of these welders also attracts small enterprises looking to minimize overhead while maximizing output. The flexibility and portability allow companies to perform repairs and new installations on-site efficiently.
"The versatility of 110v aluminum welders makes them a preferred choice in both automotive and commercial sectors, bridging the gap between professional-grade and accessible tools for all."
In summary, the applications of 110v aluminum welders are instrumental in various domains. Their advantages significantly contribute to both efficiency and effectiveness in welding tasks, making them valuable assets in modern fabrication and repair environments.
Advantages of Using 110v Aluminum Welders
The decision to utilize a 110v aluminum welder often stems from a variety of factors. Understanding the advantages of these machines can guide consumers and professionals alike in making informed choices. This section will examine the cost-effectiveness, user-friendliness for novices, and the versatility of welding techniques that these welders offer.
Cost-Effectiveness
110v aluminum welders present a compelling choice for those looking to balance performance and budget. These devices are generally more affordable than their higher voltage counterparts. Their lower upfront cost can make them an attractive option for hobbyists and small business owners.
In many cases, operating expenses are also lower. The reduced power needs of a 110v welder mean lower electricity bills over time. This aspect is crucial, especially for projects requiring extensive hours of use.
Furthermore, the availability of these welders often leads to a more competitive market. As a result, consumers can find various models that meet their specific needs without overspending. Ultimately, the cost-effectiveness of using a 110v aluminum welder can enhance the overall welding experience while staying within financial constraints.
Ease of Operation for Beginners
Beginners often seek equipment that combines effectiveness with simplicity. The 110v aluminum welder excels in this area. Many models are designed with user-friendly interfaces. This feature makes them accessible to those new to welding.
The lightweight nature of these machines adds to their appeal. Since they are portable, beginners can easily move them around, whether in a workshop or at home. Additionally, many have straightforward controls, allowing even those with limited experience to achieve satisfactory results.
Adopting a 110v aluminum welder can significantly reduce the learning curve for novices. As users gain confidence, they can enhance their skills without feeling overwhelmed by complex equipment.
Versatility in Welding Techniques
One of the standout advantages of 110v aluminum welders is their versatility. These machines can handle various welding techniques, including MIG (Metal Inert Gas) and TIG (Tungsten Inert Gas) welding. Each method brings unique benefits that can accommodate different project needs.
- MIG Welding: This technique is quite common for aluminum due to its speed and efficiency. It allows smooth, clean welds, making it suitable for automotive applications and repairs.
- TIG Welding: While typically more complex, TIG welding provides greater control and precision, leading to high-quality welds. This method is often favored for intricate projects where appearance matters.
For users engaged in diverse tasks, the versatility of a 110v welder can be a game changer. Whether working on small repairs or larger projects, these machines adapt to various techniques and settings. Such flexibility is especially beneficial in automotive settings, where different approaches may be necessary to achieve optimal results.
"Choosing a 110v aluminum welder can simplify your welding tasks while offering cost savings and immense versatility."
Choosing the Right 110v Aluminum Welder
Selecting the appropriate 110v aluminum welder is critical for achieving optimal results in your welding projects. This choice affects not only the quality of your work but also your efficiency and overall satisfaction. Understanding the various features and capabilities of different models is essential to make an informed decision. Factors such as the type of materials to be welded, the scale of projects, and specific personal or professional requirements all come into play when determining which welder fits your needs.
By evaluating these aspects thoroughly, you ensure that you select a welder that enhances your productivity while matching your skill level. Improper choices can lead to frustration and poor outcomes. Therefore, knowing what to look for when buying a welder will pay off in the long run.
Assessing Project Requirements
Before acquiring a 110v aluminum welder, it is vital to assess your project requirements carefully. Different tasks require different specifications. For instance, if you are primarily working on thin aluminum sheets, you may need a machine with precise control over the heat output. Conversely, for thicker materials, capabilities such as increased amperage and additional welding modes might be necessary.
In addition, consider the types of aluminum alloys you will be welding. Not all welders can manage every type of alloy effectively. Understanding the primary use case will guide you in choosing a welder that will perform well under those specific conditions.
Some essential factors to consider include:
- Material Thickness: Determine the thickness range of aluminum you will frequently encounter.
- Type of Welding: Know the process you will be using, whether it's MIG or TIG welding.
- Frequency of Use: If you plan to use it frequently, investing in a more durable model may be wise.
Comparative Analysis with Other Welders
When deciding on a 110v aluminum welder, a comparative analysis with other types of welders is beneficial. This helps to highlight the unique features that make 110v welders suitable for specific applications. Other options may include 220v welders or specialized machines designed for particular tasks.
110v welders have distinct advantages, especially regarding portability and ease of use. They can be plugged into standard outlets, making them more accessible for home use. However, compared to larger models, they may have limits in terms of power and performance.


When making comparisons, consider:
- Power Output: How does the 110v model's amp range compare to other welders?
- Portability: Is the welder easy to transport or store?
- Versatility: Can the welder handle various welding techniques, or is it limited in scope?
Maintenance of 110v Aluminum Welders
Maintaining a 110v aluminum welder is crucial for both optimal performance and longevity. Regular maintenance ensures that the welder functions efficiently, prevents potential breakdowns, and enhances the quality of welding results. In the automotive industry and related areas, where precision is key, a well-maintained welder can make a significant difference. Here, we will discuss the specifics of maintenance, focusing on regular inspections, cleaning, and how to effectively replace worn parts.
Regular Inspection and Cleaning
Regular inspections are vital for identifying any emerging issues before they become significant problems. Inspecting key components such as the power cord, electrodes, and cooling systems can prevent minor irritations from escalating into major repairs. Look for any fraying in wires or unusual wear on parts.
Cleaning is equally important. During use, welders can accumulate slag, dust, and other debris, which may affect their performance. Routine cleaning should entail:
- Unplugging the welder before any inspection or cleaning.
- Using a soft brush or vacuum to remove debris from vents and fans.
- Cleaning the torch and nozzle to prevent clogs.
A clean welder not only operates better but also presents a safer working environment, reducing fire risks and other mishaps.
Replacing Worn Parts
Every welder will encounter wear and tear over time, especially if used frequently. Recognizing when to replace specific parts is essential for maintaining efficiency and safety.
Common parts that may need replacement include:
- Electrodes: As they wear down, the welding quality suffers.
- Welding wire: Old or contaminated wire can produce weak welds.
- Cooling fans: If the fan isnβt working properly, overheating can occur.
Replacing worn parts requires careful attention to detail. Always ensure that replacements are compatible with your specific welder model. Itβs advisable to consult the user manual or seek guidance from manufacturers like Lincoln Electric or Hobart for recommendations on parts. Regularly replacing worn components will ultimately enhance the performance of your welder, ensuring that it operates at peak efficiency.
"Preventative maintenance is the best way to extend the life of your welder and ensure it performs at its best."
Safety Considerations
Safety is of utmost importance when using a 110v aluminum welder. This article aims to inform readers of the critical precautions that must be taken to ensure not only successful welding results but also personal safety during this process. Working with electrical equipment, especially in metal fabrication, poses inherent risks. Understanding these risks and addressing them is essential for both novice and experienced welders.
Personal Protective Equipment (PPE)
Personal Protective Equipment (PPE) is crucial for anyone involved in welding. Proper PPE protects against various hazards, including electric shock, burns, and exposure to harmful gases. Key components of PPE for welding include:
- Welding helmet: This protects the face and eyes from intense light and sparks. Most helmets come with darkened visors that shield against UV radiation.
- Gloves: Heavy-duty welding gloves provide protection from heat and sharp materials. Gloves must allow for good dexterity while safeguarding the hands.
- Long-sleeve clothing: It is advisable to wear flame-resistant clothing that covers the body. This reduces exposure to flying sparks and hot metal.
- Respirators: In certain settings, respirators might be needed to filter out harmful fumes produced during the welding process.
Investing in quality PPE is critical. Regular inspection of this equipment for damage or wear ensures maximum protection.
Safe Operating Procedures
Establishing and following safe operating procedures forms the backbone of a secure welding experience. Key practices include:
- Workspace preparation: Ensure the working area is clean, well-ventilated, and free from flammable materials. This minimizes the risk of fire hazards.
- Equipment checks: Before starting, inspect the welder for any faults. Look for exposed wires, leaks, or any signs of damage that could affect operation.
- Electrical safety: Always ensure that the welder is connected to a suitable power supply to prevent electrical mishaps. Avoid using extension cords unless absolutely necessary, and if used, ensure they are rated for the power requirements.
- Proper posture and positioning: When welding, maintain a comfortable position to avoid fatigue. Ensure that the welding arc and sparks are pointed away from others.
"Safety should never be an afterthought; it must always be part of the welding process."
By adhering to these guidelines, operators can significantly reduce the risk of accidents, leading to a safer work environment overall. Understanding and implementing these safety considerations ensures that users can focus on the task at hand with minimal anxiety about potential hazards.
End
The conclusion section is essential to reinforce the knowledge gained from this article about 110v aluminum welders. This part ensures that readers consolidate their understanding of the features, applications, and benefits of these machines. A clear and concise conclusion can emphasize significant takeaways, which is critical for making informed decisions regarding welding projects.
By summarizing the key insights discussed throughout the article, individuals can reflect on how 110v aluminum welders stand out in the market. Those contemplating purchases will find value in understanding the practical applications of these welders. Automotive enthusiasts and professionals will also appreciate the emphasis on safety measures and maintenance practices highlighted earlier.
The relevance of this conclusion lies in its ability to inform readers about the future of aluminum welding. As technology evolves, the trends in this field continue to reshape industry standards. Therefore, understanding these trends as concluded will assist readers not just in todayβs tasks but also in future endeavors with aluminum welding.
Summary of Key Insights
This article has provided valuable insights into 110v aluminum welders. The main points that have been presented include:
- Definition and Specifications: 110v aluminum welders are compact and versatile, ideal for small-scale welding projects.
- Applications: These welders are commonly used in automotive repair, home projects, and light commercial use.
- User Benefits: The blend of portability, cost-effectiveness, and ease of operation make them suitable for both beginners and seasoned welders.
- Maintenance and Safety: Regular upkeep and the use of personal protective equipment are crucial for safe operation.
This blend of features positions these machines as a worthy choice for a variety of welding tasks, catering to different skill levels and project demands.
Future Trends in Aluminum Welding
Looking ahead, several trends are likely to shape the aluminum welding landscape:
- Advancements in Technology: Continuous improvements in welding technology could lead to more efficient and user-friendly machines, increasing overall productivity.
- Eco-Friendly Practices: The industry may see a shift towards sustainable practices and materials, further enhancing the appeal of aluminum due to its recyclability.
- Integration with Digital Tools: As digitalization spreads, smart welding processes might emerge, allowing for better control and precision in aluminum welding tasks.
By keeping these trends in mind, individuals can strategically position themselves to leverage new technologies and methodologies in their aluminum welding projects.