Understanding Sheet Metal Shrinking Discs in Automotive
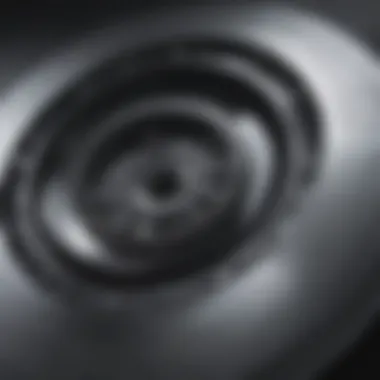

Intro
In the realm of automotive engineering, precision and efficiency are paramount. Understanding the mechanics behind tool applications is crucial. One such tool that stands out for its effectiveness in shaping metal is the sheet metal shrinking disc. This article delves into the intricacies of shrinking discs, crafted specifically for use in the automotive industry. By examining their functionality, materials, and various designs, we aim to paint a thorough picture of their importance in modern vehicle manufacturing and repair.
Shrinking discs facilitate metal shaping by effectively reducing the size of pieces, thereby enabling a more refined fit and structural integrity. Automotive professionals and hobbyists alike benefit from the innovative technology behind these tools. The insights provided will enhance your knowledge about shrinking discs and their pivotal role in automotive crafting.
Automotive Features and Innovations
Overview of Latest Technologies
The automotive industry is continually evolving, and with it, the technologies that support metalworking techniques. Sheet metal shrinking discs have adapted to incorporate advancements that improve their efficiency and versatility. Recent innovations include adjustable designs that allow users to modify shrinking intensity according to the specific requirements of the job. This results in better control over the metal shaping process.
In-Depth Look at Electric/Hybrid Vehicles
The surge in electric and hybrid vehicles has created a unique landscape for automotive metalworking. These vehicles often require specialized components that can benefit from the precision of shrinking discs. As designers focus on lightweight materials to enhance battery efficiency, the application of shrinking discs helps in maintaining the structural integrity of these components, making them essential in modern automotive production.
Analysis of Autonomous Driving Systems
As autonomous driving systems gain traction, the production of vehicles equipped with these technologies demands high-precision metal components. Shrinking discs contribute to refining the shapes of panels and frames, ensuring they align perfectly for the complex systems that govern autonomous features. Precision in these components cannot be overstatedโit is critical for safety and performance.
Evaluation of AI in Automotive Solutions
Artificial intelligence is making waves in various sectors, including automotive manufacturing. The integration of AI can streamline the processes surrounding metal working with shrinking discs. AI algorithms can analyze and adjust the parameters of shrinking operations for optimal results. This results in enhanced accuracy and reduction in material waste, contributing to more sustainable manufacturing practices.
Understanding Shrinking Discs
Sheet metal shrinking discs are crucial for any automotive professional aiming to achieve precision in their work. These tools function using heat and mechanical force, allowing metal fabricators to manipulate sheets of metal with a desired outcome.
"The primary purpose of a shrinking disc is to create a tighter fit among joined components, which is essential for the structural soundness of automotive parts."
Materials and Designs
Different types of materials are utilized in the construction of shrinking discs, including aluminum and high-carbon steel. Each material offers distinct advantages depending on the specific application. When selecting a disc, consider factors like heat resistance and durability. Furthermore, the design varies, including options for different diameters and thicknesses, ensuring compatibility with various metalworking tasks in the automotive field.
Methodologies for Effective Metal Shaping
Several methodologies can be utilized to maximize the effectiveness of shrinking discs. Proper setup and the right technique can make a considerable difference. Itโs necessary to maintain the right temperature and to apply consistent pressure. Familiarity with these methodologies enables automotive professionals to achieve desirable results while reducing the possibility of damage to the metal sheets being worked on.
Prologue to Sheet Metal Shrinking Discs
Sheet metal shrinking discs play a critical role in the automotive sector. Their primary function involves shaping metal panels, essential for both production and repair tasks. Understanding how these discs work enhances the skills of automotive professionals. As automotive technologies evolve, the tools and techniques introduced become vital for achieving high precision in metalworking.
The shrinking process allows metal workers to manipulate the form of the sheet metal. This is particularly valuable when dealing with complex automotive body shapes. Shrinking discs enable the technician to apply localized heating, which allows the metal to contract as it cools. This method is efficient and provides more control compared to traditional methods.
Benefits of using sheet metal shrinking discs include:
- Improved precision: The ability to control the shrinking process minimizes the risk of warping or undesired shapes.
- Enhanced durability: Proper use of shrinking discs can lead to longer-lasting repairs and manufacturing results, particularly in stress-prone areas.
- Versatility in applications: From customizing classic cars to modern vehicles, shrinking discs offer adaptability across various projects.
In the context of automotive applications, a profound understanding of shrinking discs allows professionals to produce superior results. It is essential to recognize the factors affecting the choice and application of these discs. This knowledge not only improves individual skill but also contributes to the overall quality of automotive craftsmanship. By mastering these tools, professionals can address structural challenges effectively and efficiently.
The Mechanics of Metal Shaping
Understanding the mechanics of metal shaping is crucial for anyone involved in automotive applications. This section outlines how these mechanics relate specifically to sheet metal shrinking discs. The shaping of metal involves various processes and techniques that manipulate the material into desired forms and dimensions. This not only enhances the aesthetic value of automotive parts but also ensures their functionality.
The importance of mastering metal shaping cannot be overstated. Proper knowledge of shaping techniques leads to improved precision and accuracy in fabrication. This is essential for automotive manufacturers who aim for high-quality vehicle production. It reduces the risk of defects, which can cost time and resources.
Overview of Sheet Metal Working
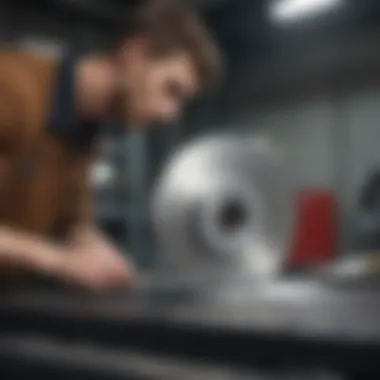

Sheet metal working encompasses a wide range of methods and processes designed to produce parts from thin metal sheets. Primarily, these parts are integral to the structure and design of automotive components. Various techniques are employed in the process, including cutting, bending, and forming. Each of these methods plays a pivotal role in transforming flat sheets into complex shapes required for different automotive applications.
A significant advantage of sheet metal working is its versatility. Technicians can create components such as body panels, frames, and even intricate ductwork for HVAC systems in vehicles. Moreover, with the rise of advanced machines, such as CNC (computer numerical control) machines, the precision of cuts and bends has greatly improved, allowing for tighter tolerances and better fitment in vehicles.
Key Techniques Used in Metal Fabrication
Several key techniques are employed in metal fabrication overall, particularly when working with sheet metal. These include:
- Cutting: This can be done using shears, lasers, or plasma cutters. The choice of method often depends on the material thickness and the desired edge quality.
- Bending: Using brakes, technicians can bend metal sheets into specific angles. This is crucial for parts requiring precise geometries, particularly in automotive bodies.
- Forming: Techniques such as stamping or deep drawing allow for the creation of complex shapes. This is essential for producing components like fenders and hoods.
Choosing the right technique is vital for achieving optimal results. Each technique brings unique benefits and drawbacks that can affect both the quality and cost of the final product. Understanding these nuances will empower professionals to make informed decisions during the fabrication process.
Understanding Shrinking Processes
The understanding of sheet metal shrinking processes is crucial in the realm of automotive manufacturing and repair. This topic covers the essential techniques and technology behind reshaping metal efficiently and accurately. Sheet metal shrinking is a vital operation that helps in restoring the shape and integrity of various components, particularly in the automobile sector. By grasping this process, automotive enthusiasts and professionals can appreciate its role in achieving precision and quality in metal crafting.
What is Metal Shrinking?
Metal shrinking is a process that modifies the dimensions of metal sheets without requiring a complete remanufacture. This is typically achieved through methods such as heating and mechanical manipulation. When heat is applied to the metal, it expands. Once it cools down, it contracts back to a smaller size, effectively shrinking the area where the heat was applied. The process is fundamental in correcting over-extensions and dents while allowing for more precise metalworking.
- Key Benefits of Metal Shrinking:
- Enhances precision in vehicle parts during manufacturing or repairs.
- Reduces the risk of further damage to the metal during reshaping.
- Allows for smoother finishes and better fitting of component parts.
Applications of Metal Shrinking in Automotive
In the automotive field, metal shrinking finds various practical applications, highlighting its significance. It is extensively used in the following areas:
- Repair Work: When a vehicle suffers from dents or structural deformation, metal shrinking is essential for restoring the original shape without significant alterations.
- Custom Fabrication: Car enthusiasts often modify their vehicles, making the shrinking process indispensable for fitting aftermarket parts securely.
- Panel Alignment: In the assembly of car panels, metal shrinking ensures that gaps are minimized, which contributes to better aerodynamics and aesthetics.
"Understanding the process of metal shrinking is integral for achieving high-quality results in automotive applications. It provides a pathway to precision that is not often appreciated until witness during a challenging repair."
In summary, a deep awareness of shrinking processes allows automotive professionals and enthusiasts to appreciate the technical skills involved in metalworking. This knowledge contributes to the development of more efficient, reliable, and aesthetically pleasing automotive products.
Components of Sheet Metal Shrinking Discs
Understanding the components of sheet metal shrinking discs is vital for grasping how these tools function within automotive applications. Each component plays a crucial role in ensuring the performance and effectiveness of these discs during metal shaping processes. Here, we will explore various material types used in manufacturing these discs as well as the design variations, providing insight into their implications on functionality and application.
Material Types Used in Manufacturing Discs
Aluminum
Aluminum is a favored choice for manufacturing shrinking discs due to its lightweight nature. It allows for easier handling and manipulation. One of the main characteristics of aluminum is its excellent thermal conductivity, which aids in efficient heat dissipation during the metal shrinking process. This trait makes aluminum discs beneficial in automotive settings, as they can quickly cool after use, reducing warping or damage.
However, while aluminum is effective, it does have some vulnerabilities. It is softer than other metals, which means it can wear down faster in high-stress applications. This characteristic makes careful use and occasional replacement necessary to maintain the desired performance.
Steel
Steel offers robustness that aluminum does not possess. It is known for its high tensile strength, making it highly resistant to deformation during metal shaping. This key characteristic allows steel discs to accommodate more intense applications without significant wear. Automotive professionals appreciate this durability, reflecting steel's long-lasting value in manufacturing.
One unique feature of steel is its ability to withstand high temperatures without a substantial increase in brittleness. This advantage makes steel a preferred option for projects involving substantial heating during the shrinking process. However, steel discs can be heavier than their aluminum counterparts, potentially making handling slightly more cumbersome in some settings.
Composite Materials
Composite materials are emerging as an innovative choice for shrinking discs. Their main advantage lies in the combination of different materials, resulting in specific desired properties. This adaptability allows manufacturers to tailor discs for specific automotive applications, balancing weight, durability, and thermal resistance.
A notable characteristic of composite materials is their resistance to corrosion, enhancing their lifespan in settings where moisture and chemicals may be present. This aspect makes them particularly advantageous for automotive work, where exposure to various substances is common. However, the cost of composite discs can be higher, which may lead some users to consider them less favorable for more general applications.
Design Variations and Their Implications


Design variations in shrinking discs are essential for addressing specific metalworking needs. Different shapes, thicknesses, and surface textures of discs can influence how effectively they perform in various situations.
For instance, varying the thickness can alter the discโs stability and heat retention. Thicker discs may offer more stability at high temperatures, while thinner options may provide quicker cooling but can be prone to warping. Each design decision has practical implications for users, affecting their choice based on the specific requirements of the automotive project.
In summary, understanding the components of sheet metal shrinking discs helps users make informed choices in their applications. The selection of materials like aluminum, steel, and composite options plays a significant role in both functionality and outcome in automotive contexts. Similarly, the impact of design variations cannot be overlooked, as they dictate the suitability of a disc for a particular task. This knowledge empowers automotive professionals to choose the right tools for optimal results in their metal shaping processes.
Advantages of Using Shrinking Discs
The use of shrinking discs is pivotal in achieving high-quality metal shaping in automotive applications. Shrinking discs allows technicians to operate with increased precision and ensure the integrity of the metalwork. Below are key factors that demonstrate the significance of adopting shrinking discs in automotive tasks.
Precision in Metal Shaping
Shrinking discs provide an exceptional level of control during the metal shaping process. This precision is crucial for achieving the desired contours and forms needed in automotive parts. When executed correctly, the shrinking process allows for minimal distortion of the metal. This is especially important when working with panels that require exact fitting to avoid gaps or misalignments.
Using shrinking discs can greatly enhance the technicianโs ability to mold metal consistently. It allows for adjustments on the fly, something that is vital in automotive repair and custom fabrication. In essence, these discs empower users to navigate complex shapes without compromising structural integrity.
Reduction of Dents and Imperfections
One of the most tangible benefits of using shrinking discs is the reduction of dents and surface imperfections. When metal is improperly shaped or manipulated, it often results in defects that are costly and time-consuming to fix. Shrinking discs effectively alleviate this issue, allowing for a smoother finish that enhances the overall visual appeal of the finished product.
Impurities or imperfections can easily be addressed with the application of shrinking discs by precisely shrinking specific areas. The result of this meticulous process is not just aesthetically pleasing but also improves the lifespan of the automotive component. Automotive professionals appreciate that tools like shrinking discs can reduce rework, ensuring efficiency in their workflows.
"Using shrinking discs significantly elevates the quality of metalwork, minimizing flaws that could result from traditional methods."
Overall, integrating the use of shrinking discs in automotive tasks positions professionals to deliver superior metalwork that not only meets but exceeds industry standards.
Choosing the Right Shrinking Disc
Choosing the right shrinking disc is critical in achieving optimal results in automotive applications. The right disc can influence the quality of metal shaping, impact the efficiency of tasks, and determine the overall outcome of vehicle manufacturing or repair. Therefore, understanding the factors affecting disc selection plays a vital role for automotive professionals and enthusiasts alike.
Factors to Consider in Selection
When selecting a shrinking disc, several factors must be considered to ensure that it aligns with the specific needs of the project. The following are key elements to take into account:
- Material Compatibility: The disc's material must be suitable for the type of metal being worked on. For instance, an aluminum disc may be more suitable for lightweight car panels, while a steel disc is preferred for heavier components.
- Disc Size: The size of the disc is crucial for achieving the desired results. A larger disc may provide a wider working surface, thus offering quicker coverage, while smaller discs may allow for more precision in tight areas.
- Grinding Grit: The grit of the disc impacts the level of abrasiveness. Finer grits offer smoother finishes, while coarser grits excel in hastening the shaping process. It is important to choose a grit that matches the stage of metal shaping.
- Brand Reliability: Different manufacturers offer varying levels of quality. Researching and selecting trusted brands can enhance durability and performance, reducing the risk of having to replace discs frequently.
Cost vs. Value Assessment
Another significant aspect in selecting shrinking discs is the cost versus value assessment. It is essential to evaluate whether a higher price point translates to better quality and results or if affordable options could suffice without compromising effectiveness.
- Initial Costs vs. Long-Term Benefits: While premium discs may come with a higher initial cost, they might offer advantages such as longevity and superior performance. This choice reduces replacement frequency and may ultimately prove more cost-effective over time.
- Performance Metrics: Evaluating how well a disc performs under pressure and its effectiveness in different applications is key. Discs that consistently produce high-quality results, even on challenging metals, can justify a higher price.
- User Experience: Recommendations from fellow mechanics and metalworkers can provide insights into whether a disc's cost aligns with performance. Online platforms like Reddit often have threads discussing personal experiences with various brands and products.
Choosing the right shrinking disc is not merely a matter of price. It is about balancing quality, performance, and costs to achieve optimal results in a variety of automotive applications.
Proper Usage of Shrinking Discs
Understanding how to properly use shrinking discs is crucial for anyone involved in automotive metalwork. Using these tools correctly not only ensures better results, but it also minimizes the risk of damaging the metal being worked on or the disc itself. Proper usage practices contribute to the precision and efficiency that automotive professionals strive to attain in their projects.
Essential Techniques for Effective Application
When employing shrinking discs, there are specific techniques that can enhance effectiveness. First, ensure the metal is clean and free of any contaminants. Dirt or grease can interfere with the shrinking process and lead to uneven results.
Maintain a steady speed while operating the disc. A constant motion allows for even distribution of heat. If working on an area needing significant shrinkage, do so in small increments. This gradual approach prevents overheating, which can warp the metal. Also, use light pressure initially. Too much force can lead to excessive wear on the disc or cause damage to the metal.
A preferred technique is using a circular motion, which helps in distributing heat uniformly across the surface. Remember to cool the metal periodically. This practice ensures the integrity of the metal is maintained and avoids any thermal shock.
Common Mistakes and How to Avoid Them
Despite the apparent simplicity of using shrinking discs, mistakes are common. One prevalent error is proceeding without evaluating the type of metal involved. Different metals have varied heat tolerances and reaction rates. For instance, aluminum requires less heat than steel. Knowing the metal type can dictate the application of shrinking techniques.
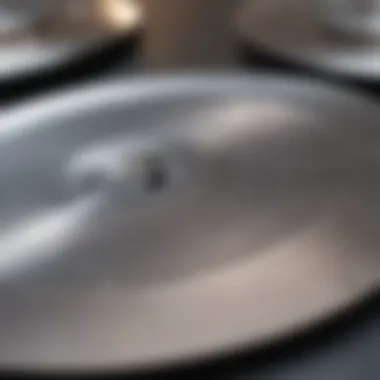

Another mistake is neglecting to check the discโs condition before use. A worn-out or damaged disc will perform poorly, leading to unsatisfactory results. Always inspect the disc for cracks or any signs of excessive wear. If defects are found, replace the disc before commencing work.
A frequent oversight is using the disc at incorrect speeds. Operating too slowly can cause overheating, while going too fast can lead to inadequate metal shaping. Finding a balance is crucial.
To summarize, effective use of shrinking discs depends on proper metal preparations, consistent techniques, and avoiding common mistakes. With diligence, one can harness these tools for optimal metalworking results.
Maintenance of Shrinking Discs
The maintenance of shrinking discs is crucial for ensuring their longevity and performance in metalworking applications, especially in automotive settings. By regularly maintaining these tools, users can prevent excessive wear, promote safety, and extend the life of the discs. Neglected maintenance can lead to decreased effectiveness and may also result in faulty repairs or defects in the vehicles being worked on. This segment will discuss how to keep shrinking discs in optimal condition and signs indicating a need for replacement.
How to Maintain Your Discs
Maintaining shrinking discs involves a series of straightforward yet essential practices. Here are some effective maintenance steps to follow:
- Cleaning: After each use, ensure you clean the disc thoroughly. Debris, metal shavings, and other contaminants can affect performance. Use a soft brush or a damp cloth to remove residue and avoid using harsh chemicals that could damage the material.
- Inspection: Frequently inspect the disc for any signs of damage or wear. Look for cracks, warps, or signs of excessive wear. Identifying problems early can prevent further deterioration and save time and resources in the long run.
- Storage: Store the discs in a clean, dry environment. Avoid areas with high humidity as moisture can lead to rust, especially on steel discs. Use protective covers to shield the discs from dust and damage during storage.
- Lubrication: For certain types of discs, a light lubricant may be beneficial. This step helps minimize friction and can enhance the disc's effectiveness when in use. Always refer to the manufacturer's guidelines on the type of lubricant suitable for the specific disc.
Maintaining shrinking discs is not just about keeping the tools clean. It is about fostering a proactive approach to ensuring their efficiency and reliability during use.
Signs of Wear and When to Replace
Recognizing when a shrinking disc needs replacement is critical for maintaining safety and efficiency in automotive work. Below are common signs of wear:
- Visible Damage: Inspect for any cracks or uneven surfaces. These can compromise its performance.
- Decreased Effectiveness: If you notice that the disc is no longer efficiently shrinking metal, it might be time for a replacement. This includes longer time taken to achieve desired shapes or inconsistencies in the final product.
- Discoloration: Overheating can cause discoloration, which indicates that the disc has sustained damage. This may reduce its effectiveness.
- Excessive Noise: Unusual sounds during operation can be a sign that something is wrong. Pay attention to any grinding or screeching, which could indicate improper alignment or severe wear.
Remember: Regular inspections and maintenance not only save time and money but also improve your overall metalworking results.
When you observe such indicators, it is advisable to replace the disc promptly. Investing in new discs is essential to maintain the quality of work and avoid potential accidents that could arise from using damaged or ineffective tools.
Future Trends in Metal Fabrication Tools
The automotive industry is in constant evolution, and the tools used in metal fabrication are no exception. Understanding future trends in metal fabrication tools is crucial for automotive professionals and enthusiasts. These trends not only enhance the quality of work but also streamline the processes involved in vehicle manufacturing and repairs. In this context, two significant areas will be discussed: advancements in material technology and the integration of automation in metalworking.
Advancements in Material Technology
Material technology is a cornerstone of innovation in the automotive sector. New alloys and composite materials are being developed, offering improved strength-to-weight ratios. Lightweight materials such as carbon fiber and advanced aluminum alloys are gaining prominence. These materials are beneficial, as they contribute to the efficiency of vehicles by reducing overall weight and enhancing fuel economy. Additionally, these materials exhibit better durability in various environmental conditions, which is essential for automotive applications.
The development of materials that can withstand extreme temperatures and mechanical stresses is a game changer. For example, high-strength steel allows for thinner panels without compromising structural integrity. This not only simplifies the manufacturing process but also decreases material costs. With the rise of sustainable practices, there's also a push for recyclable materials, which aligns the manufacturing processes with environmental responsibility.
Integration of Automation in Metalworking
Automation is reshaping the landscape of metalworking in the automotive industry. Tools and processes that once required manual effort are now becoming automated. This shift improves precision, speeds up production times, and reduces human error. Modern metalworking tools, including shrinking discs, are increasingly integrated with robotic systems and CNC technology. This integration facilitates a level of repeatability that is hard to achieve by hand.
The use of automated inspection systems ensures quality control throughout the fabrication process. With technologies like 3D scanning, flaws can be detected early, preventing costly mistakes. Furthermore, automation allows for flexible manufacturing setups. Artists and engineers can quickly adapt to different designs without a significant loss in productivity.
In summary, understanding future trends in metal fabrication tools is essential for staying ahead in the automotive industry. Advancements in material technology and the integration of automation in metalworking are shaping a future where efficiency and quality take precedence. As these trends develop, they promise to refine the processes and materials used in vehicle production and repair, benefiting professionals and enthusiasts alike.
Finale
In this article, we delve into the intricacies of sheet metal shrinking discs and their critical role in automotive applications. Understanding these tools is important for automotive professionals, hobbyists, and students in the field.
Sheet metal shrinking discs offer various benefits that can directly impact the quality of work. These tools help in achieving precision metal shaping, allowing users to create components that fit perfectly into modern vehicles. Moreover, the reduction of dents and imperfections that these discs offer cannot be overstated. When working on automotive projects, both aesthetics and functionality matter, and shrinking discs can significantly enhance both aspects.
Considerations about the selection and proper usage of shrinking discs were pivotal in our discussion. Selecting the right disc is not merely a matter of cost; it involves assessing the specific needs of a project and acknowledging the materials in use. Effective techniques for application and maintenance are essential as well. Users must be aware of signs of wear and know when to replace their tools to maintain optimal performance.
Lastly, understanding current and future trends in metal fabrication tools is necessary. As technology grows, so does the efficiency of tools such as shrinking discs. Tracking these developments is essential for anyone serious about automotive work. Innovations in materials and automation can lead to safer and more efficient metal shaping processes.
In summary, the knowledge shared in this article about sheet metal shrinking discs can empower automotive enthusiasts and professionals, leading to improved outcomes in metalworking tasks. The value of investing time to understand these tools will reflect in the quality and effectiveness of future automotive projects.
Importance of References in the Context of This Article
- Establishing Credibility: References from reputable sources such as en.wikipedia.org and britannica.com lend authority to the information presented. When readers see citations from well-established platforms, they are more likely to trust the material. This is particularly important in technical fields, where precision and accuracy are vital.
- Guiding Further Research: Providing references acts as a roadmap for readers interested in delving deeper into specific topics. For example, mentioning materials science literature or industry standards will allow automotive professionals to further enhance their knowledge and skills concerning shrinking discs.
- Supporting Claims: Any assertions made throughout the article regarding material properties, effective techniques, or advancements in technology need backing. Using data from trusted references helps ensure that the claims are not only factual but also represent a consensus in the industry.
- Encouraging Critical Thinking: By including varied sources, readers can engage in comparative analysis. They can evaluate multiple perspectives on sheet metal shaping techniques or emerging trends in manufacturing tools, thereby fostering a more comprehensive understanding of the subject matter.
Specific Elements of References to Consider
- Current Trends: Referencing recent studies or industry reports can highlight ongoing trends in sheet metal working, making the article relevant to modern practices.
- Historical Context: Occasionally, including references to historical advancements in metalworking technologies can illustrate how practices and tools have evolved over time.
- Technical Standards: Citing documents related to technical standards in metal manufacturing provides readers with crucial guidelines ensuring safety and efficiency in their own practices.